Embracing automation in sterile manufacturing
Posted: 6 December 2023 | Caroline Peachey (European Pharmaceutical Review) | No comments yet
Krishna Venkatesh, Global Head Sterile Operations at Dr Reddy’s Laboratories discusses how and why the pharma industry is embracing automation.
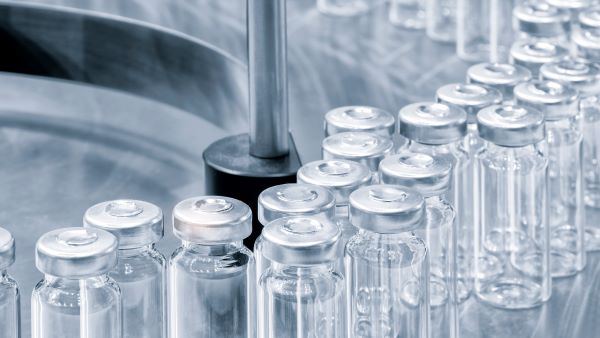
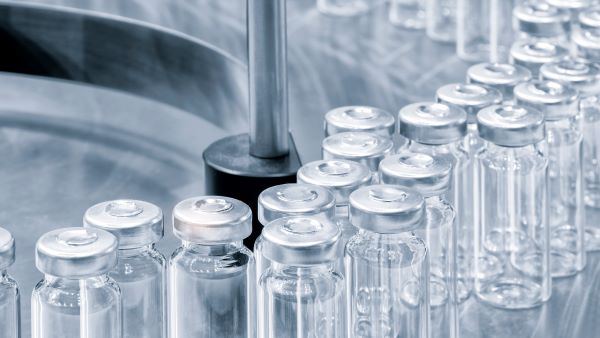
In the interview, conducted at CPHI Barcelona, Krishna Venkatesh, Global Head, Sterile Manufacturing Operations at Dr Reddy’s Laboratories explores industry’s growing focus on achieving end-to-end connectivity, as well as the potential of automation and track and trace solutions.
Venkatesh, who is responsible for sterile injectable manufacturing and operations within Dr Reddy’s global organisation, also emphasises the role of data analytics, artificial intelligence, and low-cost automation in sterile manufacturing.
Elaborating on supply chain disruptions impacting sterile injectables, Venkatesh explains how the supply of e.g. packaging material and filters has not yet caught up demand following the pandemic. He also shares some lessons from Dr Reddy’s efforts to increase automation of its manufacturing processes, and approaches for handing data.
Finally, the interview delves into the complexities surrounding the adoption of track and trace technology as an anti-counterfeiting measure. Although many countries have embraced this technology, Venkatesh says “significant work” is needed to perfect it.
What trends are you seeing in the pharma space?
Krishna Venkatesh (KV): I think, working to improve timeliness, cost, and good quality products is very important. These are key areas that are always on trend.
Packaging solutions for track and trace are becoming increasingly important and can be considered emerging trends”
Next is ensuring end-to-end connectivity of information from the point of manufacture to when it reaches the customer. Many markets have now completely embraced track and trace. Packaging solutions for track and trace are becoming increasingly important and can be considered emerging trends.
Of equal importance is ensuring that we have products that give us consistent margins, while being able to clear the required regulatory hurdles to get approval and get the products out to the market as soon as possible.
I do see increased attention on automation, too, for its ability to bring costs down, as well as anti-counterfeiting technologies.
Can you elaborate on the main technologies or innovations that have the potential to drive down costs?
KV: We have seen two specific elements. Historically, pharmaceutical manufacturers have built sufficient capacity so that they can leverage sudden surges in demand. But if those demands do not pan out, due to additional competition or if there is customer consolidation, then those capacities can actually increase the cost of manufacturing owing to your operational expenditure.
One of the elements to consider is how to ‘de-bottleneck’ and bring operational excellence elements into our manufacturing processes. [This ensures] that it is used in an efficient manner and where it isn’t used, there is capability to either shut it down or start manufacturing other products to offset the operational expenditure.
Once you organise data in a meaningful manner, algorithms, programs, data analytics and artificial intelligence can indicate which solution will bring the greatest value”
There are multiple elements that we look at. The first is cutting down waste and rejection. This includes looking at how digital solutions can help to identify areas where we are not efficient; implementing solutions around them – either digital or technical – and using these data to analyse areas where we are inefficient. Often these datasets are multidimensional. It is not easy for a human being to look at data in a multidimensional manner and deploy solutions. But once you organise these data in a meaningful manner, then algorithms, programs, data analytics and artificial intelligence can largely indicate which solution will bring the greatest value…
So, I think, using analytics to look at data, in terms of how to use it in an automated manner with AI or deploying feed-forward information in real time, enables these solutions to be deployed so that we can reduce manufacturing time, remove inventory, reduce logistics time, but more importantly, reduce wastage and reduce rework. I think these are areas that are very important.
What do you consider are the challenges with managing data?
KV: When we went through the process at Dr Reddy’s we would often deploy a sensor or a simple data acquisition system
A mistake that some companies make is to say, ‘let me master acquisition, and then I’ll deploy analytics’. You will never master acquisition because it’s a continuous process. Acquisition and analytics go hand in hand. You get the data, you deploy analytics; you learn the data you have is not sufficient, so you employ additional sensors, you add additional data acquisition systems, then you deploy additional analytics. It builds up in layers and that becomes very important.
Good data that doesn’t require enormous amounts of massaging, or cleaning is vitally important. Once you have the data, there are numerous smart people and smart programs out there that can quickly point you towards next steps.
80 percent of time spent on data analytics goes on cleaning data…. That’s a huge waste of time”
Some estimates indicate that 80 percent of time spent on data analytics goes on cleaning data; or more than 80 percent. That’s a huge waste of time. So, understanding how to get the data you want, and putting the right sensors in place represent the biggest challenge.
Can you identify any specific trends that are impacting sterile manufacturing?
KV: With the impact of COVID we’re seeing that in certain areas the times for obtaining primary packaging materials are skyrocketing. If you look at sterile filters, there is limited capacity, and it takes a long time to install new capacity. The filters were being used for vaccines – rightly so – but supply has not caught up with the demand that is there. So, we’ve been having issues there.
Some of the primary packaging material has enormous lead times so we’re having to stock up on inventory”
The second issue is with primary packaging material. Some of the primary packaging material has enormous lead times so we’re having to stock up on inventory.
The third issue in sterile manufacturing is the impact of human beings. Because we carry the biggest microbiological load, any place that we move around in, we’re moving an enormous biome.
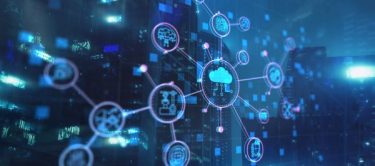
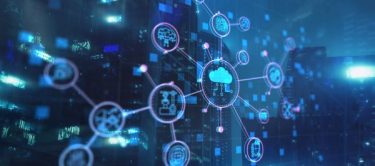
Embracing automation remains a challenge
The challenge is how to continuously automate our systems, make our systems more robust and to move from equipment maintenance that is based on breakdown all the way up condition-based predictive maintenance. Technology exists today that will stop you from making a mistake. But unless you understand how to operate, maintain and run the technology, that’s of no use.
There is so much that is interconnected; so many drives that are automated and that we need to understand. So, having capability in engineering, programming and automation is the future – this is extremely important.
We are moving away from a domain which is pharma to a domain that is actually digital engineering. Thus, we are hiring more engineers. In our manufacturing, we have a highly automated system. But, if you don’t know how to maintain it, you can make a mistake and not even know about it, which is very dangerous. These are areas in automation that are challenges as well as opportunities, but I think we continue to learn from them.
Please elaborate on the use of track and trace anti-counterfeiting technology…
KV: I think one of the biggest concerns for regulatory agencies across the world are the intermediaries who can actually syphon off products and then pass them off as genuine product. This counterfeiting is a huge issue, especially when it moves across state and country borders.
Many countries have now embraced track and trace – that goes from the unit packaging to the secondary and tertiary packaging”
With the advent of drugs being sold by mail order, for example, via numerous e-dispensaries, there is significant risk that what you order is different to what you receive. Consequently, many countries have now embraced track and trace – that goes from the unit packaging to the secondary and tertiary packaging, so that you know there is adequate control and a thread that ties everything up. But those [solutions] are not that easy to deploy and such technology takes investment to achieve.
When countries embark on this track and trace process, they each have their unique [requirements] for how data needs to be transmitted to them. The data ultimately belongs to the market, they do the scanning, and then access the data from our systems. Track and trace is a fantastic way to protect the consumer, but from a pharmaceutical manufacturing standpoint, there is significant work needed to perfect that.
About the Interviewee
Krishna Venkatesh is Global Head, Sterile Operations at Dr Reddy’s Laboratories
Related topics
Aseptic Processing, Big Data, Continuous Manufacturing, Data integrity, Manufacturing, Packaging, Process Analytical Technologies (PAT), Vaccines