How should cleaning validation sampling locations be chosen?
Posted: 1 July 2022 | Hannah Balfour (European Pharmaceutical Review) | 2 comments
Here EPR summarises the salient points of a case study, presenting a strategy for identifying worst-case sampling locations on equipment for cleaning validation.
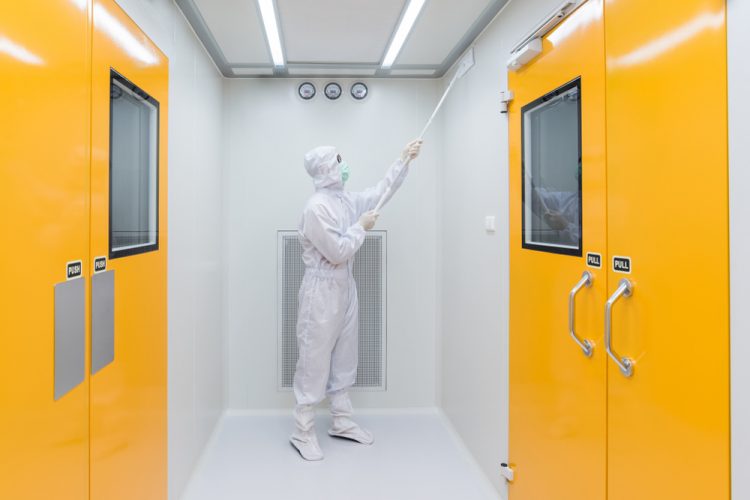
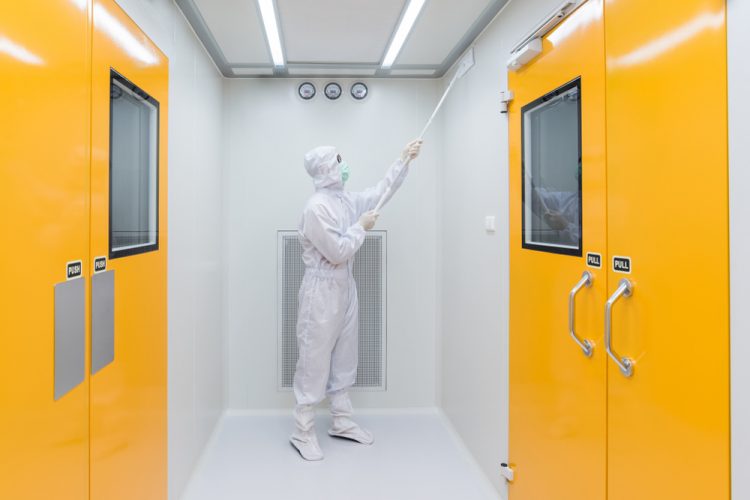
A recent paper outlines a process that can be used to select and document worst-case sampling locations to validate cleaning processes.
The article, published in the Journal of Validation Technology (JVT), presents the case study of a company undergoing an investigation and developing a strategy for identifying worst-case sampling locations on equipment, after a regulatory auditor asked for such a rationale and no written documentation could be provided.
Author Paul Pluta, Editor-in-Chief of JVT, explained how the validation of cleaning processes is an important requirement in pharmaceutical manufacturing, as it prevents cross-contamination, thereby assuring product integrity. A critical aspect of validation is selecting the appropriate sampling locations to test the cleaned equipment.
However, despite regulatory guidelines recommending the selection of worst-case sampling locations for cleaning validation, how to select such locations is not stated, nor is how to document these selections in regulatory filings.
To overcome these concerns, Pluta presents the process and documentation activities undertaken by one company.
Following the request by the auditor for the company to justify the selection of worst-case sampling locations for cleaning validation, according to Pluta, the enterprise undertook an investigation to develop the required documentation. Four activities were undertaken:
- Categorising and listing sampling locations to help identify potential contamination locations on all equipment eg, areas that are difficult to clean, may accumulate process residue, have maximum product contact
- Selection of sampling methods, eg, swab or rinse sampling
- Evaluation of sampling locations and methods – with input from engineering, quality, validation and operations personnel, the company identified problematic cleaning areas, sites with significant residue accumulation, whether the equipment could be disassembled and other parameters. This was the primary information supporting the identification of worst-case sampling locations for cleaning validation
- Based on these evaluations, sampling locations and methods for specific equipment were recommended. In addition, a general hierarchy of how sampling locations should be chosen was developed for future applications.
Corrective and preventative actions (CAPA) were then used to implement the new sampling location strategy.
Pluta noted: “The selection of sampling locations in cleaning validation must be dictated by risk assessment, ie, surface material, access for cleaning, level of contamination, and other factors that may impact cleaning must be considered when designing cleaning validation.”.
He added: “If sampling sites and methods are not correctly chosen, the cleaning validation is questionable. Regulatory guidelines clearly state that sampling locations for cleaning validation must include worst-case sampling locations. Documentation affirming the selection of sampling locations and methods must be available.”
He concluded that aside from the direct benefit of meeting regulatory guidance, the company also observed other benefits from the investigation, for instance, the equipment review enabled it to modify equipment to better enable cleaning, eg, the shortening of pipe lengths. The enterprise was also able to overcome other design deficits, eg, improving drainage where rinse water was found to accumulate; and improve disassembly and equipment cleaning procedures, according to Pluta.
Based on these evaluations, sampling locations and methods for specific equipment were recommended. In addition, a general hierarchy of how sampling locations should be chosen was developed for future applications.
Could you please provide the journal for hierarchy of how sampling locations to be selected
You can find the link to the source for this story here: