Innovative framework could enhance process efficiency in manufacturing quality control
Posted: 1 April 2025 | Catherine Eckford (European Pharmaceutical Review) | No comments yet
The proposed approach demonstrates benefit for real-world application, establishing more robust, adaptive, and economical process systems, the research suggests.
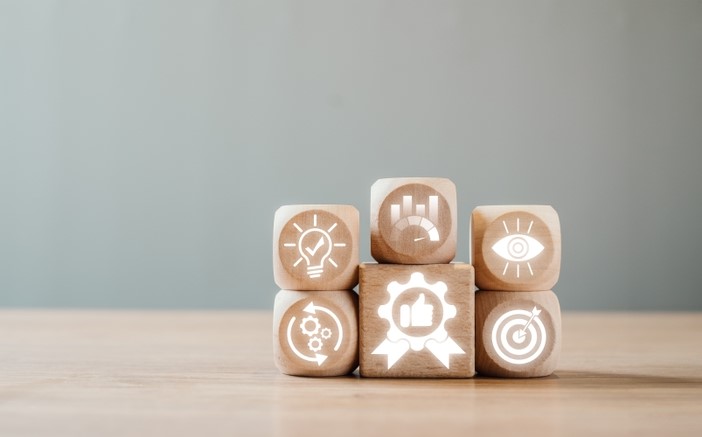
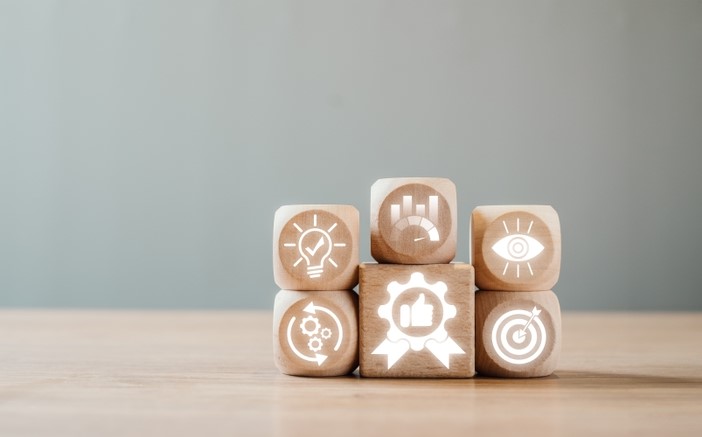
Researchers have demonstrated a novel framework that supports the advancement of quality control in manufacturing.
Current quality control strategies are often inefficient for large process uncertainties, as they often do not provide the flexibility necessary, due to a reliance on set-point control, Kay et al. explained.
This therefore raises “a clear need for more advanced and robust optimal control strategies to maintain product quality”.
They reasoned that flexibility must be considered not just as reliable set-points, but as “reliable operational spaces which provide greater flexibility to the manufacturing operation”.
Yet the proposed approach enables optimal performance across the entire design space. This is done by combining optimal and flexible design space identification with dynamic optimisation under uncertainty. In their paper, Kay et al. detail the first case study assessing the effectiveness of the technique for formulation.
Optimising quality control processes in manufacturing
The authors highlighted that optimised process flow diagrams are needed to address several challenges, such as inefficiency, reducing waste, and enhancing operational flexibility. This supports competitiveness and overcoming greater demand on sustainability measures.
Specifically, the study utilised a dynamic operational space, “robust to parameter uncertainties” for shelf temperature and chamber pressure. The team found it to be more economical and that it enables a decrease in drying times.
Additionally, by combining machine learning based clustering algorithms with dynamic optimisation within a real-world formulation process, the researchers showed that operational spaces were “optimal, flexible and reliable, [enabling] reduced batch times and energy consumption”.
[Overall, the framework] can facilitate economically advantageous process designs and reliable operational strategies that adhere to critical process constraints and key product quality”
Other benefits of flexible operating spaces were also described. For example, the ability to overcome key challenges around “implementing real-time product quality control and monitoring and precisely maintaining predefined state set-points”.
The study indicates that the framework can effectively manage real-world uncertainties, “yielding economically advantageous process designs and reliable operational strategies that adhere to critical process constraints and key product quality”, according to Kay et al.
The proposed operational space control framework represents a “pioneering more robust, adaptive, and economically viable process systems in industries facing increasing demands for sustainability, efficiency, and product quality”.
The paper was published in Chemical Engineering Science.