COVID-19 vaccines: how important is the vial?
Posted: 8 February 2021 | Hannah Balfour (European Pharmaceutical Review) | No comments yet
In this article we discuss how the problems associated with glass vial packaging may disrupt COVID-19 vaccine distribution and explore some of the latest innovations to overcome it.
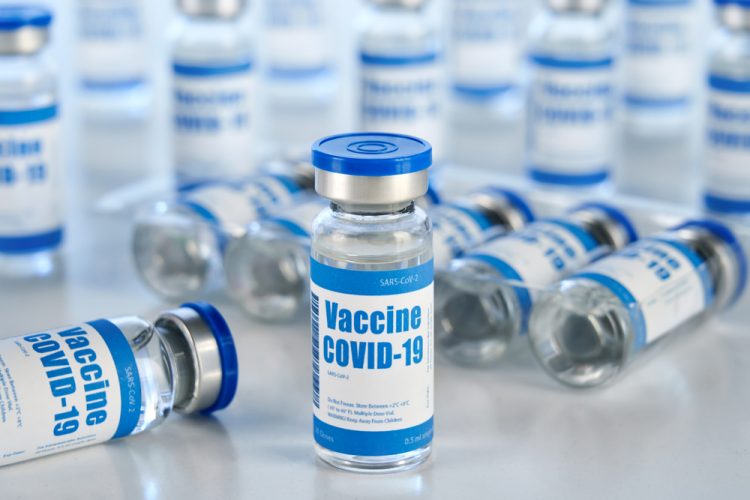
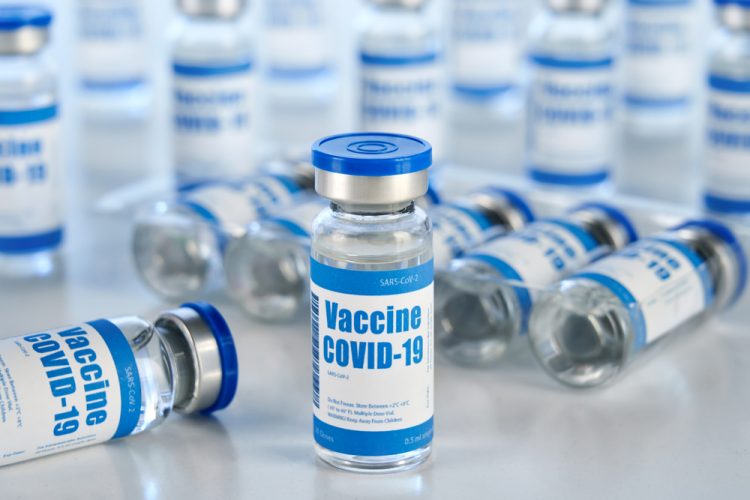
The glass vials into which vaccines and most other biologic drugs are packaged have changed very little in the past 100 years. Traditional borosilicate glass vials have several safety concerns associated with them, from the possibility of breakages to their potential to delaminate. To find out how these issues affect pharma and their possible impact on COVID-19 vaccine distribution, European Pharmaceutical Review’s Hannah Balfour spoke with Lawrence Ganti, Chief Business Officer of SiO2, an innovative materials science company who has developed hybrid vials for biologics.
Ganti explained that glass vials are used in pharma because they provide the best container closure integrity (CCI); a measure of how well a container protects the drug substance from contamination with a variety of factors, including moisture, oxygen and chemicals. He said that while some may think plastic vials are a better option as they do not break, they do not provide an effective oxygen or moisture barrier, whereas glass does. As a result, glass vials are the packaging of choice for most biologics, including COVID-19 vaccines.
Borosilicate glass vials
Most vials used for pharmaceutical packaging are made of borosilicate glass, which was invented in 1897 by German chemist and glassmaker Friedrich Otto Schott. It is primarily composed of silica (80 percent) and boric oxide (10 percent), with a small amount of sodium oxide and aluminium oxide also included. This type of glass has remained popular because it is chemically inert (ie, does not react with what you fill it with), highly resistant to enzymes and is reasonably resistant to temperature changes.1 However, borosilicate glass vials have certain limitations, including that they are relatively heavy, vulnerable to breakages and can delaminate, especially during thermal cycles such as those used in heat sterilisation.
Delamination
Delamination is the primary problem associated with glass containers. Delamination is when the glass vial sheds elements like sodium, silicon and potassium or glass flake particles into the solution it contains. According to Ganti, this weakness of borosilicate glass is responsible for a number of recalls by regulators every year. “The glass flake particles can interact and cause side effects, ranging from a simple skin rash at the site of injection to allergic anaphylaxis or death,” he said. The manufacturing processes involved in producing the glass and the drug product contained in the vial are reportedly the most common causes of vial delamination.
Breakages
Ganti explained that up to six percent of glass vials break during filling, which is referred to as ‘known breakage’. However, it is unknown exactly how much breakage occurs while these products are distributed. “This could be anywhere from less than one percent in established markets to upwards of 10 percent in emerging markets. From my experience, it really depends on the country and environment. For example, I found that India, China, Southeast Asia or Latin America had more breakages than in the US and Europe. I believe this is because the more sophisticated markets are better prepared and have different infrastructure – for instance, the roads are higher quality and they use different types of trucks or planes for distribution.”
Ganti added that the issues surrounding breakages also increase with extreme temperatures: “As glass reaches an extreme temperature, particularly an extremely cold temperature, there tends to be weakening of the material. While borosilicate vials have been strengthened over time to resist temperatures around 0°C, once you reach temperatures like -20, -50 or even -70°C (as is required for the Pfizer-BioNTech vaccine), you start to see a significant increase in the amount of breakage. Our tests have shown that freeze-thaw cycles, where the vial is repeatedly cooled and heated, increase the breakage rate of borosilicate glass vials to anywhere between 18 and 25 percent.”
How could breakages impact COVID-19 vaccine distribution?
“Breakages result in a lot of wastage, not just in terms of the vials but also the product contained within,” remarked Ganti. “The types of products usually packaged in vials tend to be more sophisticated biological products that require low temperatures, like the Pfizer vaccine, and therefore tend to be more expensive. In the context of COVID-19 vaccines, where there is such high demand and every vaccine produced is needed for the population, breakages become more of a concern.”
What has been done to overcome these issues?
While all glasses used in pharmaceutical packaging are mostly made up of silica (ranging from 59 to 80 percent), they vary in which oxides they include, eg, calcium oxide, sodium oxide, aluminium oxide, barium oxide, boric oxide, potassium oxide and magnesium oxide. In recent years companies have been developing alternatives to borosilicate vials to improve breakage and delamination rates.
Valor® Glass
Valor® Glass (produced by Corning) is one example of a recent innovation in pharmaceutical glassware. It is as aluminosilicate glass – the boric oxide of borosilicate glass is replaced with aluminium oxide – which was designed to be stronger and more resistant to breakages than its predecessor. According to its developers, where borosilicate glass breaks under 20kg of force, Valor glass is 50 times stronger, withstanding over 450kg before breaking. Additionally, in freeze-thaw testing, the company says that their vials are over 40 times less likely to break.2
The enterprise has revealed that this toughness comes from the vials being submerged in a brine bath after being cut and shaped. During this process, potassium atoms contained in the bath replace sodium atoms in the glass, fortifying the vial. They are also coated with a polymer that reduces the friction between vials on the production line.
We have never seen so much change in such a short period of time, from vaccines with completely new mechanisms of action to innovations in containers”
Valor glass is still vulnerable to breakages if placed under sufficient pressure, but it is designed to incorporate tension layers and compression layers, so cracks that occur in the tension layer cannot propagate through the rest of the vial as they do in borosilicate glasses.
In June 2020, Corning received a $204 million grant from the US government to expand manufacturing of its Valor vials so they could be used for COVID-19 vaccines under the Operation Warp Speed initiative. Valor glass has been accepted into the US Food and Drug Administration (FDA)’s Emerging Technology Program and in May 2020, Pfizer signed a multi-year supply deal with Corning. The supply will provide containers for a portion of Pfizer’s currently marketed injectable drug products, subject to regulatory approval.
Hybrid vials
SiO2 has developed a new ‘hybrid vial’ by coating the inside of a medical grade plastic container with a nano-layer of pure silicon dioxide (SiO2). Ganti commented: “The nano-layer is 50 times thinner than a human hair and cannot be seen by the naked eye. While these containers may look like and provide the same CCI as glass, if you hold one, it feels 30 to 40 percent lighter and you can throw it against a wall or drive a Hummer over it without it breaking.” He added that these hybrid vials also have a very low risk of delamination, with a sub-visible particle rate approaching zero.
In June, SiO2 was also awarded a grant by the US Government worth $143 million, to enable them to manufacture their hybrid vials for use in COVID-19 vaccines.
What other factors might hold back COVID-19 vaccine distribution?
Commenting on the current pandemic, Ganti said: “We have never seen so much change in such a short period of time, from vaccines with completely new mechanisms of action to innovations in containers. Many people in the pharmaceutical industry are afraid of change or trying new science or technologies and consumers are also afraid of trying new things. I think the only thing preventing a successful COVID-19 vaccine roll out is going to be fear. The fear of change.”
References
- Nasa P. A REVIEW ON PHARMACEUTICAL PACKAGING MATERIAL. World Journal of Pharmaceutical Research. 2014;3(5):344-353.
- Chapman C, Flynn C, Hoff K. Corning Valor® Vials Demonstrate Superior Performance by Resisting Breakage During Low Temperature Processing [Internet]. Corning Incorporated; 2019 [cited 14 January 2021]. Available from: https://www.corning.com/media/…
Related topics
Biologics, Distribution & Logistics, Drug Safety, Packaging, Research & Development (R&D), Vaccines
Related organisations
BioNTech, Corning Life Sciences, Pfizer, SiO2, US Food and Drug Administration (FDA)