The Falsified Medicines Directive: steps to compliance
Posted: 16 January 2019 | European Pharmaceutical Review | No comments yet
As the date of implementing the FMD comes closer, organisations need to be ensuring compliance, whether in the EU or even after a possible no-deal Brexit…
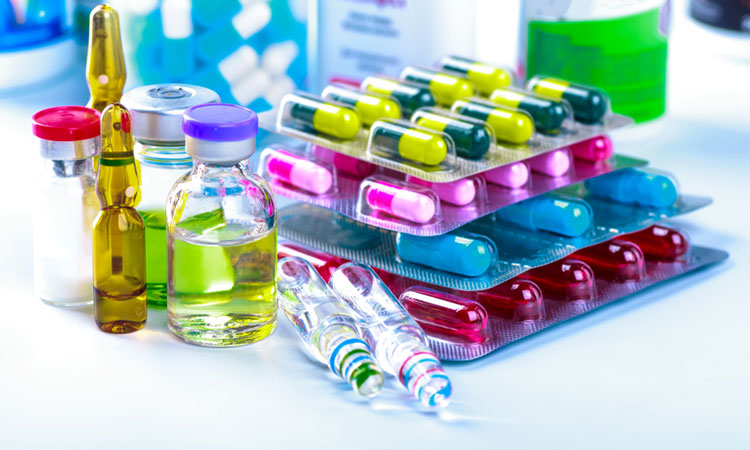
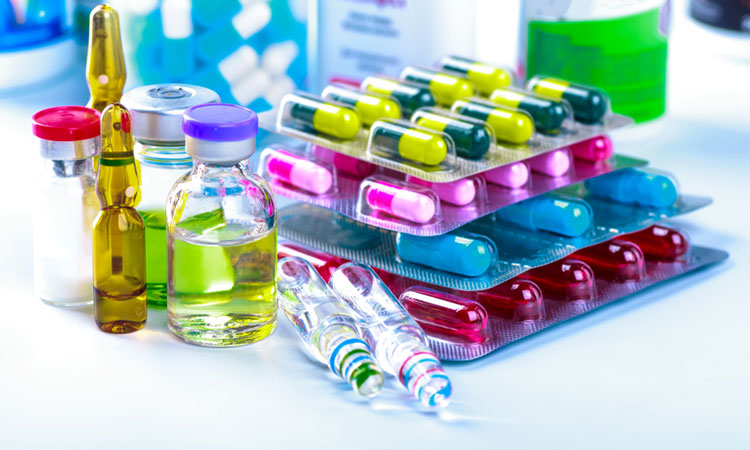
The Falsified Medicines Directive (FMD) 2011/62/EU, comes into full force on the 9th February 2019.
This directive aims to increase the security of the manufacturing process and delivery of medicines throughout Europe, providing greater protection for patients. Organisations that have not yet become compliant must now act fast to ensure they do not fall foul of the regulation.
The MHRA have also confirmed that should there be a ‘no-deal’ Brexit, it will consider a UK-only version of the EU law.
So, what can be done to make sure FMD compliance projects are completed in time and that the chosen solutions are robust enough to guarantee immediate compliance? Christian Taylor, Serialisation Business Consultant at Zetes, provides his plan to becoming FMD compliant.
Review existing processes
With the legalisation fast approaching, there is more urgency to find suitable solutions. However, as FMD compliance needs to be built into day-to-day operations, it requires a careful and considered process review.
Organisations should proactively be looking to implement solutions that create minimum disruption to current working processes, drive efficiencies and are simple to use every day. Operational team engagement in the plan is needed if businesses are to achieve full compliance and effective delivery. This, along with a well-managed implementation, that is supported by solid training and open communications, will also result in a rapid launch.
Frame projects
Organisations not only need to focus on making sure they have compliance ahead of the 9th February, but they also need to ensure that any FMD solutions that are implemented are built on flexible foundations. This flexibility will arm them with the ability to encompass broader roadmap principles such as automation for decommissioning, returns, consolidation and aggregation or adding a visibility layer for reporting and insight beyond the audit trail.
Examining the flexibility that an FMD solution can provide will allow businesses to think big, start small, scale fast and have a platform for growth in the future.
Furthermore, Good Distribution Practice (GDP) requires the capturing and storing of batch-level information. Whereas, FMD requires organisations to capture and share item level serialised data. Businesses, therefore, need to identify datasets, sources and recipients. This will be vital in ensuring future scalability, including the ability to consolidate, aggregate products and data and share this information in real time to enable other parties to mass decommission if needed.
Consider technology
Technology can play a key role in error reduction. The choice of technology is largely based on the volume throughput and the environment for capturing data. Large scale operations need to weigh up the value of manual scanning against semi-automated and fully automated options to ensure high accuracy for higher throughput volumes. Smaller scale operations may be able to get by with basic handheld devices but they must have operational procedures and process controls in place that are robust enough to ensure accuracy.
Regardless of its size, an organisation should try to avoid serialisation systems that are heavily reliant on a specific hardware or software. Such restraints could restrict its ability to take advantage of any new processes or technology without having to re-implement a whole new project further down the line.
The combination of people and technology
The successful deployment of an FMD solution requires the buy-in of not only compliance teams and the IT department but businesses should also consider wider operational teams and those using the solution day-to-day. It’s vital that any solution fits within the business environment.
Operational staff should also be made aware of the implications of FMD, however, organisations shouldn’t find themselves in a situation where an employee on the warehouse floor is making decisions that affect the legal standing of the business. Instead, it should ensure that users are armed with the most appropriate technology that helps with compliance.
Add value to the business
Typically, compliance is viewed as a business pain and something that is unlikely to create direct value. By implementing a solution that can optimise supply chains, update data flows, break down operational silos and enable tighter internal and external collaboration, substantial value will be unlocked.
Additionally, adding automation and digitising messages to complement the physical flow of the supply chain, will not only increase efficiency and reduce errors but also provide greater actionable insight to optimise the future process, while providing early alerts of any potential risks.
Related topics
Manufacturing, Regulation & Legislation, Research & Development (R&D)