Novel design proposed for aseptic processing areas
Posted: 3 April 2025 | Catherine Eckford (European Pharmaceutical Review) | No comments yet
The approach offers key benefits such as facilitating a reduction in the risk of microbial contamination and reduction in the required air change rate in aseptic processing.
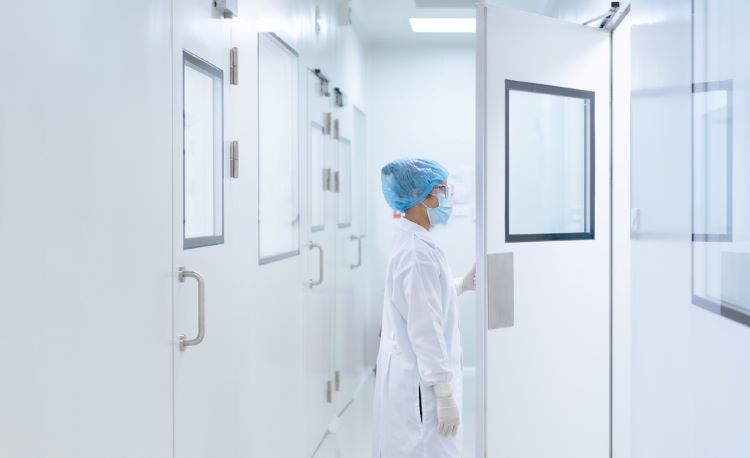
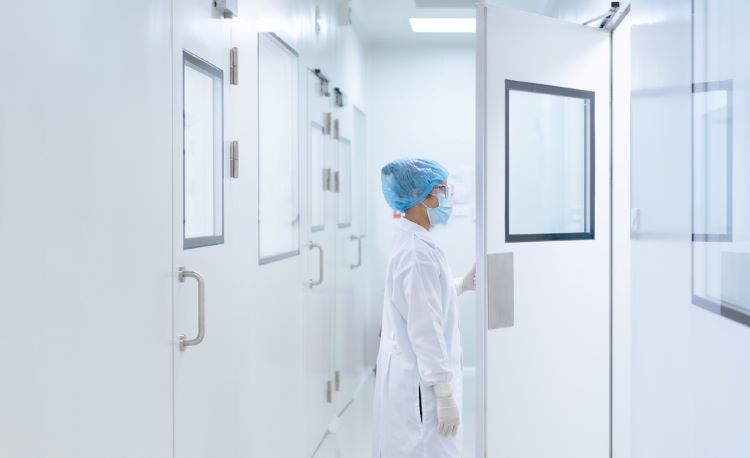
A novel design approach could improve aseptic processing for cell therapy manufacturing, research suggests.
In their Regenerative Therapy paper, Furomitsu et al. proposed an environment by designing an air mass balance in an aseptic processing area.
The approach used open and closed system equipment consisting of critical processing zones, such as biosafety cabinets and isolator systems.
Separate research published in a paper last year on particle monitoring in biosafety cabinets, demonstrated that “the number of particles and falling bacteria varied depending on the type of clothing.” For example, the authors suggested that the data could be used to identify risks in aseptic manufacturing areas.
In the present research, the proposed space consisted of three zones: critical processing zone and a support zone, the latter being divided into two upper and lower vertical zones, the researchers explained. The support zone was based on airflow and location of the particle emission sources.
The team developed a kinetic model for particle concentration to describe the impact of airflow rate on the cleanliness of the aseptic processing area.
Potential of the design approach for aseptic processing
designing an environment divided regionally can realise cell manufacturing in an [aseptic processing area]”
Based on the findings of their study, the authors stated that the “appropriate location of the air inlet and outlet can construct the cleanliness of the aseptic processing area, which reduces the risk of microbial contamination”.
Furomitsu et al. concluded that “designing an environment divided regionally can realise cell manufacturing in an [aseptic processing area], which eliminates the need for an air duct connected to the equipment from outside the cleanroom, reduces the air change rate, and allows for a more simplified gowning of operators”.
Importance of aseptic connections in manufacturing
As the industry transitions to “more precise processing for biologics or advanced therapy medicinal products (ATMPs) manual aseptic connections will become more crucial in meeting critical process parameters for microbiological quality,” according to Vanessa Vasadi Figueroa.