Building CO2-neutral, defossilised supply chains for chemicals
Posted: 21 December 2022 | "Stefan Koenig (Roche), Jan Backmann (Roche), Martin Held (Institute of Biotechnology of the Swiss Federal Institute of Technology) ", Martin Olbrich (Roche) | No comments yet
Manufacturers of (bio)pharmaceuticals, medical devices and in vitro diagnostics have the opportunity to lead the way in the defossilisation of organic chemicals. Here Martin Held from the Institute of Biotechnology of the Swiss Federal Institute of Technology and Roche’s Stefan Koenig, Martin Olbrich and Jan Backmann propose how to reduce the environmental footprint of the pharma industry by establishing a market and infrastructure for the large-scale production of defossilised organic chemicals, benefitting other industries too.
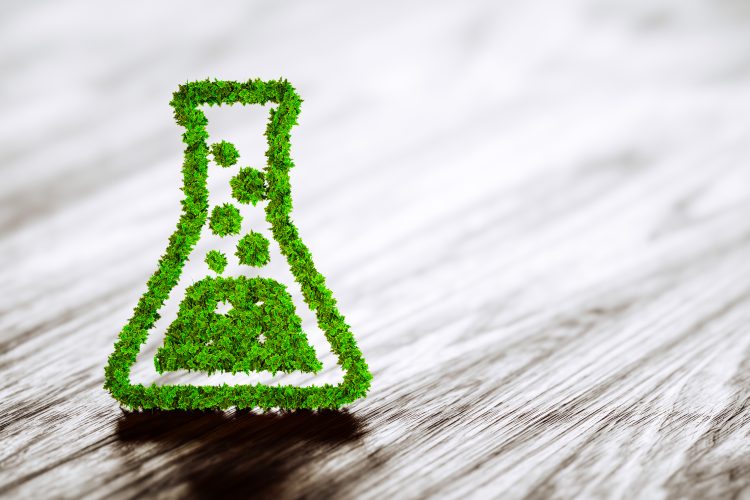
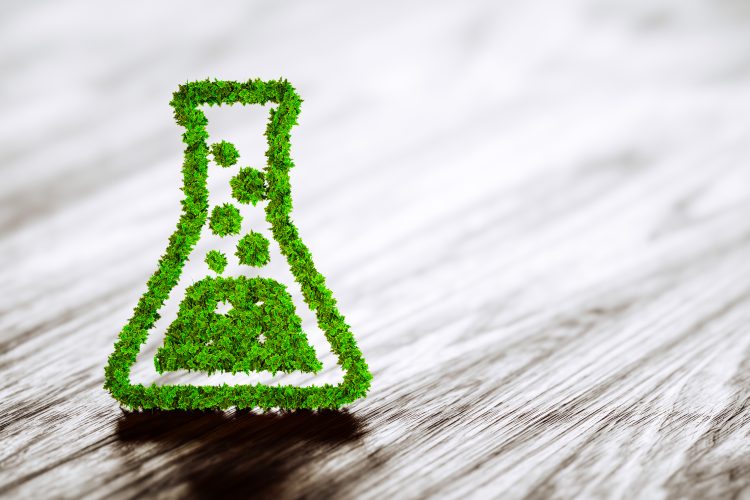
The healthcare industry is successful in innovating new treatment paradigms ranging from small molecular to biological therapeutics to personalised medicines.1 Over the past quarter century, the industry has increasingly adopted green chemistry practices in a continuing effort to improve process efficiency and reduce its environmental footprint.2 However, most of these efforts relating to catalysis,3 process waste metrics,4 lifecycle assessments,5 pharmaceuticals in the environment6 and the phase out of substances of concern7 mainly mitigate the consequences of pharmaceutical manufacturing. They do not address the underlying issue responsible for global warming, namely that almost all organic chemicals including plastics originate from fossil resources.8,9
Organic compounds are arguably the foundation of the pharmaceutical industry. All traditional small molecule pharmaceuticals include carbon building blocks”
Organic compounds are arguably the foundation of the pharmaceutical industry. All traditional small molecule pharmaceuticals include carbon building blocks – by definition, organic materials – which are then transformed via modern synthetic chemistry to assemble the complex and highly variable skeletons that the final target structures demand.10 Diagnostics and biologics also heavily utilise carbon-based materials as constituting building blocks, processing aids, single-use reactors, or packaging materials. Currently, these organic compounds including plastics predominantly originate from fossil carbon derived from mineral oil, natural gas, or coal and are converted into carbon dioxide (CO2) and other decomposition products released into the atmosphere during production or at the end of life of the manufactured goods or auxiliaries.
Production of defossilised organic chemicals and materials
The mitigation of global warming urgently calls for CO2 neutrality, which can be reached if the carbon flux is closed. The transition to a closed carbon flux we call defossilisation. Organic materials have several routes through which defossilisation could be achieved:
- Recycling
- Synthesis from biomass
- Carbon capture and utilisation (CCU).
Recycling is well established for standardised processes like solvent regeneration or polyethylene terephthalate (PET) recycling in commercial manufacturing and will continue to play a key role in the circular economy.11 Recycling also has great potential, but there are significant limitations due to the high quality requirements and regulatory barriers (eg, for unused medicines).12 In the vast majority of all cases, if ever, only thermally or chemically recycled materials can hence be used.13,14 Beyond the core theme of this article, it is worth mentioning that recycling is specifically crucial for inorganic catalysts (and other materials) so that further environmentally destructive mining and landfilling are avoided.15
Defossilised organic chemicals are increasingly the focus of the industry and there are promising alternatives like new solvents being marketed”
Organic chemicals from renewable resources (so-called defossilised organic chemicals) are increasingly the focus of the industry and there are promising alternatives like new solvents being marketed.16,17 However, care must be taken to ensure that chemicals from biomass are not produced in competition with food production and do not have a negative impact on the environment or natural habitats. Consequently, byproducts of existing value chains or biotechnological methods with rather slim land use are the only methods to be used long-term.
CCU has considerable unexploited potential. It starts with capturing gaseous oxidised carbon (CO2 or CO) ideally from concentrated point sources, eg, waste incineration, cement works or biogas power plants, and thus actively prevents it from entering the atmosphere. The captured carbon is then transformed into high-value organic chemicals that can then be used as feedstock for product manufacturing.18 CCU can hence be operated without any carbon derived from fossil fuels. This advantage comes however at the expense of considerable power or heat requirements for the production of chemical reduction equivalents (eg, hydrogen) required for recharging the CO2-derived carbon atom with electrons.
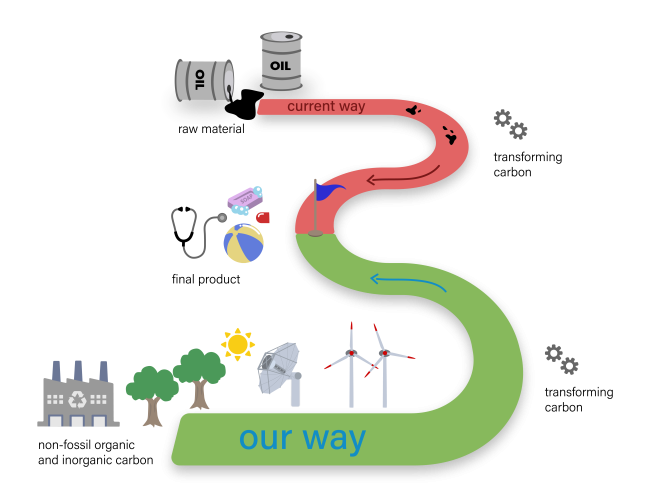
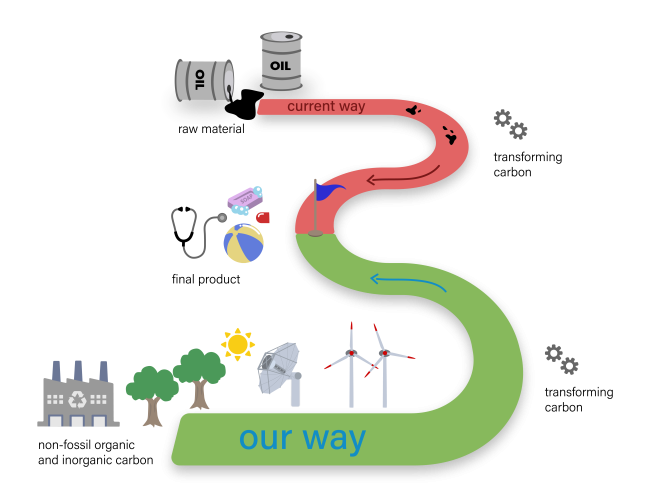
The goal of defossilisation is to shift material sourcing away from fossil resources (red) to non-fossil resources, including carbon dioxide, biomass, or recyclate (green path). Figure courtesy of ccloop.ch
All the above-mentioned routes allow reduction of greenhouse gas emissions. In addition, defossilisation avoids the destruction of natural resources and habitats through the extraction of natural resources. At the same time, dependence on the volatile and unreliable fossil raw material markets and on raw material-based autocracies are reduced.
Challenges of producing defossilised organic chemicals
There are currently several challenges to be overcome to achieve large-scale provision of defossilised organic compounds”
There are currently several challenges to be overcome to achieve large-scale provision of defossilised organic compounds. Sourcing of defossilised raw materials is currently made more difficult as standard databases and systems do not provide information about how much coal, crude oil or natural gas is used to produce a given organic chemical or plastic. Beyond this lack of transparency regarding the source of raw materials, comprehensive end-to-end information about the manufacturing process and energy sources must also be considered to prevent regrettable substitutions from a sustainability perspective and to avoid falling into the trap of greenwashed products.
Despite the fact that the origin of chemicals is already addressed in the Green Chemistry Principles devised by Anastas and Warner,19 awareness of this topic throughout the chemical industry is still limited. Defossilisation of pharmaceutical supply chains has only recently been assessed for the first time.9 In particular, the option of CCU is not widely considered. As such, ccloop, a cross-industrial collaboration of Swiss companies and international information platform, was recently founded with the mission to increase awareness and initiate activities to drive CCU implementation.
While there has been significant progress in the field, CCU capacities are still small and organic chemicals from CO2 are scarce. Large-scale manufacturing of defossilised chemicals like methanol could create a segue for a CCU industry and represent a first milestone. The advantages are that the basic technology and process for methanol refinement to more sophisticated commodity chemicals is in place and that methanol as such is used in many different fields. In addition, the emerging Power-to-X technologies (also known as PtX or P2X) are an important starting point for a broadening range of defossilised organic substances.20,21
“As the contribution of costs of organic chemicals used as feedstock to the operating expenditures is small, the pharmaceutical companies can spearhead and guide the transition.”
The economic models for the transition to defossilised chemistry still need elaboration. However, it is already clear that the investments will be gargantuan. In order to justify them, the future infrastructure and facilities must be written off over decades. Furthermore, entire value chains must be redesigned and the CO2 emitters (especially point source emitters), chemical industry and power sector, downstream users, eg, healthcare industries and their customers, and healthcare providers need to be coordinated, informed, sensitised and must work out contractual frameworks to de-risk the investments. Therefore, costs for defossilised organic substances (including plastics) will initially be higher than for the conventional fossil-based counterparts but will come down in time once the virtuous cycle of increased demand stimulating scaling and innovation is started. As the contribution of costs of organic chemicals used as feedstock to the operating expenditures is small, the pharmaceutical companies can spearhead and guide the transition.
Another challenge is that the entire field of real-zero CO2 chemicals is yet to be regulated in a favourable manner by legislation or incentivised by tax instruments. Certification systems designed to reduce the financial burden of buyers willing to pay a premium price for organic chemicals produced from sustainable carbon would accelerate the transition. Similarly, pragmatic technical solutions carefully considering means for integrating defossilised material streams into existing large‑scale facilities of the chemical industry are needed. In light of long due geoeconomic adjustments, one of the most important tasks of advocacy in the near future will be to draw the attention of policymakers and legislators to the challenges and opportunities ahead, and to call for a long-term strategy and close coordination of the energy and chemical sectors.
CCU has the potential to reduce dependence on feedstock produced offshore and also adds value to CO2 as a starting material”
When making near-term decisions, the long‑term strategic impact on the development of the European – and global – economic markets must also be considered. Importantly, CCU guides investments and emitted CO2 into a productive path and holds the promise to close supply chains within economic areas. To this end, CCU has the potential to reduce dependence on feedstock produced offshore and also adds value to CO2 as a starting material. While trusting in the innovative power of the energy sector for CO2-neutral electricity and heat production, implementation of CCU can potentially contribute to business continuity and maintenance of the European manufacturing base and provides an economic incentive to commercially exploit the inherent potential of CO2 as a feedstock. The production of organic chemistry in the vicinity of geographically widespread point sources of CO2, eg, waste incineration plants or cement works, may also harbour structural policy opportunities. Production and value creation can be regionalised and decentralised, which could lead to a more resilient economic structure.
The path to real zero
The lengthy validation of defossilised organic chemicals and plastics for the healthcare sector will take several years.
So, when could the goal of a net zero pharmaceutical industry be achieved? In the context of CO2 neutrality, the years 2030 and 2050 are mentioned as crucial milestones. The year 2030 as a target date for any field is perhaps somewhat overambitious because the scale-up will last until the end of this decade and the lengthy validation of defossilised organic chemicals and plastics for the healthcare sector will take several years.
The year 2050, however, does not seem ambitious enough for an innovative and financially strong industry such as the healthcare industry. We believe that some industry pioneers, the best in class, could and should reach the real zero goal much sooner. It will be important that scaling and validation do not wait for each other, thus creating an unnecessary chicken-and-egg problem.
About the authors
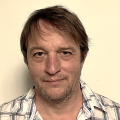
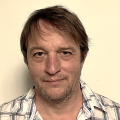
Martin Held graduated as a technical biologist from the University of Stuttgart and received his PhD for the development of a scaled biocatalytic process for the manufacturing of fine chemicals with whole cell biocatalysts from the Institute of Biotechnology of the Swiss Federal Institute of Technology (ETH). He is currently group leader of the Technology Development and Discovery Group at the Bioprocess Laboratory of the ETH. His research activities led to the foundation of five startup companies active in disciplines ranging from drug development to industrial biotech within the past 15 years.
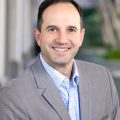
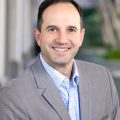
Stefan G Koenig serves as a Distinguished Scientist in the Small Molecule Pharmaceutical Sciences department at Genentech, Inc. in South San Francisco, CA, USA. He joined Genentech after earning his PhD at Yale University, conducting postdoctoral research at the Swiss Federal Institute of Technology (ETH) in Zürich, and spending several years at Sepracor/Sunovion in Marlboro, MA. During his time at Genentech Stefan has advanced several small molecules and new modalities (antibody‑drug conjugates, oligonucleotides and peptides) into the clinic as lead chemist and technical development leader. In addition, he continues to be a passionate advocate for green chemistry as well as greater inclusion within the scientific enterprise.
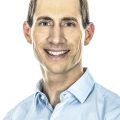
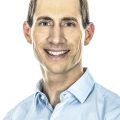
Martin Olbrich obtained his PhD in Organic Chemistry from the Ludwig Maximilian University of Munich. In 2015 he joined the Process Chemistry & Catalysis group at F. Hoffmann-La Roche Ltd, Switzerland, and since then has developed manufacturing processes for complex synthetic molecules with a focus on oligonucleotides. In a matrix role as chemical project lead, Martin coordinates the drug substance activities in cross-functional teams currently handling late-stage development activities for several oligonucleotide projects. Beyond project work, he is currently serving as team lead of the Roche Green Chemistry working group.
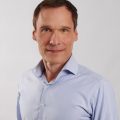
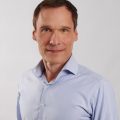
Jan Backmann leads the Chemical Legislation Unit of the multinational healthcare company F. Hoffmann-La Roche Ltd based in Basel, Switzerland. After earning his MSc in Chemistry, he worked at the Robert Koch Institute in Berlin (German Federal Health Office) and completed his doctorate at Berlin Free University. Jan conducted postdoctoral research at the University of Brussels and the Flemish Institute of Biotechnology (Belgium). This was followed by a position at the International Soap and Detergent Association A. I. S. E., located in Brussels. Afterwards, Jan worked at the Swiss contract research organisation RCC Ltd as well as the chemical companies Ciba and BASF. His special interests are in the field of chemical policy and sustainable chemistry.
References:
- Elverum K, Whitman M. Delivering cellular and gene therapies to patients: solutions for realizing the potential of the next generation of medicine. Gene Ther 27, 537–544 (2020). https://doi.org/10.1038/s41434-019-0074-7
- Kar S, Sanderson H, Roy K, et al. Green Chemistry in the Synthesis of Pharmaceuticals. Chem Rev 2022 122 (3), 3637‒3710. https://doi.org/10.1021/acs.chemrev.1c00631
- Bullock RM, Chen JG, Gagliardi L, et al. Using nature’s blueprint to expand catalysis with Earth-abundant metals. Science 369, eabc3183 (2020)
- Roschangar F, Li J, Zhou Y, Aelterman W, Borovika A, Colberg J, Dickson DP, Gallou F, Hayler JD, Koenig SG, Kopach ME, Kosjek B, Leahy DK, O’Brien E, Smith AG, Henry M, Cook J, Sheldon RA. Improved iGAL 2.0 Metric Empowers Pharmaceutical Scientists to Make Meaningful Contributions to United Nations Sustainable Development Goal 12. ACS Sustain Chem Eng 2022 10 (16), 5148‒5162. https://doi.org/10.1021/acssuschemeng.1c01940
- Kralisch D, Otta D, Gericke D. Rules and benefits of Life Cycle Assessment in green chemical process and synthesis design: a tutorial review. Green Chem 2015, 17, 123‒145. https://doi.org/10.1039/C4GC01153H
- Wilkinson JL, Boxall ABA, Kolpin DW, Teta C. Pharmaceutical pollution of the world’s rivers. PNAS 2022, Vol. 119, No. 8.
- Ujaczki E, Stark-Rogel V, Olbrich M, Fuetsch M, Backmann J. Experiences and consequences of phasing out substances of concern in a multinational healthcare company. Environ Sci Eur 34, 101 (2022). https://doi.org/10.1186/s12302-022-00678-0
- Levi PG, Cullen JM. Mapping Global Flows of Chemicals: From Fossil Fuel Feedstocks to Chemical Products. Environ Sci Technol 2018, 52, 4, 1725–1734 https://doi.org/10.1021/acs.est.7b04573
- Wollensack L, Budzinski K, Backmann J. Defossilization of pharmaceutical manufacturing. Current Opinion in Green and Sustainable Chemistry. Vol. 33, February 2022, 100586. https://doi.org/10.1016/j.cogsc.2021.100586
- Clayden J, Greeves N, Warren S. (2012) Organic Chemistry. Oxford University Press, pp. 1–15. ISBN 0-19-927029-5
- Shores BT, Sieg PE, Nicosia AT, et al. Design of a Continuous Solvent Recovery System for End-to-End Integrated Continuous Manufacturing of Pharmaceuticals. Org Process Res Dev 2020, 24, 10, 1996–2003. https://doi.org/10.1021/acs.oprd.0c00092
- European Federation of Pharmaceutical Industries and Associations. EFPIA White Paper on Circular Economy, June 2020. https://www.efpia.eu/media/554663/circular-economy.pdf
- Joseph B, James J, Kalarikkal N, Thomas S. Recycling of medical plastics. Advanced Industrial and Engineering Polymer Research. Vol. 4, Issue 3, July 2021, pp. 199‒208. https://doi.org/10.1016/j.aiepr.2021.06.003
- Healthcare Plastics Recycling Council (HPRC), Advanced Recycling of Healthcare Plastics: An Opportunity for Circularity. https://www.hprc.org/wp-content/uploads/2022/05/Advanced-Recycling-White-Paper-Phase-1.pdf
- Molnár A, Papp A. Catalyst recycling ‒ A survey of recent progress and current status. Coordin Chem Rev, Vol. 349, 15 October 2017, pp. 1‒65. https://doi.org/10.1016/j.ccr.2017.08.011
- Zhang C, Wang Y, Yang W, Zheng J. Biobased 2,5-Dimethyltetrahydrofuran as a Green Aprotic Ether Solvent. Org Process Res Dev 2022, 26, 9, 2685–2693. https://doi.org/10.1021/acs.oprd.2c00136
- Sherwood J, De bruyn M, Constantinou A, et al. Dihydrolevoglucosenone (Cyrene) as a bio-based alternative for dipolar aprotic solvents. Chem Commun 2014, 50, 9650‒9652. https://doi.org/10.1039/C4CC04133J
- Guil-López R, Mota N, Llorente J, Millán E, Pawelec B, Fierro JLG, Navarro RM. Methanol Synthesis from CO2: A Review of the Latest Developments in Heterogeneous Catalysis. Materials 2019, 12(23), 3902. https://doi.org/10.3390/ma12233902
- Anastas PT, Warner JC. Green Chemistry: Theory and Practice, Oxford University Press: New York, 1998, p. 30
- Ramboll website. Power-to-X: paving the way for a greener future. https://ramboll.com/net-zero-explorers/explainers/power-to-x-explained
- International Energy Agency 2022. CO2 Capture and Utilisation.
Issue
Related topics
Drug Manufacturing, Drug Supply Chain, Manufacturing, Supply Chain, Sustainability
Related organisations
Institute of Biotechnology of the Swiss Federal Institute of Technology, Roche