Innovative PAT-based filtration strategy reported for continuous biomanufacturing
Posted: 10 July 2023 | Catherine Eckford (European Pharmaceutical Review) | No comments yet
The PAT-based approach is the first of its kind to prevent membrane fouling when using a robust single-pass tangential flow filtration (SP-TFF) operation in bioprocessing, according to a paper.
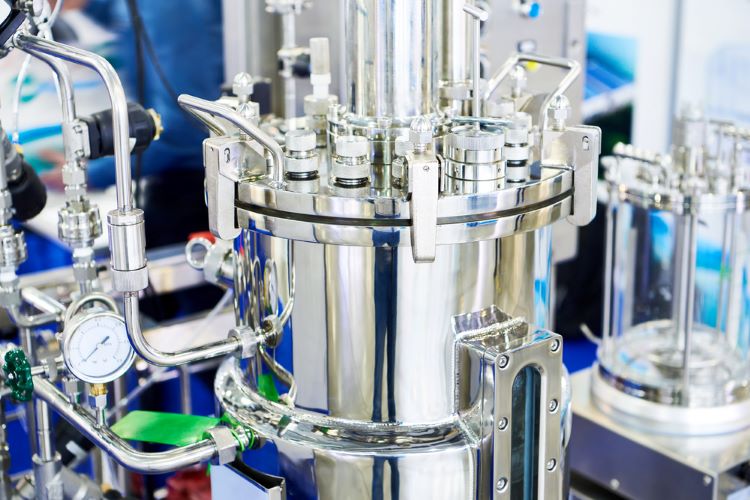
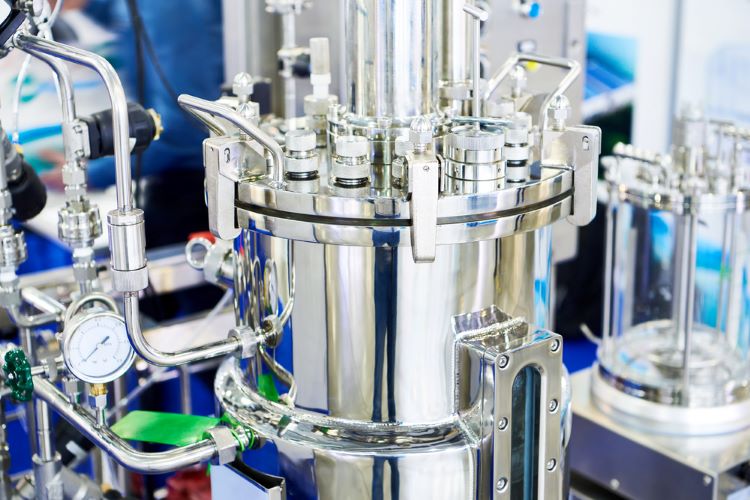
A paper published in Journal of Membrane Science has demonstrated an approach for implementing a robust single-pass tangential flow filtration (SP-TFF) operation in either batch or continuous format during biomanufacturing. The process analytical technology (PAT)-based strategy used SP-TFF in an integrated and continuous manner for six days.
Specifically, the authors proposed a technological solution involving robust control algorithms for precisely maintaining consistent protein concentration in single-pass ultrafiltration (SP-UF) and achieving the targeted buffer exchange in single-pass diafiltration (SP-DF).
Applying the novel PAT-based filtration technique
The PAT-based approach can be adopted in therapeutic bioprocessing and validated by demonstrating an integrated and continuous operation of SP-UF and SP-DF.
The novel approach is the first of its kind that prevents membrane fouling… when implementing a robust SP-TFF operation in either batch or continuous bioprocessing”
According to the authors, this novel ‘bottom-up’ SP-TFF PAT-based technique is the first of its kind that prevents membrane fouling and maintains the target process and product attributes when implementing a robust SP-TFF operation in either batch or continuous bioprocessing.
Bench-scale experiments were conducted at potential operating conditions to characterise the SP-TFF process and developing semi-empirical models as a function of the feed flux and feed concentration for the operating ranges. As a result, optimum filter sizing and SP-TFF performance was identified. This implemented robust process control to achieve desired protein concentration in SP-UF and maintain consistent concentration and obtain targeted DVs of buffer exchange in SP-DF.
Benefits of integrated and continuous biomanufacturing (ICB)
ICB offers several advantages in fed-batch and perfusion bioreactors compared to traditional batch methods:
- Facilitating a reduced facility footprint
- Compatibility with single-use technologies
- Consistent and homogenous product quality
- Reduced capital and operating costs.
However, most of these advancements have been early in the purification process, with relatively fewer advancements in the final filtration steps, Malladi et al. observed.
In recent years, SP-TFF has become favoured compared to traditional TFF in both batch and continuous processes because, for example, it can handle higher process volumes. This eliminates a potential bottleneck in downstream purification operations.
Being able to perform continuous SP-UF and SP-DF is a key element for successful integrated and continuous biomanufacturing of formulated drug substances. The biopharmaceutical industry has been shifting from traditional batch processing towards integrated and continuous biomanufacturing (ICB), due to an increased necessity to achieve process intensification and implement agile manufacturing, the authors highlighted.
According to the paper, from a process intensification perspective, recent advances have facilitated increased cell densities in fed batch and perfusion reactors resulting in higher product volumes and titers. These productivity gains constrain the downstream operations, necessitating greater flexibility in their design and processing capabilities in a cost-effective manner.
A fundamental advantage of the novel process analytical technology-based method described in the paper by Malladi et al., is that it can be applied not only in continuous biomanufacturing, but in other processes like batch or cyclic batch too. Its application covers not only monoclonal antibodies (mAbs) but also different modalities such as fusion molecules and enzymes.
Related topics
Analytical techniques, Antibodies, Biologics, Biopharmaceuticals, Bioprocessing, Bioproduction, Continuous Manufacturing, Drug Development, Drug Manufacturing, Manufacturing, Microbial Biological Manufacturing, Process Analytical Technologies (PAT), Research & Development (R&D), Technology, Therapeutics