Merck & Co.’s automated compound distribution centre
Posted: 23 May 2006 | | No comments yet
In the mid-1990s, HTS labs were equipped with high-end automation for screening tens of thousands of compounds while compound management labs continued to manually pick samples and invest in standalone equipment…
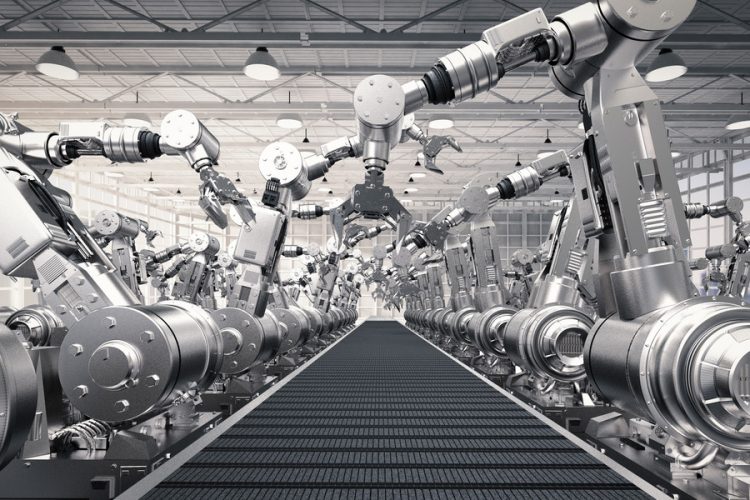
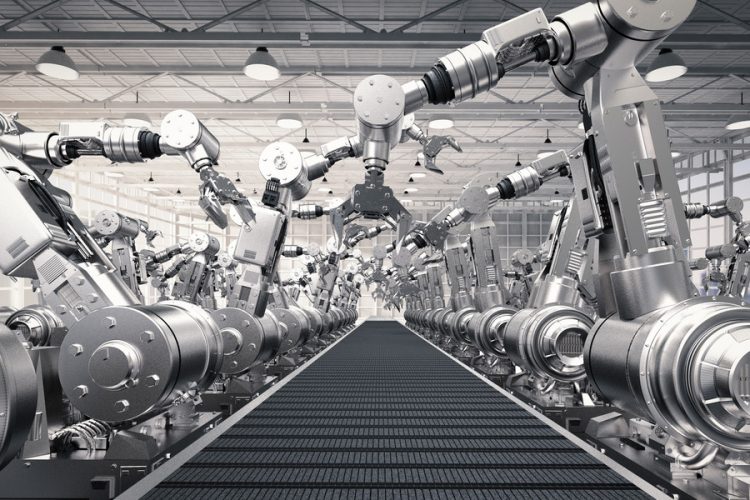
The bottleneck for screening shifted from testing samples to distributing compounds. In order to solve this problem, Merck & Co., Inc., developed an automated compound distribution center. The facility uses automation from The Automation Partnership (TAP), and a Merck-developed compound ordering system to provide solid and solution samples to Merck scientists worldwide.
Ten years ago, High Throughput Screening (HTS) was the buzz word. Pharmaceutical companies spent millions of dollars outfitting HTS facilities with state-of-the-art automation for replicating and screening tens of thousands of compounds daily. This infusion of money and automation led to a decrease in the timeline for finding novel leads in new biological targets. As HTS labs screened 10,000s of compounds per day, the bottleneck moved from screening to the distribution of compounds. Hand-picking bottles was slow and tedious; providing labs with dry or solution samples in vial format was no longer practical. An automated solution was needed to match or exceed the screening capacity of HTS labs at Merck Research Laboratories (MRL). MRL formed a project team consisting of compound management staff, hardware engineers and software engineers to evaluate and determine what internal sample handling processes could be automated while keeping capacity and sample integrity in mind.
Project timeline
Vendor selection for the automated compound distribution centre began in the third quarter of 1999. At the end of this process, The Automation Partnership (TAP) was selected. Initial discussions concerning requirements were held from January 2000 through June 2002. This ended in the delivery of an initial Functional Specification. A Detailed Functional Requirements Specification was completed in the first quarter 2001. An Acceptance Test Plan was completed in July 2002, with Factory Acceptance Testing (FAT) occurring in September 2002.
A new building was built to house the new Compound Distribution Center. Merck’s engineering function, Central Engineering, became involved in discussions with TAP during the second quarter of 2000. Construction commenced in December 2000. The building was fully enclosed by June 2002 (Figure A).
After Factory Acceptance Testing (FAT) was completed, the system was disassembled and shipped across the Atlantic Ocean to Newark, New Jersey. Installation of the system started in January 2003 and was completed by May 2003. Site Acceptance Testing (SAT) was held in June 2003.
The great transfer
During the design and development period, MRL implemented a project plan to transfer all dry compounds to robot-friendly vials and solution samples to 1.4 ml tubes. The goal was to transfer 450,000 dry samples to TAP one dram vials, 50,000 bulk compounds to standard bottles and 550,000 solution samples to Matrix 1.4 ml 2D bar-coded tubes. The plan included hiring five contractors to assist the Compound Management Group’s logistics staff with the dry compound transfer, and the purchase of TAP’s Haywain to accurately weigh the transferred compounds. In addition, MRL hired one additional contractor to help the CMG solution staff verify and replicate solution samples; no additional hardware was needed to complete this task. By September 2003, all samples were transferred to robot-friendly vials and tubes, just in time for the loading of the TAP Automated System.
Initial Load
Initial Load ran from September 2003 through mid-November 2003. MRL had an aggressive schedule for loading the TAP Automated System with the Great Transfer vials and tubes. The Initial Load project plan included two eight-hour shifts working five days per week. The plan had three teams working during the day to cap, scan, and load 10,000 TAP one dram vials into TAP Racks. During the days, two hardware engineers and one software engineer to handle any hardware or software problems. The night shift job was to scan and load our Manual Dry Store and to feed the Automated Dry Store with capped and registered TAP Racks. The goal was to load an average of 10,000 vials per day. This average was met. On several occasions, we exceeded this goal by 3000 vials per day.
IT architecture
The Merck Haystack system is a three-tier system. At the top level is a Merck developed web-based ordering system called Basic Research Compound Ordering System (BRCOS). The middle tier is a TAP developed repository management system called Ordering System for Compounds and Reagents (OSCAR). The third level is the TAP developed automation control suite called PinPoint (IT Flow Diagram Figure B).
BRCOS is a Web-based system used by Merck scientists worldwide to request compounds from the Compound Management Group in Rahway. It allows scientists to order wet compounds, in several standard concentrations or dry compounds. BRCOS uses J2EE technology (Enterprise java beans, XML, XSL), and an Oracle database for the backend.
BRCOS is integrated with the OSCAR system through an Oracle database. It consults the database to determine a compound’s availability, and passes the order information on to the OSCAR system after the user has finished submitting an order. The order is then processed in OSCAR and subsequently by Pinpoint. Once the compounds have been picked and shipped, OSCAR updates the BRCOS database with the type of containers in which the compounds are shipped, boxes for dry compounds and plates for wet ones. Plate and box mappings are electronically available through BRCOS, directly through views of the Oracle database.
OSCAR manages orders within the Haystack system. It retrieves orders sent by BRCOS through the Oracle database. It also accepts orders placed directly by the repository staff. OSCAR also provides many supervisory functions such as order tracking, inventory reports, and audit trails. Orders received by OSCAR are approved before being sent down to PinPoint, which controls the automation.
PinPoint is the third tier of the system. It manages order execution on the automation and operator workstations. PinPoint uses a Sybase database to maintain a record of orders and their status throughout the system. PinPoint sends boluses of work down to individual workstations that control automated components of the system.
Haystack system components
Haywain
The Haywain is used to tare weigh empty one dram vials used for neat compounds and gross weigh one dram vials with compound in them. The Haywain has a Fanuc LR-Mate robot with a TAP-designed wrist. The wrist provides multi-turn rotation for screwing and unscrewing one dram vial caps. Two Metler AT104 balances provide weighing capability.
Weigh booths
There are 15 weigh booths in the system. The weigh booths contain Mettler AT104 analytic balances which are controlled by an ELO touch screen operator interface. Weigh booths are enclosed in a NuAir HEPA enclosure.
Automated dry store
Neat compound samples are stored in one dram borosilicate glass vials. Each vial has a 1D linear barcode on the side. Trays of these vials are stored on the shelves of a vertical carousel manufactured by Kardex AG. There are 98 levels in each carousel, with three trays on each level. Our Automated Dry Store is composed of two Kardex carousels, with a total capacity of approximately 1.3 million vials (Figure C).
The entire process of picking and placing vials is automated.
Manual dry stores
In addition to our one dram vial collection, large bottles of dry compound are stored in four manually-controlled Kardex carousels. These carousels hold approximately 14,000 50ml bottles, 14,000 120ml bottles, and 121,000 40ml bottles.
Solubilisation/replication
Solution copies of compounds are created at the Solubilisation/Replication (Sol/Rep) Station. Sol/Rep is composed of three Tecan Genesis units with modified ROMA arms. The Tecans are used to add DMSO to vials of dry compound. The vials are sonicated, and then the Tecan Genesis units transfer solution from the vials to Matrix tube racks.
Tube stores
Solution samples are stored in 1.4ml Matrix tube racks. Each tube has a 2D DataMatrix barcode on the bottom. Each carousel can store approximately one million tubes (Figure D). Tubes are stored at +4C, with a target humidity of 25%RH. Storage areas have seven air changes per hour. A FM-200 fire suppression system protects the store rooms.
There are two tube storage rooms. The Working Solution Store holds tubes for adhoc requests. The Archive Solution Store holds a copy of the screening set. The Working Store has four carousels with an approximate capacity of four million tubes. The Archive Solution Store has three carousels with an approximate capacity of three million tubes.
Both tube stores are equipped with an RVSI 2D barcode reader. All tubes are scanned when they are placed into the store and when they are picked out of the store. This helps guarantee the integrity of the store.
Plate Production Module
Plate Production Modules (PPM) are used to create daughter plates from mother tubes held in Matrix tube racks. The Matrix tube racks are moved from the solution stores to the PPM by Haywagons. The PPM is composed of six modules: Haywagon docking station, Capper/Decapper, tip transfer module, BasePlate, Plate Interface Module (PIM), and Tray Transfer Module (TTR) (Figure E).
The Haywagon docking station consists of bays where four Haywagons can be docked. Typically, one or two Haywagons are loaded with mother tube racks. One Haywagon is loaded with clean tips. If needed, one Haywagon can be loaded with deep well dilution blocks. The docking station mechanically mates the Haywagon to the PPM, precisely aligning it so that the TTR can withdraw Haytrays. A Haytray is a steel tray designed to hold six Matrix tube racks, six Matrix ‘Dart Holders’ or six dilution blocks.
The Capper/Decapper is on physical module with two separate functions (Figure F). The decapper portion takes caps off of tubes. The capper portion puts new caps on tubes.
Our pipette tip is a Matrix 5503. These tips come in ‘Dart Holders’ from Matrix. A dart holder is a plastic rectangle with 96 holes, in an 8 X 12 array. A tip resides in each hole, forming a tip array. These plastic tip holders are not rigid enough to hold tips on the BasePlate liquid handler head, so each tip must be transferred to a TAP steel tip holder. The Tip Transfer Module (TTM) is used to transfer clean Matrix 5503 tips from Matrix Dart Holders to TAP steel tip holders (Figure G).
The BasePlate is the liquid handling part of the system (Figure H). The system is composed of two three-axis, 96 tip pippetting heads. One head is used to perform liquid transfers. The second head is used to perform dilutions. Typically, a Haytray of uncapped tubes, a Haytray of TAP tip holders, and a Haytray of microtiter plates are on the deck of the BasePlate. If dilutions are being performed, a Haytray of deep well dilution blocks is also on the deck. The BasePlate head uses a stepper motor and lead screw to drive pistons in the pippetting head. The seal between the tips and head is a face seal with a removal gasket. The system has been tested to provide a 3% CV on a one microliter dry dispense.
The last module on the PPM is the Plate Interface Module (PIM). The PIM collates new and completed plates. In addition, it seals and labels plates.
All of the modules of the PPM work independently. The modules can be thought of as a pipeline. At the beginning the pipeline is not efficient, but as the pipeline fills up, the efficiency of the system becomes great.
At capacity, the Merck Haystack System is designed to have three PPMs. At present, we have two PPMs (Figure I).
Shipping
Completed microtiter plates and completed dry samples are brought to the shipping work station. Shipping provides a mechanism of collating items to be shipped into shipping boxes. Boxes are scanned as they leave the building, providing a record of when boxes are picked up by dedicated carriers. Therefore, all vessels in the system are tracked by PinPoint from the time they are created until they physically leave the building.
Sample flow
Adhoc solution orders received from BRCOS are validated and approved in OSCAR. Although, 99.9% of the dry compound collection is represented in the solution collection, some solution orders require the MRL CMG to weigh and solvate some dry compounds. These compounds are newly deposited samples in the ADS. The OSCAR software automatically places a Build Order, pulling the dry samples from the ADS into a TAP Rack. The Build Order is taken to a weigh station, where a technician weighs an exact amount into a High Recovery Vial (HRV). The HRV is capped, placed into an automation-friendly rack designed to mimic a 96-well plate. The TAP vials are returned to the ADS, and the completed Build Order is taken to the Solubilisation/Replication area. The rack is scanned on a Tecan Genesis liquid handler. The Haystack software retrieves the volume files for the initial solubilisation. After the addition of DMSO, the rack of samples is capped and taken to a sonicator or shaker table, this process insures that all dry residues are completely solvated before the replication process takes place. The CMG makes multiple copies of each solution sample. These samples are used for the initial Adhoc order and the additional copies are used for future screening collections. The registered, filled tube racks are capped on a standalone Capper/Decapper station before being taken to the Haywagon Association Station. Samples for Adhoc requests are located in a separate Haywagon to be docked at the Working Solution Store. Samples for future screening collections are located in another Haywagon and docked at the Archive Solution Store.
Once the Build Order is complete and all of the Adhoc solution samples are located into the WSS, the initial solution order is approved. An empty Haywagon containing empty Matrix Tube Racks is docked at the WSS. Then, individual tubes are picked and placed into a Matrix Tube Rack on a Haytray. Each filled Haytray is taken to the 2D Matrix scanner for verification. After the verification step, filled Haytrays are returned to the Haywagon. The filled Haywagon is undocked and samples are thawed by pulling ambient air across the samples.
The thawed Haywagon is docked at a Plate Production Module. Haywagons filled with clean Matrix 5503 tips and BD Deep Well Blocks are docked along side the thawed Haywagon. Matrix 5503 tips are used to minimise cross contamination of samples. BD Deep Well blocks are used to dilute sample requests on the fly. Once all three Haywagons are docked, the PPM software is initialised. The Tray Transfer Robot (TTR) pulls a Tube Haytray and transports the tray to the integrated Capper/Decapper. As the tubes are being decapped, the TTR accesses a Tip Haytray. The Tip Haytray is taken to the Tip Transfer Unit, were the tips are transferred from the Matrix Dart Holder to a metal tip holder that is designed to work with the TAP BasePlate. The Plate Interface Module picks a selected plate from a plate safe and places the plate on a Haytray. The TTR moves this Haytray to the deck of the BasePlate. At this point in time, the BasePlate has already been loaded with Haytrays of uncapped tubes from the Capper/Decapper, clean Matrix tips in metal holders from the Tip Transfer module, and a Haytray of BD Deep Well blocks.
The clean tips are picked up by the BasePlate head and are used to mix the samples creating a homogeneous solution. After the mixing step, a known aliquot size is aspirated and dispensed into a 96 or 384-well plate.
The PIM transfers the samples to the Beckman Plate Labeler for the application of a label with the plate’s unique identifier, the Set_ID. This identifier is used by scientists to identify the plate and its contents — compound_id, volume and concentration. The plate is then shuttled to the AbGene Plate Sealer where a pealable foil seal is applied. The PIM then collates plates based on order type or final destination.
Conclusion
The MRL Project Team set very high acceptance criteria, including accelerated pick and place rates, multiprocessing components, minimum errors, and the ability to run the system with minimal human intervention. The HayStack system has been fully operational for two full years. During the first year of operation, the Working Solution Store picked and placed more than 1 million tubes for ad hoc requests. The first screening collection included the picking and placing of 500,000 samples, making ten copies on the in just under 4 months. During this two-year period, the system has either met or exceeded our expectations for processing samples. That does not mean the system has not had hardware or software problems. It means the Compound Management and Engineering teams work together to keep the downtime minimal, fixing small problems and being proactive on future problems.
References
- Archer, R. History, evolution, and trend in compound management for high throughput screening. Assay and Drug Development Technology 2, 6, 675-681 (2004)
- Collette DeChard Fully Automated Compound Distribution Center LRIG meeting January 2005
- Dalin Nie The AstroZeneca ACMF European Pharmaceutical Review 10 3, 49-53 (2005)