How should environmental monitoring locations be chosen?
Posted: 21 April 2022 | Hannah Balfour (European Pharmaceutical Review) | No comments yet
Here, EPR summarises Dr William Whyte’s guidance for formally selecting cleanroom monitoring locations and action levels.
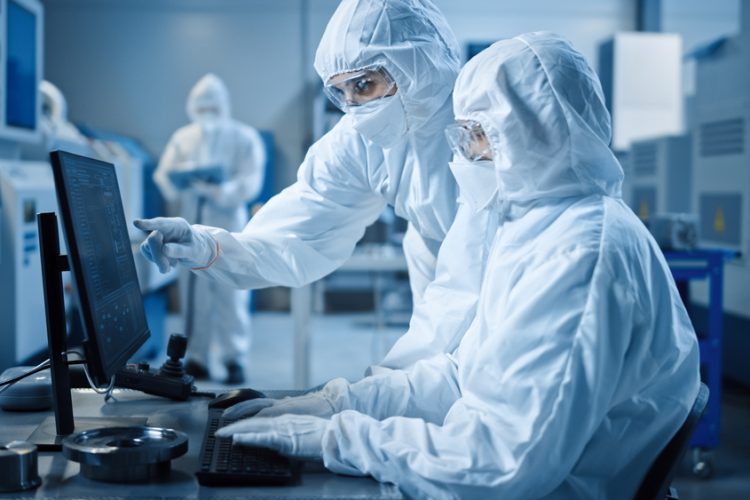
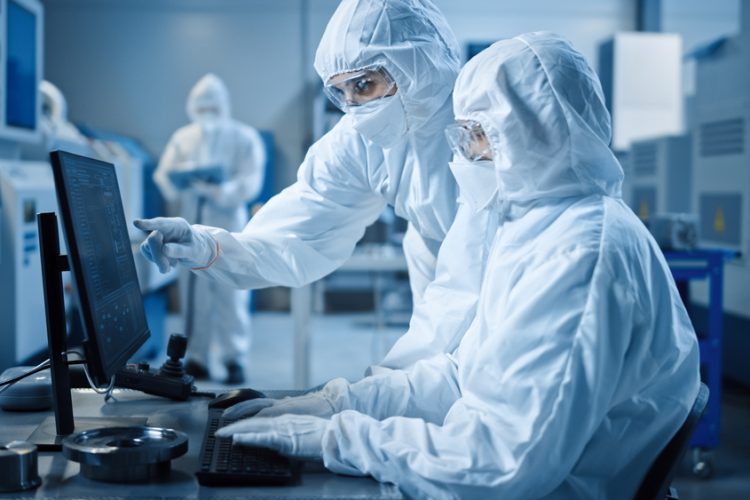
Airborne concentrations of particles and microbe-carrying particles (MCPs) in cleanrooms have to be monitored and maintained below certain levels. While monitoring locations and control levels are often decided informally, what should the formal approach look like?
In a new paper, Dr William Whyte outlines a formal approach to selecting cleanroom monitoring locations and setting control levels. He explained that a risk assessment should be undertaken to identify locations where there is the greatest risk to the product or process.
Dr Whyte described the three types of monitoring locations:
- critical locations – those with the greatest risk of contamination to product or process, “where critical surfaces such as product, components and processes are exposed to direct deposition of contamination from the surrounding air”
- critical control points (CCPs) – where the transfer of airborne contamination to the product or process is controlled, but failure in the control “is likely to cause significant product contamination”
- sources with high dispersion rates – for example a machine or person where contamination can be easily transferred to critical surfaces.
To formally define these locations, Hazard Analysis and Critical Control Point (HACCP) 4 and Failure Mode and Effect and Criticality Analysis (FEMCA) 5 are risk assessment methods most frequently used in cleanrooms, according to Dr Whyte. The first step in these assessments is to choose locations that have a potential for causing airborne contamination of critical surfaces and then calculate the risk, considering the probability and severity of the risk factors of contamination.
The full paper gives examples of risk assessments being undertaken to select the highest risk locations for monitoring.
Once the locations are selected, you need to know what to monitor for. There are two common control levels: alert and action. The action level is the concentration of contaminants that should not be exceeded, prompting immediate action if it is, where the alert level is “an airborne concentration that is greater than normally found in the cleanroom or clean zone,” and essentially acts as an early warning of potentially unacceptable conditions.
To define these levels, Dr Whyte presents formal statistical approaches based on Statistical Process Control (SPC) 11.
For a cleanroom with roughly normally distributed contamination, there are two options for setting the levels:
- set the action value at the maximum particle or MCP concentration set by guidances such as ISO 14644-1, Annex I of the EU GGMP or the FDA Guidance, and the alert value at two (95 percent confidence level) or three (99.7 percent confidence level) standard deviations above the mean particle concentration.
- set the action level at an airborne particle concentration that is rarely exceeded in the cleanroom, typically three standard deviations above the mean, and the alert value at two standard deviations above the mean.
For a non-parametric (not normal) distribution, control levels of airborne concentrations can be set at the upper percentiles in exactly the same way as the standard deviation confidence limits – ie, 95th percentile is equivalent to 95 percent confidence limit.
For further details, read the article published as an annex in the book Cleanroom Testing and Monitoring and reproduced in the latest issue of European Journal of Parenteral and Pharmaceutical Sciences.
Related topics
Airborne particle counting, Cleanrooms, Environmental Monitoring, Microbial Detection, Microbiology, QA/QC