Validating FTIR for rapid cleaning verification
Posted: 4 October 2022 | Caroline Peachey (European Pharmaceutical Review) | No comments yet
Researchers simulated the effect of surface roughness on Fourier-transform infrared (FTIR) spectroscopy, developing guidance for validating the technique for rapid cleaning verification.
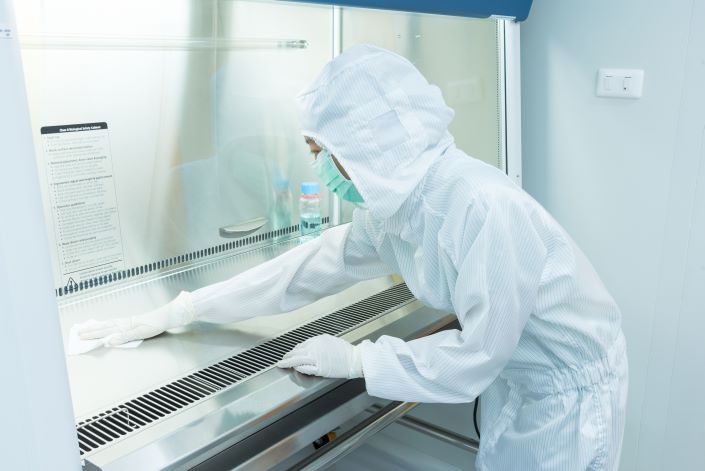
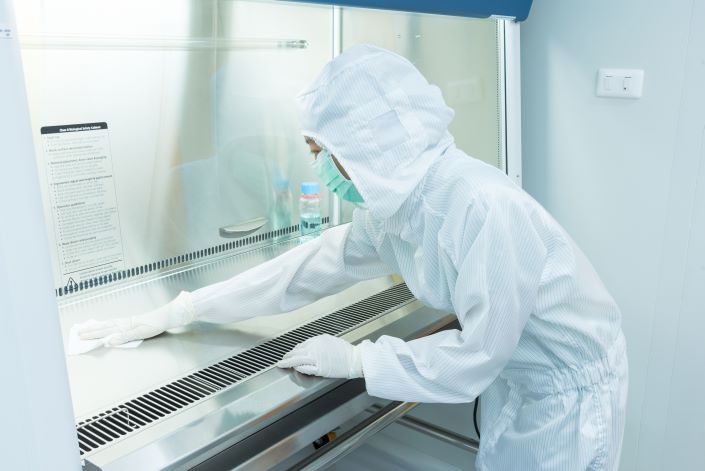
Currently, validation of cleaning processes for pharmaceutical manufacturing equipment is done using analytical methods such as swab or rinse and subsequence laboratory testing. Fourier-transform infrared (FTIR) technology has the potential to produce the results in real-time, as well as improve the analytical accuracy significantly. However, although FTIR has proven to be effective, it must be robust to be used in a Good Manufacturing Practice (GMP) manufacturing facility.
A study by Sarwar et al. published in Talanta Open focused on potential sources of interferences that may impact the result of FTIR during routine use as a solution for real-time cleaning verification.
During the lab-based investigation the researchers looked to identify the surface roughness or surface type using FTIR before completing the measurement so they could use an appropriate calibration model for the surface measurement.
The experiment was divided into two parts:
- use a blank coupon to identify the surface type using an FTIR
- deposit active pharmaceutical ingredient (API) on the coupon and quantify the effect on the actual API to simulate the real-life scenario.
As FTIR measurement is performed directly on the surface it is crucial to understand the effects of the different surface types used in the pharmaceutical manufacturing plant, the authors noted.
It is well known that most pharmaceutical manufacturing equipment is stainless steel. However, the study demonstrated that the surface finish number could impact chemical prediction by approximately 28 percent.
The entire range of the stainless-steel surface types used in pharmaceuticals can be divided into two groups, namely (a) finish number 4, 5 and 6 with badly scratched surface and (b) finish number 7 and 8 with minor scratches.
“The use of two different calibration models can significantly improve the robustness and accuracy of the measurement,” they added.
Sarwar et al. found that various factors could interfere with the measurement such as temperature, instrument measurement distance & angle to the surface, and chemical interference.
Key recommendations from the study include:
- That the manufacturing equipment must be visually clean prior to analysis
- Checking the FTIR spectral alignment in the software to prevent collecting data far from the surface
- Regular collection of background when the instrument is used in an uncontrolled temperature environment.
“Incorporating the mitigation demonstrated in this investigation are critical such as measuring the surface roughness using the FTIR before measurement using a [principal] component analysis (PCA) model,” the authors stated.
“If the method described in this investigation is followed precisely, the FTIR would be capable of measuring surface cleanliness with a high degree of accuracy,” they added.
Future potential…
The study concluded, “Although the rapid cleaning verification method using the FTIR can be validated using the guidance outlined in this paper and the previous publication by the author, a comparability study to swab testing will be required prior to using the technology in a good manufacturing practice (GMP) regulated pharmaceutical manufacturing environment.”
Sarwar et al. also noted that while FTIR technology has the potential to be a game-changer for cleaning verification practices, the size of the current instrument and the collection interface remain significant challenges. “Smaller compact FTIR and the collection interface are critical for the technology to succeed in the pharmaceutical cleaning verification sector,” the authors stated.