GCD enables product traceability and batch definition in continuous biomanufacturing
Posted: 12 November 2021 | Hannah Balfour (European Pharmaceutical Review) | No comments yet
Research shows using the greatest common divisor (GCD) to define batches in continuous biomanufacturing enhances process control and raw material traceability.
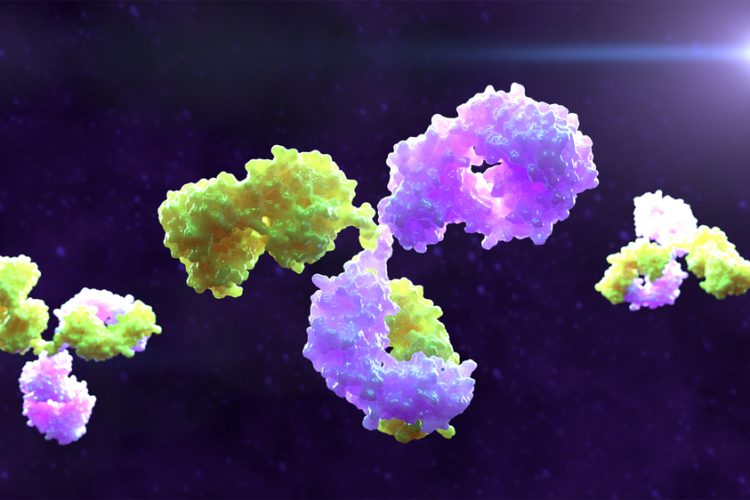
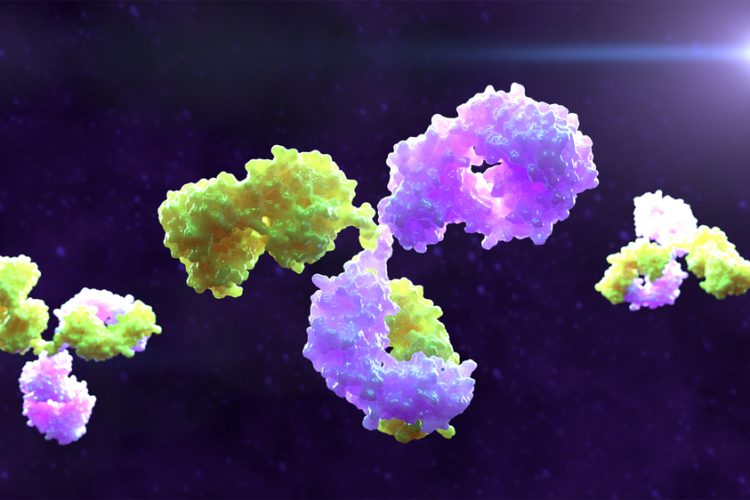
According to a new paper, using the greatest common divisor (GCD) could enable biomanufacturers to define batches and trace raw materials in fully continuous and hybrid bioprocesses.
The authors explained that despite continuous integrated processing’s potential to improve biomanufacturing, two major challenges in its implementation are the traceability of the product and the definition of batches.
Guidance suggests batches are defined by residence time distribution (RTD), “a probability distribution that describes the amount of time a mass or fluid element remains in a process, and can be measured through a tracer experiment, online process measurements of appropriate product attributes, and/or process modelling”. However, ICH Q7 states that, in continuous processing, a batch could be as large as the entire campaign or a fraction of the production campaign. The larger the batch, the more of a concern it is economically if it fails, so for many it is a priority to break up the production run and have smaller batches.
In a paper published in Journal of Chemical Technology and Biotechnology, Lali et al. describe the application of GCD (which takes into account the time period of unit operations) in defining batches and compare it to the conventional idea of using a fixed time period to define them. Their research concerned the semi-continuous purification of antibodies using staphylococcal Protein A affinity.
In the study, the scientists divided the inlet stream of a three-column periodic countercurrent chromatography (PCC) system in two ways: 1) even sections of two hours, an arbitrary number; and 2) sections based on GCD, in this instance, 2.29 hours. They then tracked the product through the process using an RTD model and found that the outlet could also be sectioned based on the inlet sectioning times. These outlet sections could then be called a batch or pooled to create a larger batch.
The authors reported that when sectioning was based on the GCD of the period for semi-continuous unit operations, there was a predictable, constant periodic behaviour in the outlets. With the arbitrary time selection, this outlet pattern was chaotic. The consistency enabled the amount of different inlet sections in the outlet to be quantified, providing traceability of materials and process control. Moreover, the authors stated that the GCD method better fulfilled the regulatory criteria of knowing RTD than dividing batches based on an arbitrary number of hours or days.
Lali et al. wrote: “Finding a solution for a continuous integrated biomanufacturing batch definition is crucial”, explaining that their GCD method not only allowed them to trace raw materials, but also enhanced process control and did not require high-tech equipment nor expert human resources. They added that a further benefit is that the GCD method could also be used for hybrid processes – integrating some continuous unit operations and some batch.
“Using GCD, we optimised the traceability of raw materials through the entire continuous interconnected process train, and we obtained a robust and stable description of where raw materials end up in the end product. Using GCD as a guide for batch definition or as a process design parameter for interconnected processes allows for quantified and stable section output in terms of which inlet sections end up in which outlet section,” they concluded.
Related topics
Biologics, Bioprocessing, Bioproduction, Chromatography, Drug Manufacturing, Models, Therapeutics