Online drying process control of pharmaceutical intermediates using near-infrared spectroscopy in a bypass system
Posted: 27 February 2019 | Christian Huck - Leopold-Franzens University | No comments yet
Strong regimentation and economic interests demand the development and implementation of new techniques for process control and analysis in the pharmaceutical industry. The extensive analysis of all deployed materials, intermediates and products leads to a higher degree of process stability and can contribute to a faster compensation for deviations, especially at highly critical production steps.
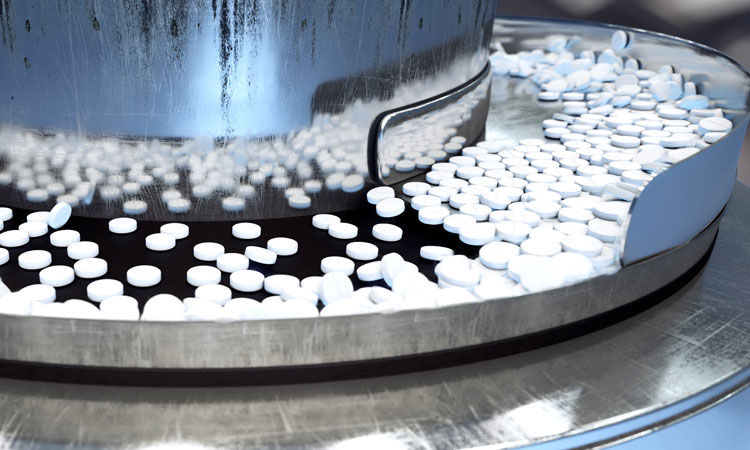
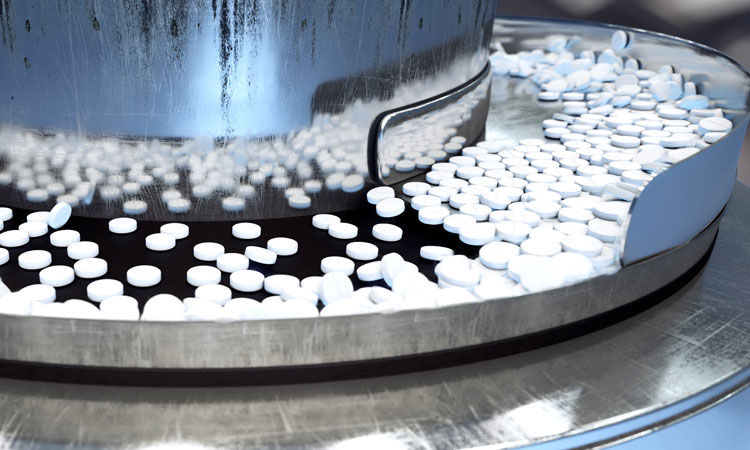
Traditionally, wet chemical analysis was applied to gather the required information about the content of water and solvent residues, requiring significant chemical, financial and time expense. As a result, there is increasing interest in replacing these methods with efficient spectroscopic techniques that offer fast, non-invasive analysis of manifold parameters simultaneously.
With online near-infrared (NIR) control systems for the drying steps, real-time product information can be used to reduce the risk of over-drying and improve product yield and quality, especially during longer cycle times. Minimal manual sampling decreases safety concerns, and considerably less reference analysis limits environmental impacts and saves money.
In this article, the implementation of an automated online monitoring system based on the continuous evaluation of NIR spectroscopy data is summarised and evaluated for a fluidised-bed drying process of a pharmaceutical intermediate. The objective of the original study was to determine the ideal end point at which to stop the drying course during the ß-lactam antibiotics production and therefore attain the best product assay at sufficiently reduced levels of water and solvent content at the same time. Using this approach, the NIR device continuously collects spectral data throughout the whole drying process and performs an automated evaluation to effectively follow and assess the drying progress based on the calculated product, assay and water contents supplemented with the fluidised-bed temperature profile.1
Experimental
NIR spectroscopy: A Solvias reflector process probe (PP; Solvias, Basel, Switzerland) combined with a Fourier-transform NIR spectrometer (Matrix-F, Bruker Optik GmbH, Ettlingen, Germany) that meets the required automation criteria was used for the control system implementation. The spectrometer covers the wavelength range from 4,000-12,000cm-1 with a variable resolution down to 1cm-1. The stainless steel probe offers a temperature stability up to 130°C with an immersion depth of 300mm and a 12mm tip diameter. The 3mm beam spot is directed onto the sample substance through a sapphire window. The probe placed in the production area (EX zone 22) is connected to the spectrometer device in the analysis room via coupled 2m and 5m fibre optic cables.
The spectrometer device is additionally equipped with a laboratory probe (LP) using a multiplexer connection to enable complementary offline spectra recording. An automatic trigger for continuous measurements is provided by the process control system via a PROFIBUS interface using an OPC client/server system on the control PC running the OPUS 6.5 PROCESS package. Data evaluation is performed immediately with the OPUS/QUANT module according to the respective calibrations. The resulting values are sent back to the process control system and displayed on the switch-room monitoring screen.
Reference methods: Water – to quantify the water content of the samples, a Karl Fischer back-titration method was performed; HPLC – product assay was determined by isocratic high-performance liquid chromatography (HPLC); GC – the respective content of acetone was analysed by gas chromatography.1
Results and discussion
In the production plant of – for example, an antibiotic intermediate – a fluidised-bed dryer can be installed to complement the former slow vacuum paddle dryer method leading to limited product quality, brining stress and long-term direct heat impact on the pharmaceutical product.
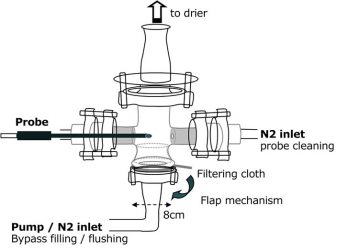
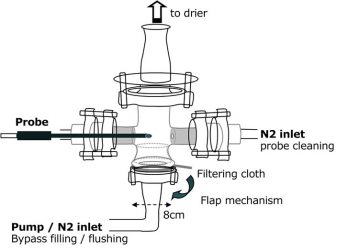
Figure 1. Schematic drawing of the bypass configuration
Sampling system: Measuring configurations directly inside the drier – such as a contact-free measurement head applied through a window or an integrated probe positioned toward the product stream – had to be discarded due to high inefficiency. To minimise several factors of uncertainty a bypass configuration was designed to record spectra outside the drier. The bypass system (Figure 1) had to meet the following requirements: a fast and reliable filling and purging procedure; reproducible and defined sample density during the measurements; an efficient probe tip-cleaning mechanism to avoid artefacts; and both optical and easy mechanical access to the sample material for operational control and reference analysis. The inner part of the bypass system should be kept as simple as possible and the sample volume should be kept small to reduce temporal effort for each measuring cycle. The final system was made of glass with the probe tip pointing outward to enable direct visual access to inspect proper coverage of the probe. Employing a vacuum pump, moist product is withdrawn and following recording of the spectra the whole sample powder is blown back with nitrogen gas. The probe itself is cleaned with a directed gas stream across it to avoid contamination. Sample drawing is conducted manually with a spatula through a sealed window.
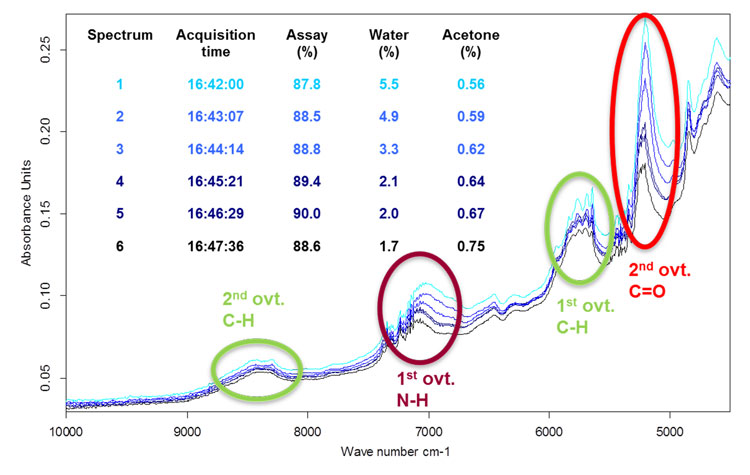
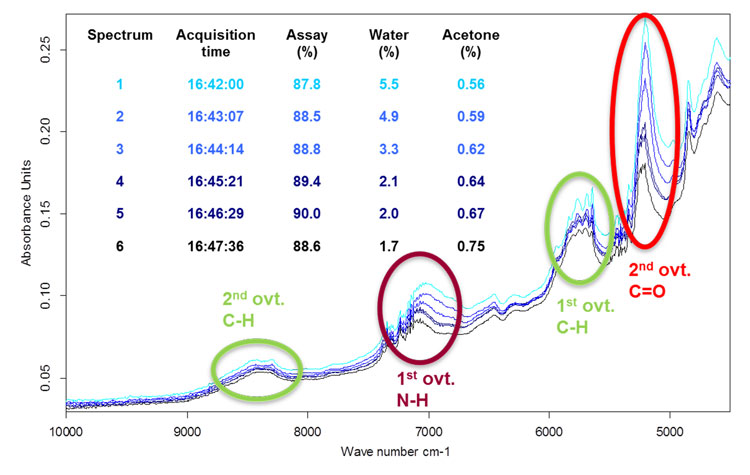
Figure 2. Example of six spectra recorded just before reaching the drying end point
Calibration procedure: The bulk set of process-probe calibration spectra was recorded systematically at internal drier temperatures of 90, 100 and 105°C and the drying end point at approximately 110°C. Figure 2 displays a typical set of changing spectra of the increasingly dry material during a drying course used for calibration. Spectra of the intermediate show a high fibre-optic-related noise level at wavenumbers below 4,200cm-1 and low intensities in the higher-wavenumber region. Therefore, only the range between 4,200 and 9,000cm-1 was considered for multivariate calibration. The basic spectral feature of the complex antibiotic molecule containing a -lactam structure is the massive water peak at 5,206cm-1 strongly varying in size. A second broad peak originating from water vibrations dominated the wavenumber range at around 7,000cm-1. Signal features in the range of 5,600-5,900cm-1 arise from CH and CH2 first overtone vibrations. The spectral characteristics that feature in the region of 4,100-4,400cm-1 refer to CH combination bands of fundamental vibrations and deformation modes. Patterns in the region of 7,000-7,400cm-1 arise from CH combination bands of overtone and fundamental vibrations. The process-probe calibration set was expanded with a set of spectra recorded offline, outside the bypass in separate glass vials to broaden the temperature range and integrate sufficient bulk density variations.
Calibration results: All calibration spectra were mean-centred and subjected to a range of standard spectral pre-treatment methods such as vector normalisation, multiplicative scatter correction, first and second differentiation, and different combinations thereof. The optimised details of the calibration obtained can be deduced from Table 1.1,2
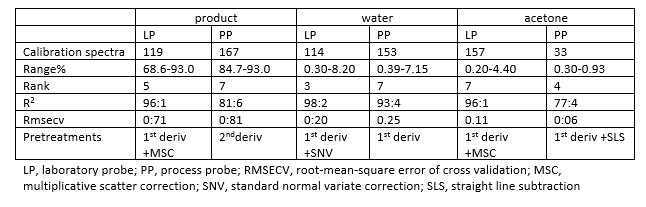
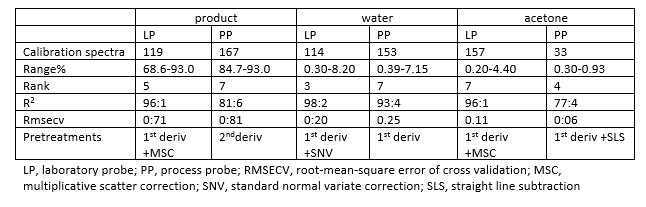
Table 1: Details of the Calibrations Obtained for the Three Different Parameters for the Two Probe Types
Testing of the method: The calibrations were tested for their reliability over an extensive period with independent test samples. During a three-month testing time the average deviations of the NIR predictions from the reference values for all disposable samples were 0.87 percent for assay (64 samples), 0.28 percent for water (83 samples) and 0.14 percent for acetone (20 samples).
Conclusions
Routine operation is now performed by combining the NIR results with the drying temperature progression. Any deviation from the normal drying course can be detected easily and instantaneously. This is a highly efficient way to improve and stabilise quality in antibiotics production.
References
- Märk J, Karner M, Andre M, Rueland J, Huck CW. Online Process Control of a Pharmaceutical Intermediate in a Fluidized-Bed Drier Environment Using Near-Infrared Spectroscopy. Anal Chem [Internet]. 2010 May 15 [cited 2016 Dec 23];82(10):4209–15. Available from: http://www.ncbi.nlm.nih.gov/pubmed/20405893
- Märk J, Andre M, Karner M, Huck CW. Prospects for multivariate classification of a pharmaceutical intermediate with near-infrared spectroscopy as a process analytical technology (PAT) production control supplement. Eur J Pharm Biopharm. 2010;76(2).
Biography
Christian Huck is currently a Professor for Analytical Chemistry at Leopold-Franzens University of Innsbruck, Austria. He is developing novel analytical tools mainly based on vibrational spectroscopy, including separation and enrichment techniques in the field of pharmacy, medicinal plants, food and material science. He has been a visiting guest professor at Prof. Yukihiro Ozaki´s lab in Sanda, Hyogo, Japan and is also editor in chief of NIR news.
Issue
Related topics
Analytical techniques, Drug Manufacturing, Manufacturing, Near Infrared Spectroscopy (NIR)