Semi-automation of manual interventions in high-speed filling lines
Posted: 20 June 2024 | Catherine Eckford (European Pharmaceutical Review) | No comments yet
Research has highlighted the potential of using robotics for isolator filling line interventions, enabling gloveless executions by operators.
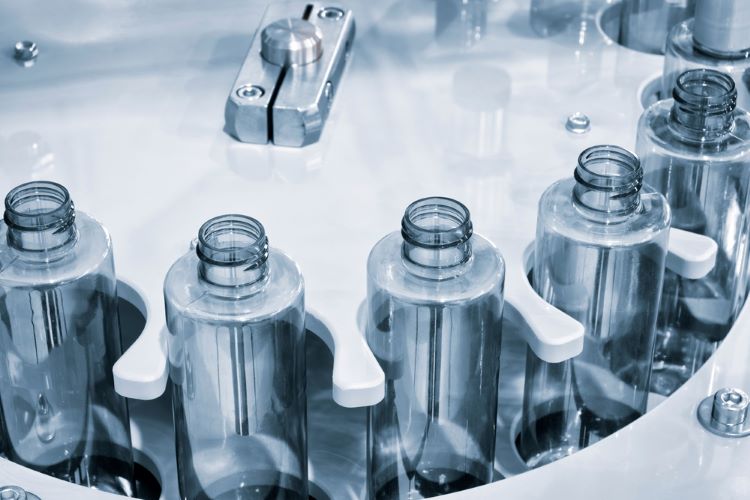
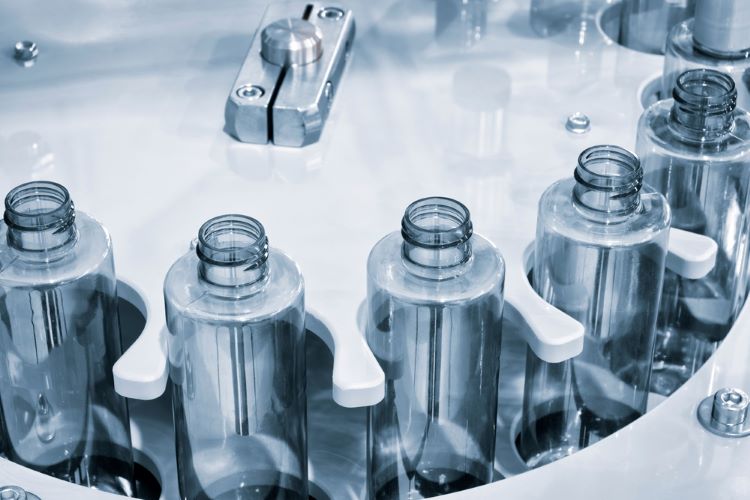
Researchers have developed a novel, gloveless intervention method with remote robotic interventions for high-speed pharmaceutical isolator filling lines.
While these high-speed lines are currently fully automated, Dekker et al. noted that operator interventions are still done manually. For example, a common intervention is the removal of erroneous plungers or stoppers.
Robotic integration
A “major remaining bottleneck” for these automated filling lines is when operators “use of rubber gloves on the side for performing interventions”, Dekker et al. highlighted.
As such, a primary goal of the study was to reduce the downtime of current state-of-the-art isolator filling lines during manufacturing. The authors investigated the applicability of a computer vision algorithm for continuous monitoring of the state of the plunger feed.
They proposed a semi-autonomous intervention strategy for a plunger removal intervention, suggesting that utilising robotics “could increase both the throughput and the sterility of the system”.
Autonomous motion planning for large, general movements, combined with manual teleoperation with system guidance for small, precise motions creates an intuitive, gloveless intervention method, the authors stated.
Beneficially, subject to the robot being validated for inside an aseptic environment, it is part of the entire isolated filling machine, cleaning and maintenance as any other part inside the isolator, the authors explained.
Moreover, because the robot does not need breaks, the authors added that “theoretically”, it could run on a continuous 10-day production batch.
Filling line study results
the static and the dynamic setups provided “a vast improvement in operating time” when compared to the time for the current manual glove-based method (two to three minutes)”
Notably, the static and the dynamic setups provided “a vast improvement in operating time” when compared to the time for the current manual glove-based method (two to three minutes).
According to the findings, time measurements of the user attempts indicated “no significant improvement for subsequent attempts when the plungers are static”.
In contrast, when users found that with dynamic plungers, “the second attempt was significantly faster than the first”.
The authors concluded that this means operators can therefore learn to perform the intervention more efficiently.
A future goal of these filling lines is to “pave the way for full robotic integration in both a fully autonomous and (guided) teleoperative way within future isolator setups, and ultimately the complete removal of gloves”, Dekker et al. anticipated.
The paper was published in the Journal of Pharmaceutical Innovation.