Greener method for ethylene oxide manufacture identified
Posted: 25 February 2025 | Catherine Eckford (European Pharmaceutical Review) | No comments yet
The cleaner method could significantly lower production costs and reduce carbon dioxide emissions resulting from ethylene oxide manufacturing.
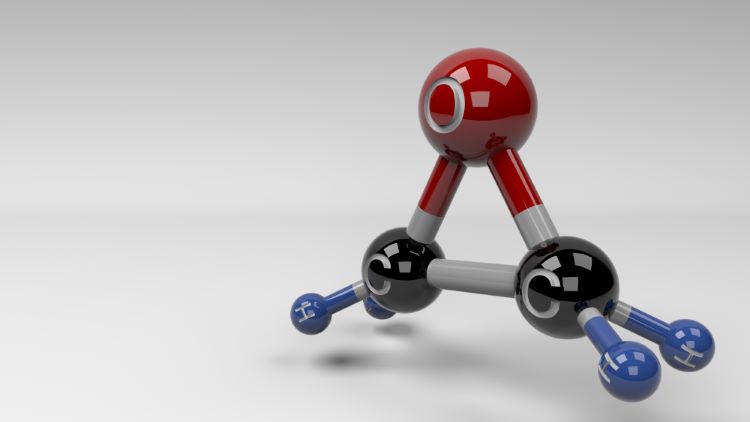
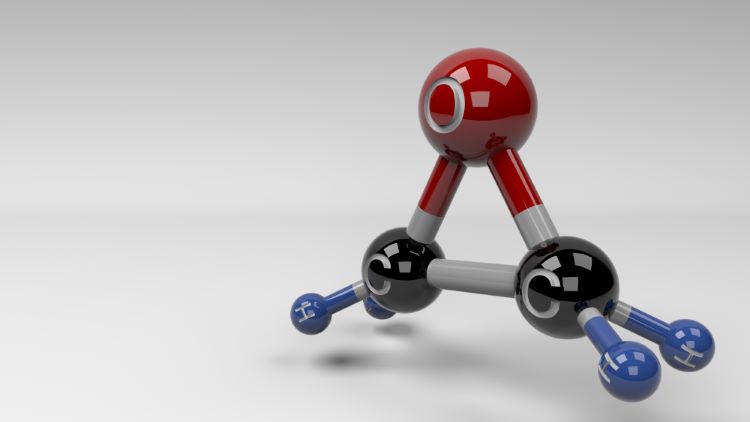
Scientists have developed a new, potentially safer method to produce ethylene oxide. Based on the proposed technique, adding small amounts of nickel atoms to silver catalysts can maintain production efficiency while eliminating the need for chlorine, leading to a reduced environmental impact for ethylene oxide manufacturing.
What sparked this development?
Tulane University chemical engineer Matthew Montemore theorised that the single-atom alloy concept developed by Tufts University chemistry professor Charles Sykes may be applicable to oxidation reactions.
Positively, the researchers were able to overcome the technical challenge of developing a method that incorporated nickel atoms into the silver catalyst.
“[Jalil et al.] showed that nickel dopants on silver could activate molecular oxygen, and surface science experiments showed that nickel could stabilize nucleophilic oxygen that would otherwise react unselectively. Parts per million addition of nickel enhanced selectivity by 25%, and added chlorine could also boost the effect of nickel by an additional 10%,” explained the paper’s editor, published in Science.
Current ethylene oxide manufacturing methods
“[the research showed that]… adding small amounts of nickel atoms to silver catalysts can maintain [ethylene oxide] production efficiency while eliminating the need for chlorine”
Jalil et al. noted that at present, ethylene oxide production processes typically generate “two molecules of carbon dioxide per ethylene oxide molecule. Adding chlorine improves this ratio to about two molecules of ethylene oxide per carbon dioxide molecule. The new nickel-enhanced catalyst could potentially reduce these emissions further while eliminating the need for toxic chlorine in the process”.
“If industry does try this out and they find it to be useful and are able to commercialise it, the twin benefits are you can save a lot of CO2 and a lot of money at the same time,” Montemore added.
Having identified the potential of the new approach, the team are in the process of filing a patent for their finding and in talks about incorporating the technology into existing manufacturing facilities.
Related topics
Data Analysis, Drug Manufacturing, Drug Safety, Industry Insight, Processing, Production, Research & Development (R&D), Sustainability, Technology
Related organisations
Tufts University, Tulane University, University of California Santa Barbara