Manufacturing Solutions: Continuous processing
Posted: 20 April 2015 |
Ivo Backx of Siemens discusses continuous processing in the context of the company’s Simatic PCS 7 system and PAT software…
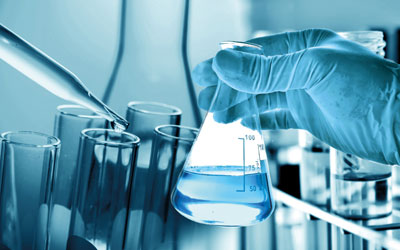
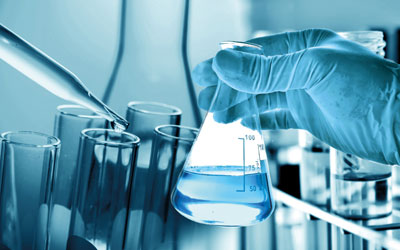
The pharmaceutical industry is currently dominated by batch processes. However, a continuous process offers substantial benefits – so substantial, in fact, that the US Food and Drug Administration (FDA) actively promotes the development and introduction of continuous process concepts in pharmaceutical manufacturing.
Recently, companies have presented the first concepts for continuous production plants for commercial application in Oral Solids Dosing Manufacturing. Now, concepts are being developed for Bioprocessing. A key factor for implementing such concepts in an actual production environment are integrated automation solutions and process analytical technology (PAT) systems for in-line quality control.
The main arguments in favor of continuous processing, according to Janet Woodcock, Director of the FDA’s Center for Drug Evaluation and Research (CDER), are agility, flexibility, geography, quality, costs, and societal benefits1. Continuous manufacturing will permit increased production volume without the current problems related to scale-up and also help accelerate clinical development. Additionally, continuous manufacturing facilitates regional or in-country manufacture and scalable capacity in case of emergencies. Continuous manufacturing also improves uniformity of products so that higher-quality drugs can be produced with less waste. Less waste and a better utilisation of resources also reduces the environmental impact.
With a view to these opportunities, experts expect that continuous processes will grow from 5% of business today to as much as 30% over the next 10 years. At the same time, continuous manufacturing requires a shift in mind-set on different levels within the pharmaceutical industry. It creates the need for a tighter integration between process, PAT, and control systems.
From proof of concept to production scale
At the 2013 Continuous Bioprocessing Conference in Barcelona, Spain, an industry consortium initiated by Bayer Technology Services presented a proof of concept for a complete continuous bioprocess at lab scale. Since then, the concept has been further advanced and is now refined for a production-scale application, including the matching systems for process control and PAT. The findings so far illustrate the significant payoff of establishing continuous manufacturing in bioprocessing: continuous processes work as a closed production system, so there is no need to enclose equipment units in clean rooms and physically separate the different processing steps from the general production environment. This could result in savings of up to 70%2.
Upgrading processes and systems for continuous processing
Part of this consortium is Siemens, which provides the process control technology (based on the Simatic PCS 7 process control system) and the PAT software (based on Sipat). Currently, Siemens is working with the partners in the project to create the required standardised architecture for an integrated process control system for upstream, fermenter, and downstream processing. In continuous processing, the integration of unit operations requires global coordination of the entire process flow. Continuous systems have to be equipped with a second-level software control system that supervises and aligns the operations of the individual units. Both hardware and software should provide a high degree of automation, requiring minimal operator involvement. Another focus is on defining and developing a standard interface for easy and efficient integration of equipment units from multiple manufacturers, which is a prerequisite for modular continuous-production processes.
Maybe the biggest challenge is in developing suitable analysers to monitor critical-to-quality data in process and in real time. To create a working solution while the available technology is developed to provide adequate options for monitoring biological processes, Siemens has integrated its Sipat software with rapid at-line sampling and analysis, and advanced modeling and data analysis tools to provide real-time release capability with systems that are currently available.
Continuous manufacturing: The next step
Although a large amount of research and development is still needed, continuous manufacturing is an essential part of meeting the growing need for agile, efficient, local, and high-quality biological production in the pharmaceutical industry. It will help the industry achieve operational excellence through a higher degree of automation, streamline drug development by offering a uniform platform for clinical development and commercial production, and significantly reduce production footprint and capital expenditures.
References
- Janet Woodcock, “Modernizing Pharmaceutical Manufacturing – Continuous Manufacturing as a Key Enabler” (paper presented at MIT-CMAC International Symposium on Continuous Manufacturing of Pharmaceuticals, Cambridge, MA, May 20, 2014)
- Thomas Daszkowski, “Continuous Processing in Biotech Production: An Alternative to a Modern Single Use, Batch, Facility?” (paper presented at Integrated Continuous Biomanufacturing Conference, Castelldefels, Spain, October 20–24, 2013)