How can PAT help advance biologics manufacturing?
Posted: 13 July 2023 | Catherine Eckford (European Pharmaceutical Review) | No comments yet
Lonza’s Associate Director of R&D has offered insight on implementing process analytical technology (PAT) into biologics manufacturing using real-world examples.
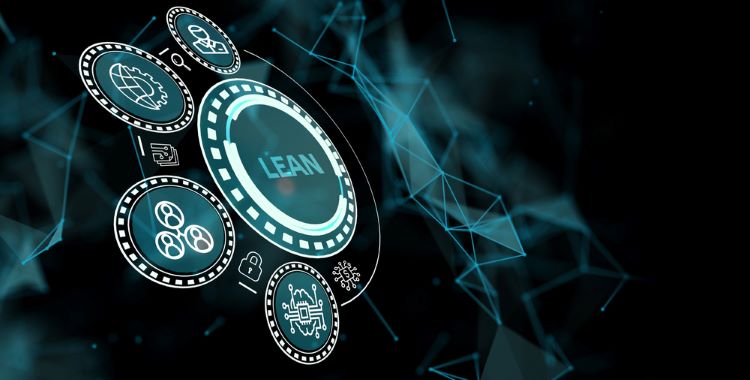
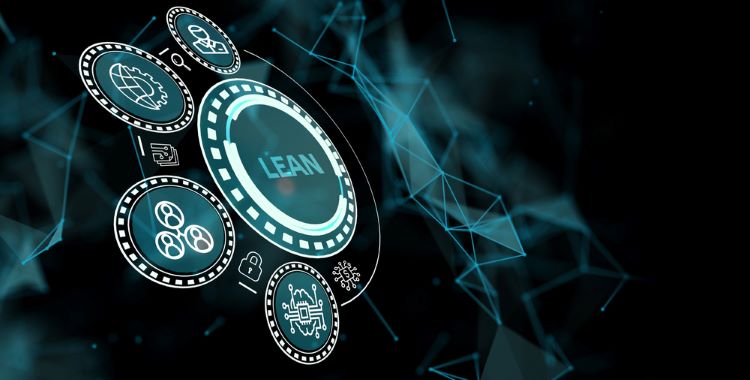
In EPR’s Future of Bio/Pharmaceutical Analysis online summit last month, Lonza’s Associate Director of R&D discussed the benefits and challenges of using process analytical technology (PAT) in biologics manufacturing.
The CDMO’s Carrie Mason shared that PAT, “takes a little bit more time and more effort and more capital to set up in the beginning, but once you get it up and running it’s very continuous and it should continue to provide results for a long time”.
Mason frequently brought up the importance of preparation and expectations when using the analytical technique PAT. Being “very laser focused… really trying to make some good calculations on where to spend the money [and] where to invest the time and energy is critical”.
What is behind biopharma’s modern evolution?
“where the industry is evolving its in-line control… we now have the ability to really control processes based on the data that we’re getting and then the ability to bring that back into the process and enable what I like to call process levers… we’ve gotten to where we are because of digitisation of data.”
Mason reflected that “a lot of our signals early on from our PAT was analogue… [it] gives us great traces” but it was also “very cumbersome”. Process control systems was really able “to bring us to this computerised age of PAT and that has really helped with us being able to make quick strides in bringing these technologies and being able to evaluate them and to make real lasting changes in our processes”.
Advantages of PAT
When asked about the top three benefits of implementing PAT technology, Mason responded: “where you’re going with it is going to be process characterisation” therefore understanding it is like “shining lights into the dark corners of your process and trying to see what’s going on.”
Mason also mentioned that with more information, “we can actually go and start making process changes in order to bring process robustness into the equation [which] is really great from a quality side of things… out of process robustness you start to see process optimisation and your savings”.
Mason noted a few real-world examples of implementing PAT, based on experiences with her team at Lonza. The CDMO team created models that work “very well for our platform processes using glucose control and RAMAN to measure glucose [and were then able] to use our distributed process systems to control glucose swings.”
As a comparison, she offered a practical example: “historically you would take an offline sample once a day once a shift maybe 12 hours every 24 hours…”
However, using their process, Mason and her team were able to “completely automate it… so instead of just making once daily adjustment, we’re then able to control down to a much tighter window of control around our set point using real-time data… real time 15 minutes but in a 12-day bioreactor”. Ultimately, this “really helped us with process variation” she concluded.
Downstream processing
The Associate Director of R&D also covered downstream processing and highlighted that the industry needs to advance in this area. Mason predicted that for chromatography, there is going to be “more of a multi-quality attribute monitoring [and] where these all become kind of interlinked and why we need them is the fact that continuous chromatography [is very] data heavy.”
Recruitment in the biologics manufacturing sector to deliver PAT
Touching on recruitment in the biologics manufacturing sector, Mason commented: “we are now putting into our systems a requirement for much more data for a type of analytics that hasn’t been done before, so I think our systems of controls engineering and programmers… we’re a little bit behind when it comes to recruiting talent into that area.”
She urged the industry “to do a better job… [at] saying how big data and how process control engineers are critical”. Mason added: “the industry truly underestimates the amount of people that we would need for [digitalisation and data]” and proposed that to help solve this lack of awareness, “academic outreach is very critical”.
When questioned more broadly on what she would change or do differently, based on previous experience, Mason replied: “understanding how to design your experiments… finding out how things work right and then really having a view of what your expectations are.”
Related topics
Analytical techniques, Big Pharma, Biologics, Biopharmaceuticals, Bioprocessing, Continuous Manufacturing, Contract Manufacturing, Contract Research Organisations (CROs), Drug Development, Drug Manufacturing, Industry Insight, Interviews, Manufacturing, Process Analytical Technologies (PAT), QA/QC, Raman Spectroscopy, Recruitment, Research & Development (R&D), Therapeutics