Six Sigma: How Rottapharm is using Lean Six Sigma principles
Posted: 20 August 2013 | | No comments yet
From their headquarters based in Monza, Italy, Rottapharm’s long history of success began in 1961 with the creation of a small laboratory for independent research. The company from its early beginning has continuously invested in research, innovation and development of pharmaceutical products for distribution on a worldwide scale. After acquiring the German multinational Madaus Pharma in 2007, the Group is currently one of the most significant and prominent pharmaceutical companies in Italy and is present in over 85 countries worldwide. The field of research is above all the undisputed true mission of the company.
Rottapharm can boast a rich portfolio of original molecules and drugs, discovered and patented by its own R&D department. From the original glucosamine sulphate, an essential molecule in the treatment of osteoarthritis, to pro-glumetacina, a non-steroid anti-inflammatory drug, up to the launching of the first transdermal active matrix patch with estradiol an innovative transdermal releasing system for hormone replacement therapy in the menopause, research has not stopped but in fact has continued to grow and develop in a steady manner. In the pharmaceutical sector, Rottapharm|Madaus has over 13 projects in its pipeline.
Rottapharm in Ireland
The Rottapharm manufacturing site in Dublin, Ireland was officially opened in June 1999 and commenced manufacturing operations later that year. The Dublin site employs 150 people manufacturing a range of capsules, sachets and tablet formulations in addition to the API Crystalline Glucosamine Sulphate. The company’s leading product DONA, the original Glucosamine Sulphate, is manufactured in sachet and capsule formats for markets in Europe, Asia and South America. DONA is the first drug of choice to be administered as early as possible in the treatment of osteoarthritis.
Production output has grown steadily over the years, with the Dublin site becoming one of the most important manufacturing sites within the Rottapharm|Madaus group of companies. Figure 1 shows the growth in terms of percentage output from 2000 to 2012. The increase in growth from 2009 onwards was as a result of a seven million Euro investment and facility expansion. The investment involved the transfer of a number of new processes from another facility within the group. The project expansion resulted in an addition of four packaging lines, two coating systems and an encapsulation machine. Volumes of finished product packaged increased significantly, as a result and 35 new positions were created. The project was completed in 2010.
Lean Six Sigma and the Operational Excellence programme
In order to improve operations and performance, the Senior Management team at Rottapharm Dublin introduced a Lean Six Sigma program in 2007. Six Sigma seeks to improve the quality of process outputs by identifying and removing the causes of defects and minimising variability in manufacturing and business processes. It uses a set of quality management methods, including statistical methods, and creates a special infrastructure of people within an organisation (Black Belts, Green Belts, etc.) who are experts in these methods. Each Six Sigma project carried out within an organisation follows a defined sequence of steps and has quantified financial targets cost reduction and/or profit increase. Rottapharm has run over 20 Six Sigma projects over the past five years. Typically, these projects were completed on difficult process problems encountered and by the application of Six-Sigma methodologies, an effective means of problem-solving and process improvement could be implemented. These problems were tackled by teams using the Six Sigma approach of – Define the problem, Measure, Analyse, Improve and Control (DMAIC problem solving process). The Six Sigma DMAIC problem-solving approach continues to be used to date, supporting the overall Operational Excellence programme within the plant. The company has also introduced other lean tools and concepts into the business in order to remove waste and drive down costs in the business. Some of these tools and concepts are described below.
Total Productive Manufacturing (TPM)
The lean tool known as Total Production Maintenance or Total Production Manufacturing (TPM) is the main driver of the Operational Excellence programme within the Rottapharm Dublin facility.
TPM is a way of working in a cellular based team structure with manufacturing teams, made up of operators, technician and engineers, supported by various Pillar Champions, usually managers of a particular support function such as materials, maintenance, safety, quality etc. TPM focuses on equipment, the interaction of people with that equipment and the waste associated with the equipment and the various interactions. TPM doesn’t just focus on equipment alone; all other support departments are integrated into the overall structure as their contribution plays a key role in the success of each project. All the waste associated with both the actual manufacturing activity and the support activities are targeted in order to keep costs down and productivity up.


Figure 1. Production output expressed as percentage for year on year comparison
The TPM project at Rottapharm Dublin began in May 2010 with 19 people trained on the nine step TPM improvement plan. Two separate shift teams focused on a manufacturing area while two other shift teams looked at a sachet filling and packing line, each team comprised six members. The teams took 20 weeks using one day a week every fortnight to go through the nine step TPM programme for their project. Each day that TPM was scheduled, production activity was suspended and the teams worked through a programme of activity designed to improve the equipment uptime and performance and remove waste associated with that equipment and the associated interactions. The success of the projects was immense; particularly one associated with a packaging line where a dramatic increase in OEE was obtained rising from an average of 15 per cent to an average of 50 per cent. Fourteen TPM projects have been rolled out to date across the plant. The TPM programme is broken into nine steps:
- Collecting equipment history and performance information
- Defining Overall Equipment Effectiveness (OEE) measurement and potential and reviewing progress
- Assessing the six top losses and setting improvement priorities
- Carrying out a critical assessment of the equipment
- Carrying out a condition appraisal of the equipment
- Planning the refurbishment, spares and manpower to carry out the work
- Developing future asset care
- Developing best practice
- Problem solving and prevention.
At the end of the nine step TPM activity, the teams present a close out to Senior Management and then progress onto an ongoing Continuous Improvement phase, the teams meet every week for two hours reviewing performance and performing various activities focusing on improvement and reducing waste. In order to ensure that progress is maintained there are eight levels of assessment that each team must achieve as the team progresses on their journey. The teams start to become self empowered and self managing of all activities within their influence. The TPM tool is very much a cultural change tool and the benefits of this rather than as an equipment or maintenance tool becomes evident after implementation and using the tool over a period of time.
Total Productive Administration
In September 2012, based on the recognition that the cellular based structure of TPM was successful both in terms of achieving better KPIs and developing a culture of Continuous Improvement among cross functional departments, it was decided to introduce the concept of Total Production Administration (TPA) into the support functions at Rottapharm Dublin.
Four project areas were chosen, Quality Assurance (QA), Quality Control (QC), Finance and Materials. The teams selected were drawn from members of those departments along with members from other process and support departments to provide an external insight to the team and offer a new perception to the project in question. The tool used by the teams was process mapping whereby the teams used the brown paper method to:
- Review existing process activities
- Remove non-value adding activities
- Develop a new improved process with the wasteful activities removed.
In one example, the QC team reduced non-test task activities from a total time of 39 hours to 16.5 hours, a 58 per cent saving of time for a QC analyst to perform more value adding tasks.
Paperless projects
The lean paperless projects, which began in 2009, have transformed the operations and maintenance systems within the Dublin site.
Paperless maintenance involved the installation of a Computerised Maintenance Management System (CMMS) to support timely and accurate information on maintenance activities within the plant. The system was installed and validated to CFR 21 standards within six months. Data access and inputs are performed by Rottapharm maintenance personnel using military standard laptops.
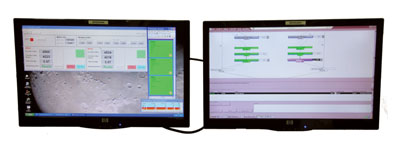
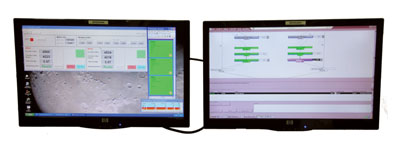
Rottapharm designed automation program for automatic enforcement of in process checks and the MES electronic batch record screen
The CMMS enables maintenance activities to be logged as they occur. In conjunction with an Overall Equipment Efficiency (OEE) system integrated to the equipment, real-time information on equipment performance can be generated and a range of KPIs were developed for performance review. The CMMS and OEE systems are also linked which allows meter based maintenance activities with actual running times determining routine maintenance requirements.
The Manufacturing Execution System (MES) is a software application which manages various operations on the factory floor. The MES implemented at Rottapharm includes numerous interfaces with plant equipment. The project started in the warehouse in 2009 and has now been rolled out to over 95 per cent of the manufacturing and all packaging activities. This means that batch records are now electronic rather than paper-based. Over 800,000 wet signatures have been removed as a result of this project. This ensures a reduction in processing errors and allows a faster batch review time through the use of ‘review by exception’ taking place. Paper has all but disappeared within the production and maintenance environment of the company.
Energy reduction
Rottapharm has taken steps to improve the energy efficiency of the business over the last number of years. The primary reasons for this have been to reduce the emissions of Green House Gases, Carbon Dioxide (CO2) and also to reduce the overhead costs of electricity and natural gas. Green House Gas CO2 emissions have dropped from a high of 4685.8 tCO2 in 2010 to 3207.3 tCO2 in 2012. Energy consumption dropped by 44 per cent between 2010 and 2012 with relatively similar production output of packs of 20.9 million in 2010 and 20.5 million in 2012.
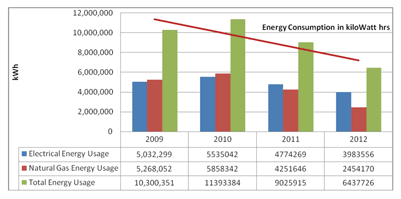
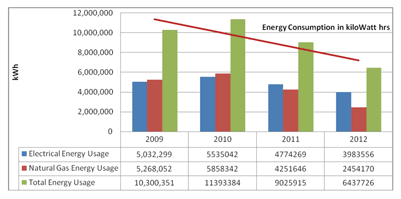
Figure 2. Rottapharm Dublin energy consumption in kilowatt hours (2009 to 2012)
The energy awareness project team have also introduced a number of energy reduction projects over the last number of years, targeting some of the significant energy users, which has resulted in reduced consumption of electricity and natural gas, these are listed as:
- The recirculation of air in the Heating Ventilation & Air Conditioning (HVAC) system
- The installation of occupancy and daylight sensitive lighting controls in corridors
- The optimisation of the chilled water plant by raising operating temperature and improving control of the chilled water plant units
- The optimisation of the Building Management System (BMS) in order to control heating requirements in times when areas are unoccupied
- The phased installation of Light Emitting Diode (LED) lighting in the facility.
The Green Shoots Awards Competition
The Green Shoots Awards Competition came about as a result of the need to promote energy and waste awareness within the Rottapharm plant. The competition was launched on World Environment Day, 5 June 2012.
The competition was successful in engaging employees in suggesting ideas for both energy and waste reduction. Over 140 ideas were submitted to the competition and through a process of elimination this figure was shortlisted to 12 finalists. Each of the finalists was assigned a sponsor to aid them in preparing a more detailed explanation of their idea. The 12 detailed entries were then judged by Senior Management and members of the green shoots awards committee. The overall winner of the competition was selected along with the category winners for the best energy and waste reduction ideas. The winning energy reduction entry was to examine what equipment etc. could be switched off during off peak periods for the whole plant. The waste reduction winning idea was to install MES screens on the warehouse turret trucks to speed up stock location. The overall winning idea was establishing a CRS standard Spectrum for all raw materials in the QC laboratory.
The winners were announced on 19 December 2012 and all 12 finalists received a prize. The ideas suggested, for energy and waste reduction during the competition, have already started to be implemented across the plant.