Making the journey to PAT and Pharma 4.0
Posted: 13 July 2021 | David Leitham (AspenTech) | No comments yet
Here, David Leitham, senior vice president and general manager at AspenTech, explains how implementing PAT pushes the industry towards Pharma 4.0.
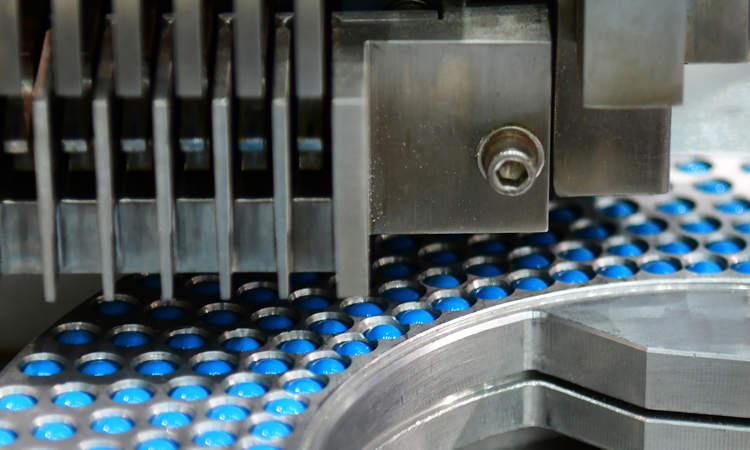
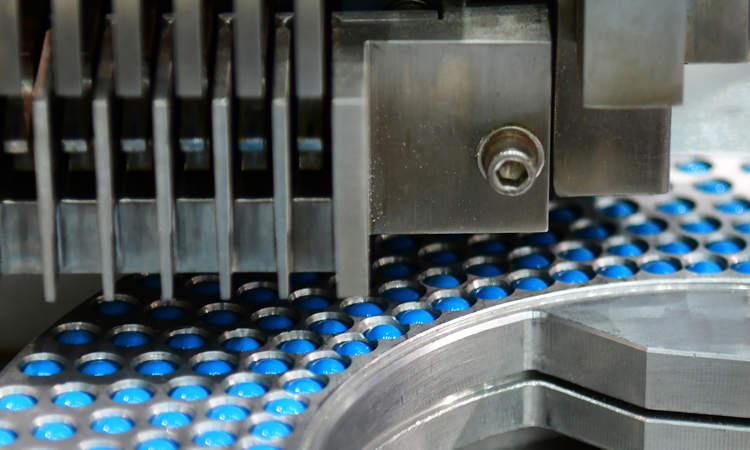
Until recently, the push towards Pharma 4.0 had primarily been undertaken on a project-by-project basis. The focus was on addressing digitalisation by investigating point solutions across the product lifecycle, removing or replacing paper processes, using digital technologies to automate analytics and generally piloting/developing competencies to start a digital transformation.
It has sometimes been a slow process. Pharmaceutical manufacturers have historically found it difficult to embrace change. All pharmaceutical businesses by necessity have well-established, often complex, proven validation processes in place. If a technology has been through this cycle and is working in the manufacturing environment, businesses are often reluctant to take on further ‘evaluation pain’ in a bid to achieve more rapid time to value.
Over the past year, we have seen the process of change accelerate and the industry move ever closer to realising the dream of Pharma 4.0 and escape the loop of everlasting pilot activity. COVID-19 has fast-tracked the drive to speed up broader Pharma 4.0 initiatives, particularly with regards to using innovative techniques and partnerships to bring vaccines to market, supply chain and manufacture, contract organisation integration and other lifecycle elements.
the industry is beginning to shift its focus away from a conservatively academic outlook and on to applied innovation”
With existing manual processes less easy to execute thanks to social distancing, the industry is beginning to shift its focus away from a conservatively academic outlook and on to applied innovation. In this context, many manufacturers are intensely concentrated on reducing supply chain disruption, increasing capacity of batch production and minimising batch losses. Reducing lifecycle maintenance costs and CAPEX remain high on the agenda too. Notwithstanding compliance and safety, manufacturing equipment availability is therefore a top priority.
To address this challenge, we have seen the evolution of predictive and prescriptive maintenance capabilities. The latest asset performance management (APM) solutions leverage such capabilities to enable pharmaceuticals companies to protect their supply chain, increase asset utilisation and avoid unplanned downtime by predicting when equipment anomalies will occur, understanding why they do and prescribing how to avoid potential failures.
Running in parallel, we are seeing solutions driving further efficiencies for pharmaceuticals manufacturers, enabling them to:
- Increase collaboration, from lab to pilot plant to API manufacturing
- Simulate end-to-end batch processes with first-principle models, accelerating regulatory approval and scale-up to full production
- Identify factors impacting product quality and process efficiency using multivariate analytics
The above capabilities offer ideal starting points for pharma organisations looking to quickly gain value and reduce costs through digitalisation. However, in order for organisations to consolidate gains and continuously optimise processes over time, they need to start moving from achieving pockets of efficiency towards more co-ordinated and overarching closed loop solutions, where accuracy is improved over time.
The rise of PAT
Capabilities like predictive analytics for APM and multivariate analytics for monitoring process behaviours that impact batch quality, in particular, will ultimately lead to closed loop Process Analytical Technology (PAT) solutions. For more than 15 years, PAT has been a well-reputed and promising approach to faster, better and more integrated manufacturing processes in pharmaceuticals, ensuring quality though the process versus testing for quality after completion.
The promises and visions associated with PAT have a lot in common with trends like Industry 4.0 and Internet of Things (IoT). While these new trends have placed themselves firmly on the management agenda, PAT has not so far achieved the same attention at the management level. The time is definitely now to change this, as PAT is very much an enabler for digital transformation, and ultimately for Pharma 4.0, in the production and development department of pharma manufacturers.
PAT leverages real-time data and measurements, along with advanced analytics to better understand and to adjust operational processes in order to improve the end quality of the product itself. Moving forwards, it will increasingly become fundamental to the whole pharmaceuticals manufacturing process.
Indeed, we are already seeing this starting to happen today. PAT tools are continuously getting better, simpler and more robust, which, in turn, is helping to lower the threshold for implementation. As little as five years ago, a PAT project often ended up simply as a development project, with no immediate direct commercial benefit. Today, as long as the right application is chosen, a PAT project can be all about implementation – reducing project risk and saving pharmaceuticals manufacturers from a number of avoidable pitfalls and delays.
Whether a manufacturer’s PAT project turns into an implementation or just a development project depends on the planning phase. Choosing the tools and technologies that scale-up and can integrate into existing infrastructure is a must. Next, organisations should also consider the future direction of PAT; to be future-proof, the business will need to choose a PAT system which supports a range of data source types, for instance. Moreover, businesses implementing PAT, should never underestimate either the need for early results to ensure that the benefit of their project is recognised.
Final thoughts
By measuring the results they achieve, manufacturers will attain quantifiable benefits they can build on and scale up over time. It is about providing a robust control environment and secure documentation and compliance and, ultimately, unlocking the value from using PAT in a future-proof commercial environment. Once manufacturers have got that right, they will have gone a long way on the path not just to PAT but also Pharma 4.0. They will have embedded digitalisation into their manufacturing processes; and will be well-placed to monitor and control processes to achieve optimum quality of the final manufactured product.
About the author
David Leitham is Senior Vice President and General Manager at AspenTech. He has 25 years’ experience in the pharmaceutical industry and is responsible for expanding AspenTech’s footprint in the pharmaceuticals market, shaping the product and solution strategy and leading go-to-market efforts. David has demonstrated a track record of success integrating and transforming software businesses and products and growing them at double digits, while leading a software portfolio that drove over one billion dollars in connected sales. Prior to joining AspenTech, David was Vice President and General Manager at Thermo Fisher Scientific, where he was responsible for a team that consistently delivered double-digit growth in software revenue.