Harnessing continuous improvement in the CAPA process
Posted: 3 August 2023 | Catherine Eckford (European Pharmaceutical Review) | No comments yet
In a risk-based framework for implementing a corrective and preventive action (CAPA) process, a continuous improvement approach is proposed as a way to drive higher product quality and improve patient safety.
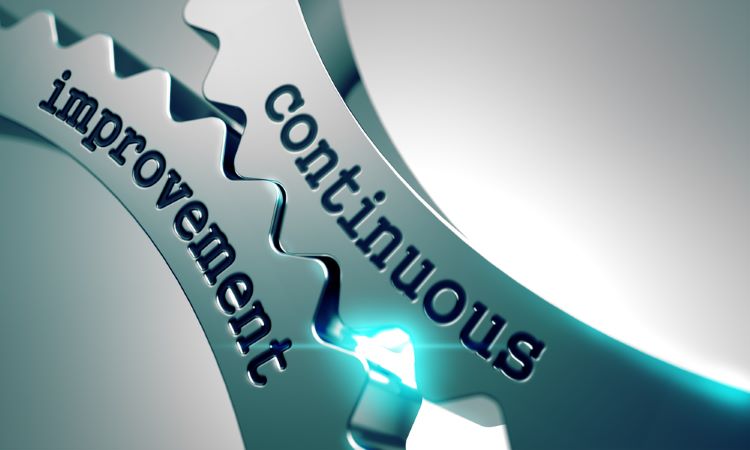
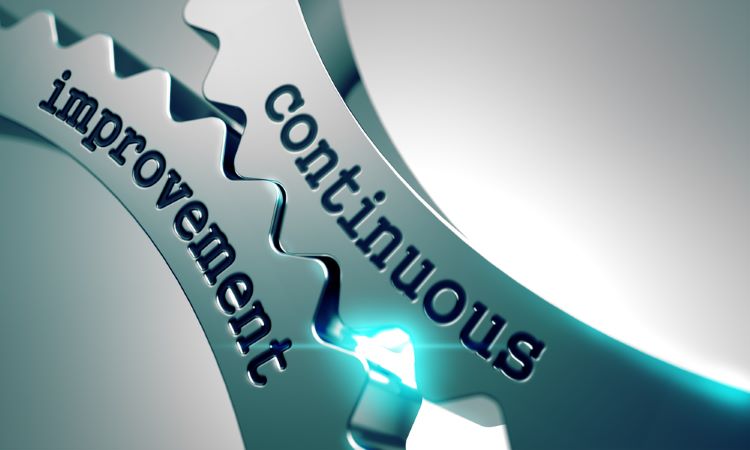
With the corrective and preventive action (CAPA) process often a “one-size-fits-all” approach, a whitepaper by the Medical Device Innovation Consortium (MDIC) Case for Quality Collaborative Community (CfQcc) has instead shared a risk-based framework focusing on continuous improvement.
The optimised framework aims to overall, drive higher product quality and improved patient safety.
Summarising recommendations and best practices for CAPA process improvement, this whitepaper uses data collected from a pilot suggested in the MDIC’s initial whitepaper that proposed the framework. These results are included in most recent paper.
Rather than focusing on documentation with the aim to achieve compliance, the initial proposed framework shined a light on problem-solving and therefore the initiation of preventative action as a key part of the process. Essentially, the risk-based framework pushes developers of medical devices to emphasise high-risk issues, like ones that impact product quality, instead of all events.
According to the MDIC, results from the pilot demonstrated that the optimised framework enable improvements to be applied to the CAPA process in months compared to years. This showed an up-to-80 percent reduction in the time required to implement improvements.
Organisations also experienced improvements in the connected quality management system (QMS) processes, for example, in risk management as well as trending, according to MDIC.
Improving the CAPA process – what does the risk-based framework include?
In the whitepaper, MDIC stated that external quality events (events outside an organisation’s control) are addressed in the framework using “a focused cross-functional effort that includes a fully documented root cause analysis and statistically valid, time-bound effectiveness checks”.
The optimised framework requests that external events and high-risk trends that are potentially patient- or user-impacting follow the external CAPA path. The paper’s authors wrote that internal events (events within an organisation’s control) and low-risk trends follow a fast-track CAPA path.
All other issues (both trends and non-trends), assessed as requiring corrective action, are managed through the existing QMS. For example, these include nonconformance process, complaint management process and the measuring and monitoring process.
US Food and Drug Administration (FDA) guidance on medical device quality defines “least burdensome” to be the minimum amount of information necessary to adequately address a relevant regulatory question or issue through the most efficient manner at the right time, the MDIC highlighted.
This most recent CAPA whitepaper was produced in collaboration with the Medical Device Innovation Consortium (MDIC), the medical device industry, strategy consultants, and the US FDA.
In conclusion, the MDIC encouraged members of the med-tech industry and auditing authorities to continue to “look for opportunities to shift the culture toward actions that would be the most beneficial for accelerating the rate of improvement, therefore favourably impacting the level of product quality over time.”