Pioneering PAT to improve gene therapy AAV manufacture
Posted: 11 September 2023 | Catherine Eckford (European Pharmaceutical Review) | No comments yet
The CGT Catapult and two other collaborators have agreed to work together and use advanced process analytical technologies (PAT) to improve the process and efficiency of gene therapy AAV manufacturing.
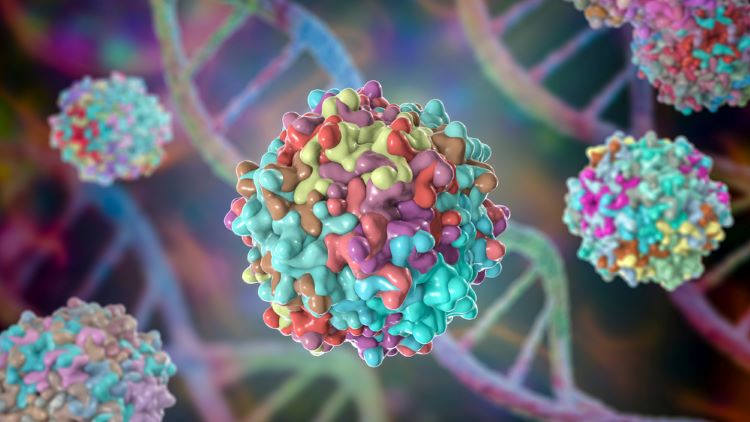
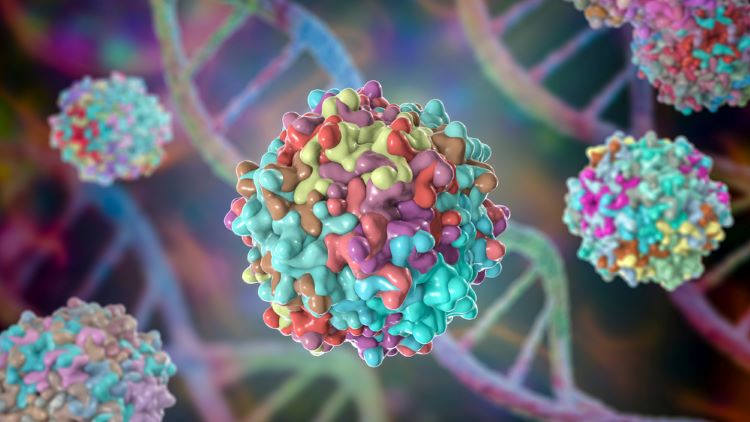
The Cell and Gene Therapy Catapult (CGT Catapult) is set to improve the process and efficiency of AAV manufacture for gene therapies as part of a two-year project alongside two other organisations. CGT Catapult will partner with contract development and manufacturing organisation (CDMO) Rentschler Biopharma and Refeyn Ltd to improve the process of manufacturing adeno-associated viruses (AAV) through automated and digital process analytical technologies (PAT).
Although over 65 percent of gene therapies in development currently are based on AAV, the production is challenging and time-intensive. This is partly because current analytical methods usually use manual sampling.
What will the PAT project involve?
The new PAT project aims develop an automated gene therapy manufacturing platform. The system will be applied to Rentschler Biopharma’s existing AAV manufacturing process.
High throughput and automated sampling and analysis of AAV material will be undertaken. The data obtained will be leveraged to create digital twins, leading to initial tests of any changes to the process in a digital environment. A key benefit of this process is that it should reduce the number of physical tests that are required to be conducted in the laboratory.
The collaborators will assess any improvements in productivity and AAV yield using automated analytical technologies.
“We expect the collaboration to make a significant contribution to enhanced manufacturing capability for the industry,” stated Matthew Durdy, Chief Executive of the Cell and Gene Therapy Catapult.
Potential outcomes for gene therapy manufacturing
The potential of faster viral vector development with multi-parameter driven optimisation “promises to translate to higher outputs, robustness and better process control; ultimately lowering the risk associated with the transition from early to late-stage manufacturing,” declared Dr Christian Schetter, Chief Scientific Officer of Rentschler Biopharma.
The PAT project is financed through a ‘Digitalisation and automation of medicines R&D and manufacture’ grant from Innovate UK.
Related topics
Analytical techniques, Biopharmaceuticals, Drug Development, Drug Manufacturing, Gene therapy, High Throughput Chemistry (HTC), HTS (High Throughput Screening), Industry Insight, Lab Automation, Manufacturing, Process Analytical Technologies (PAT), Research & Development (R&D), Technology
Related organisations
Cell and Gene Therapy Catapult, Cell and Gene Therapy Catapult (CGTC), Innovate UK, Refeyn Ltd, Rentschler Biopharma