Simplify, standardise, digitalise to transform manufacturing
Posted: 23 December 2022 | Arnaud Robert (Sanofi), Brendan O’Callaghan (Sanofi) | No comments yet
Here, Sanofi’s Arnaud Robert and Brendan O’Callaghan explore how advances in digital technology, partnerships and new ways of working are supporting manufacture and delivery of medicines for patients across the globe.
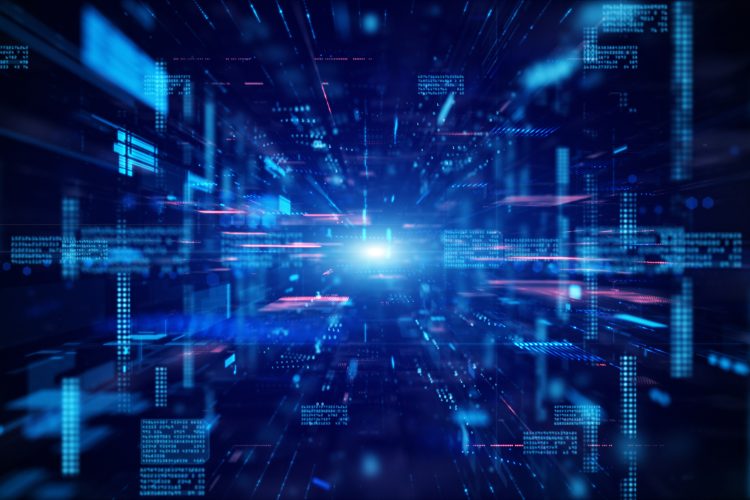
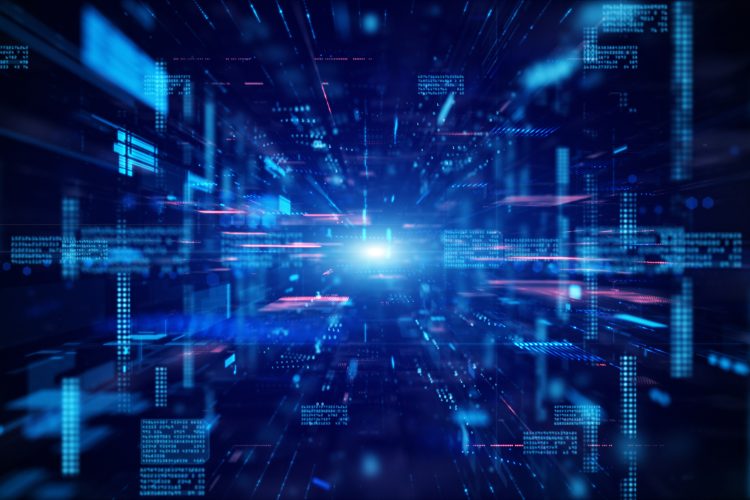
With over 90,000 employees across the globe, Sanofi supplies over 5 billion doses of medicines and vaccines every year, supporting the health needs of millions of patients in more than 170 countries.
This responsibility has increased significantly in recent years, due to the COVID-19 pandemic; the war in Ukraine; rising energy costs and inflation and the increase in geopolitical tensions globally – all of which are creating unprecedented upheaval and disruptions to global supply chains.
To navigate these challenges and succeed in this increasingly VUCA (volatility, uncertainty, complexity and ambiguity) world, we need to simplify / standardise / digitalise: challenge all our existing processes, streamline operations across our sites and leverage our digital capabilities. We need to exploit the vast amounts of data we capture and derive insights that enable faster decisions, and optimise performance and reliability. This will not only transform the practice of medicine, but will transform ourselves as an organisation. Our ambition is to build a modern, industry-leading manufacturing network, by bringing together talented people and cutting-edge processes, technologies and data to reliably deliver high quality, affordable and sustainable medicines and vaccines to patients.
Simplify systems, applications and processes
In a global company built from many mergers and acquisitions (M&As) over the years, we have inherited many different legacies, including mindsets, ways of working and a wide variety of systems, applications and processes. On the data front, we have successfully generated and collected data from numerous applications; however, we have fallen short on sharing data across the organisation and deriving insights. We have had many different and incompatible data solutions, adding a technical complexity to the equation.
“Deployment of electronic batch records, enabling computer-assisted batch reviews, have led to a decrease in batch review cycle times from 10 to two days”
To address this, we’re focused on two aspects: mindset and tools. First, we are adopting an agile mindset across the business: in 2021, we upskilled over 16,000 Sanofi employees – with courses offered for different levels, with an emphasis on an agile mindset, not just the methodology. This new shared knowledge is what allows us to innovate faster today. Second, we developed with a partner a mobile application called Plai, that displays our key performance indicators (KPIs) across the company, from research to manufacturing to commercial. Plai has been a driving force to glean the relevant and important data, embrace data transparency and become a more data-driven organisation adept at generating and analysing the wealth of data at our fingertips. We have created an environment where we can celebrate successes and discuss areas of improvement across the board, without functional silos. We even incorporated a layer of gamification to motivate our leaders to improve KPIs.
While the technical solution behind Plai is relatively straightforward – albeit involving a lot of work – catalysing the cultural shift, a key driver for collective success, is not as straightforward. While there was some initial reluctance about sharing KPIs across the company – some employees were concerned about a loss in autonomy and an increase in top‑down monitoring – our employees soon began to see data transparency as an opportunity. For example, a manufacturing site leader can see positive trends at another site, connect with peers and apply the learnings to improve his/her own team’s performance. Each site is strong, but our network is even stronger once we collaborate and work together with a ‘One Sanofi’ mindset and common datasets.
Standardise manufacturing
We are also partnering with the McLaren Formula One team to help standardise processes, streamline performance and advance our ability to innovate. Through this close collaboration between the McLaren team and our digital, manufacturing and supply teams, we are accelerating the efficiency and performance of our global network to attain world-class standards of manufacturing excellence. By embracing its racing spirit, McLaren brings experience in precision engineering and data analytics to help us optimise performance for better throughput and capacity utilisation.
Focusing on a scope of 130 lines in 14 sites, this has enabled us to reach almost 30 lines to date, achieving 60 percent Overall Equipment Effectiveness (OEE), with an overall performance improvement of 16 percent over the last 18 months across our global network. This has enabled most of our sites to achieve top decile performance.
Another example, the deployment of electronic batch records, enabling computer-assisted batch reviews, have led to a decrease in batch review cycle times from 10 to two days. With such improvements, we can be more reliable, efficient and effective suppliers, maximising the reach of our medicines and vaccines to patients.
Digitalise manufacturing: artificial intelligence and machine learning
This is only the beginning – our ambition is much bolder. In the future, predictive artificial intelligence (AI) will monitor every step in our manufacturing processes. Through machine learning (ML) it will feed back into the system and simultaneously adjust or improve based on real-time data inputs. We will build self-healing processes where data and algorithms can influence and optimise our operations in real time without human intervention. Collecting precise data will be key in producing optimum yield, avoiding potential disruptions, and producing more of our medicines, faster, more reliably and at higher quality for the benefit of patients.
Data generated in our plants serves more than just our manufacturing operations. We share this data with the wider organisation through our internal, AI-driven search engine called OneSearch. This enables employees from across the company to tap into manufacturing and other relevant datasets, enabling smarter, data-driven decision making, to ensure the best actions are taken for all activities of our value chain, from R&D to commercial.
Democratising data – from accessibility to insights to automated action – has been a key step in our digital transformation, creating a successful digital organisation that enables us to do more for patients.
“In the future, predictive artificial intelligence (AI) will monitor every step in our manufacturing processes. Through machine learning (ML) it will feed back into the system and simultaneously adjust or improve based on real-time data inputs”
We are applying the same digital and data transformation across the board.
For example, in R&D we use data and AI to find new targets; design new molecules, messenger RNA (mRNA) sequences and lipid nanoparticles (LNPs); automate several processes based on sophisticated image recognition; and leverage digital twins to design, implement, qualify and operate modular operating lines at our Evolutive Facilities (EVF) in France and Singapore.
As another example, we have standardised our key commercial applications across the globe – a Herculean task. We are now able to innovate at speed and at scale, using data and AI to suggest the best content on the best communication channel to our healthcare professionals (HCPs), have a real-time, 360 view of HCP engagement, and find new HCPs that have patients that could benefit from our treatments.
The digital transformation journey is not an easy one. We are taking ambitious steps to simplify, standardise and digitalise a large multinational company working in a highly regulated industry. Moving from an individual to collaborative mindset within an organisation built on a history of M&As provides an added challenge.
As an industry, we have an obligation to do the best by all the patients we serve. To achieve this, we will continue to collaborate openly across our digital and manufacturing teams to build a data‑driven network that is constantly improving.