Continuous manufacturing method used to make generic lomustine
Posted: 8 March 2019 | Nikki Withers (European Pharmaceutical Review) | No comments yet
The goal is to improve manufacturing flexibility, enhance quality and uniformity, while lowering the costs for patients…
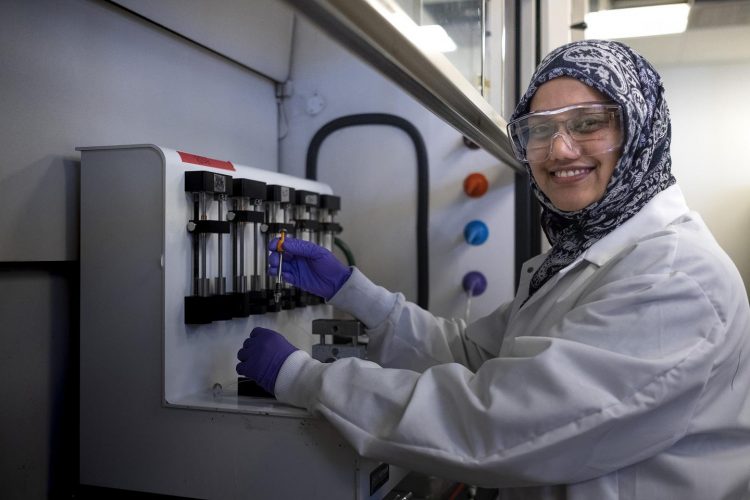
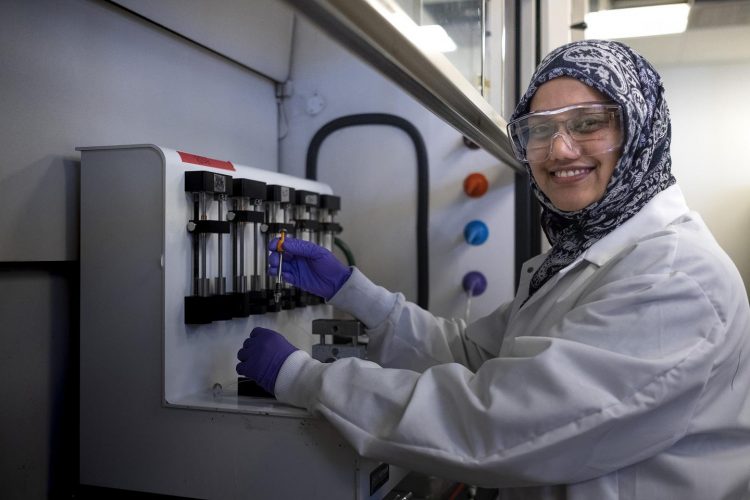
Researchers at Purdue University have developed an innovative and cost-effective continuous manufacturing method to make generic lomustine.
The team synthesised lomustine – an important agent for treatment of brain tumours and Hodgkin’s lymphoma – using continuous flow methodology, and it is thought the approach could be applied to other products.
“Desorption electrospray ionisation mass spectrometry (DESI-MS) was used to quickly explore a large number of reaction conditions for one of the reaction steps and guide the efficient translation of optimised conditions to continuous lomustine production,” write the authors in Organic Process Research and Development.
“Using only four inexpensive commercially available starting materials and a total residence time of nine minutes, lomustine was prepared via a linear sequence of two chemical reactions performed separately in two telescoped flow reactors.”
The Food and Drug Administration (FDA) wants the pharmaceutical industry to get away from making drugs using the traditional batch method and switch to continuous manufacturing.
In February, the FDA put out a statement saying the continuous process allows manufacturers to more easily scale operations to meet demand and should help reduce drug shortages. The statement also said continuous manufacturing can provide a more robust, lower cost and diverse supply of drug products.
Professor David Thompson, from Purdue’s Department of Chemistry and a member of the Purdue University Center for Cancer Research, began working on applying his continuous manufacturing process for lomustine after reading an article written by Dr Henry Friedman, a neuro-oncologist from Duke University, about how the cost of lomustine had risen dramatically.
His aim was to make lomustine quickly and cheaply, and within six months, Thompson’s team developed a method to make lomustine at a rate equivalent to one dose every two hours using continuous manufacture. His group is now developing methods to scale up the production rate.
“All of this is happening in a space that is the size of a small desk. A very small footprint,” Thompson said.