Quality risk management in radiopharmaceutical production
Posted: 28 March 2024 | Catherine Eckford (European Pharmaceutical Review) | No comments yet
A quality risk assessment of a Good Manufacturing Practice (GMP) radiopharmaceutical production site found that dispensing was the most critical phase of the process.
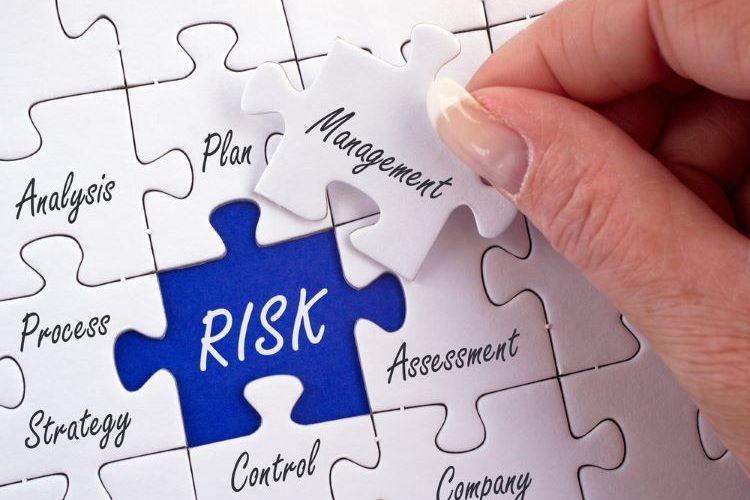
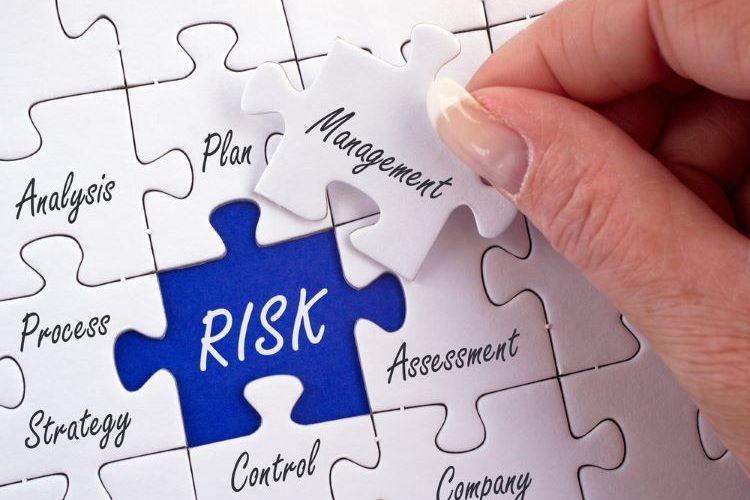
A paper published in Applied Sciences has described a quality risk assessment methodology for application in sterile PET radiopharmaceutical production under Good Manufacturing Practice (GMP) regulations.
According to research highlighted in the paper, applying quality standards such as GMP and ISO 9001 “guarantees the quality and safety of a radiopharmaceutical and contributes to optimising the performance and efficacy of the entire production process.”
As such, the paper by Poli et al. emphasised the importance of having a risk management process for GMP production facilities.
Ensuring radiopharmaceutical quality
Study approach
In the paper, the authors clarified that prior to the current investigation, the production process at the site assessed changed “radically… moving from production with final sterilisation in an autoclave to production using aseptic techniques.”
The quality risk assessment was performed by the research team before the new production process at the site began. Its validity was evaluated by applying it to real data collected over 21 months of production activities of 18F-FDG, the paper stated.
This was done to “confirm whether the critical aspects that previously have been identified in the quality risk assessment were effective.”
As the “most widely used radiopharmaceutical in PET clinical investigations”, the paper suggested that it will still be the most common radiopharmaceutical used in nuclear medicine “for years to come”.
What did the results show?
Compared to the initial quality risk assessment, the evidence collected during the 21 months demonstrated that the method, “adopted both for the assessment of management risks and operational risks, is a suitable tool for identifying the critical phases of the process”, the paper noted.
Based on the findings, production was the most critical phase of the process (asepsis and radioactivity), the authors reported. Specifically, the dispensing phase proved to be the most critical, according to the data. This implies “a delay or even a loss of production along with customer dissatisfaction”.
Poli et al. concluded that the proposed method “could be used by other similar radiopharmaceutical production sites “to identify the critical phases of the production process and to act to improve performance and prevent failure in the entire cycle of radiopharmaceutical products.”
Related topics
Anti-Cancer Therapeutics, Drug Safety, Good Manufacturing Practice (GMP), Production, QA/QC, Therapeutics