Pharmaceutical bottle packaging – the quest for zero defects and data integrity
Posted: 16 December 2020 | Iván Avilés-Segundo (Pfizer), José-Miguel Montenegro-Alvarado (Pfizer) | No comments yet
This article shares the results from an evaluation of a novel thermal imaging technology that took place before the initial implementation in a Pfizer manufacturing facility. The manuscript describes the technology and reviews the extensive process used to challenge its inspection capabilities through field testing. Finally, the potential benefits of adopting this first-in-class pharmaceutical technology as a new standard for non-destructive testing1,2 of bottle induction sealing integrity in the pharmaceutical industry is summarised.
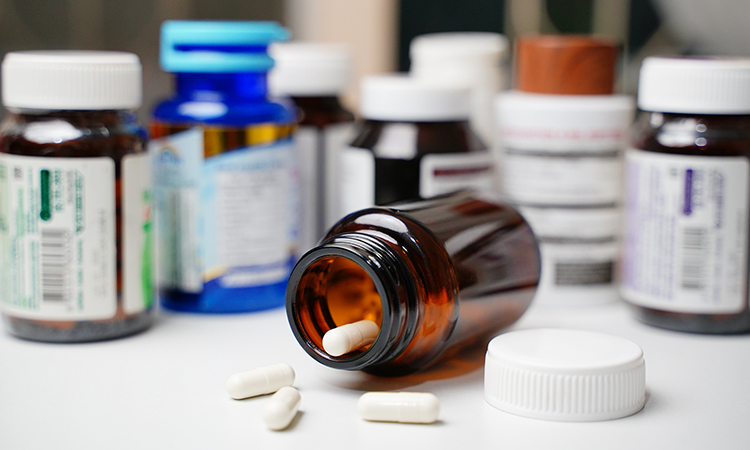
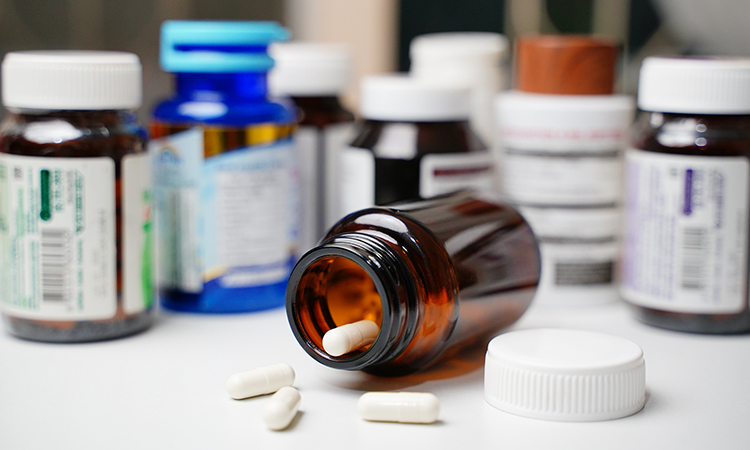
HIGH-RESOLUTION, cryogenically cooled thermal imaging technology was initially developed for military purposes. Furthering the commercialisation of the technology for civil applications, a pharmaceutical assembly – for high-speed and 100 percent inline verification of induction integrity in bottle packaging – was first developed and made available for testing relatively recently.3 This article summarises outcomes from initial plant feasibility work and extended rigorous proof-of-concept trials. The evaluation process resulted in the first Pfizer network implementation of the technology for the routine inspection of heat induction foil sealing integrity in a high‑speed bottle packaging line at a pharmaceutical manufacturing facility.
Background
The need to improve sealing inspection triggered a search for technologies resulting in the development of a new application of high-resolution thermal imaging”
As part of identifying continuous improvement opportunities for packaging processes, a request was made to enlist the top unmet technical challenges at a Pfizer manufacturing facility. The intention was to identify recurring issues and evaluate potential solutions. From an initial list, the top unmet technical requirement identified – based on criticality and occurrence – was related to customer complaints due to incomplete foil sealing in bottles. This is considered a critical defect because of its potential to negatively impact product integrity, stability and efficacy during the claimed shelf-life period.
In the past, there was no technology available to enable automated 100 percent inline inspection of foil sealing integrity through the caps for bottle packaging. Once the bottle was capped, the integrity of the seal could only be verified by removing the cap. Therefore, the seal integrity attribute relied on in-process testing based on a statistical sampling of bottles. Samples were manually handled, bottle caps were individually removed and foil sealing integrity was visually checked in an off-line fashion. When sealing issues were found, the path forward usually involved either increasing the overall number of samples for off-line inspection or arranging for 100 percent manual inspection of the batch as a separate unitary process. The latter significantly increased production cycle times and required a considerable amount of additional resources to execute. In addition, the risks for human errors and ergonomic issues grew during this labour‑intensive activity. The need to improve sealing inspection triggered a search for technologies resulting in the development of a new application of high‑resolution thermal imaging.
Apparatus and principle of measurement
The high-resolution thermal imaging apparatus implemented as a result of the evaluation described in this article is named Induction Integrity Verification System (I2VS) from DIR Technologies, Haifa, Israel*. From a high-level and general standpoint, this technology leverages black body radiation principles as it captures and visualises the electromagnetic radiation emitted by an object (or focus area thereof) of interest.
Implementation of the technology eliminates the need for sampling and off-line inspection, reducing operator interventions and potential human errors during visual inspection”
Electromagnetic radiation is emitted by warm bodies due to the thermally-induced motion of molecules.4,5 In principle, thermal imaging cameras detect the radiation emitted by objects at temperatures above absolute zero. The images generated – also known as thermographs – capture information on temperature variations, as the amount of radiation emitted by an object in the infrared spectrum increases with temperature.6 In practice, the radiation emitted at these wavelengths by objects can often penetrate most plastics.
In the specific application of bottle packaging, the sensing apparatus can capture the electromagnetic radiation contour emitted by the foil sealing ring through the polymer plastic caps. This enables the generation of thermographs of the covered foil that are not possible with visible light-based imaging systems. For this inspection application, the thermal imaging camera is positioned immediately after the induction sealing step above the conveyor belt that transports the capped bottles. After capturing the radiation patterns from the induction sealed foil ring of each bottle, the information is analysed in real‑time using high-speed image processing software. Pre-determined algorithms and adjusted threshold values for thermal pattern variability allow for discrimination and detection of a range of defects that end up impacting bottle foil seal integrity.
*DIR Technologies is no longer in business, but the intellectual property associated with this application has been sold to a third party.
Field evaluation of technology
During a search for an appropriate solution, it was found that a thermal imaging technology with the potential to inspect foil sealing integrity inline was being evaluated on some external technology forums at the time. However, there was limited information about its performance in a commercial high-speed production environment. The technology seemed promising, but there was a level of risk involved due to the uncertainty of its effectiveness as well as the level of capital investment required for full implementation. Ultimately, it was agreed with the vendor to collaboratively perform plant feasibility work to understand the technology’s capabilities and applicability to our inspection needs.
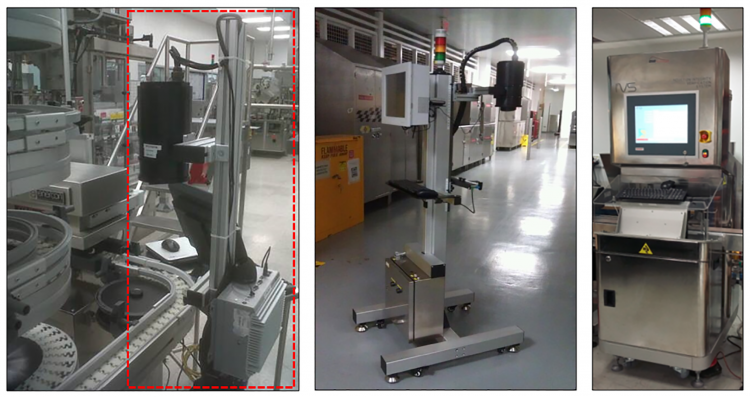
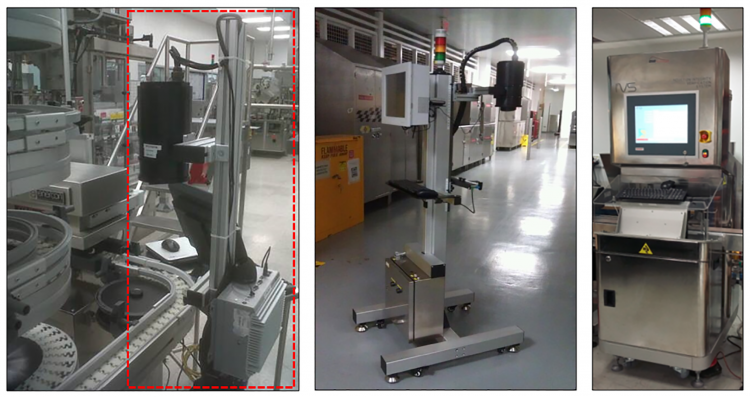
Figure 1: Left: Basic high-resolution thermal imaging assembly used for initial feasibility work. Middle: Field tester unit used for extended plant proof-of-concept trials. Right: Commercial system implemented in a high-speed bottle packaging line in a Pfizer manufacturing facility.
Feasibility work (Figure 1) was performed using a prototype system consisting of a thermal imaging camera mounted on a portable tripod and a computer with software to control the capture of the thermographs and conduct their evaluation. Empty bottles were used to test the system defect detection capabilities at this early stage. The study confirmed the equipment capabilities to identify a wide range of the typical bottle sealing defects observed in a pharmaceutical packaging environment. The results obtained in the prototype phase (Figure 2) were very promising, which led to a second phase for extended plant proof‑of-concept trials.
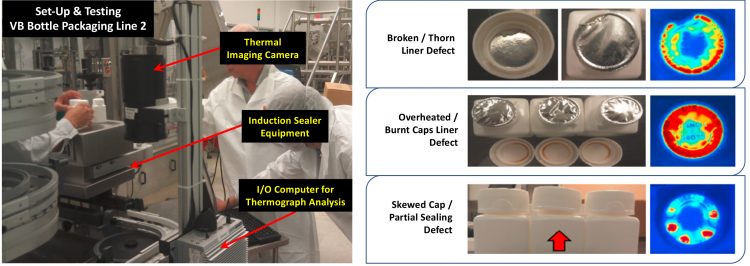
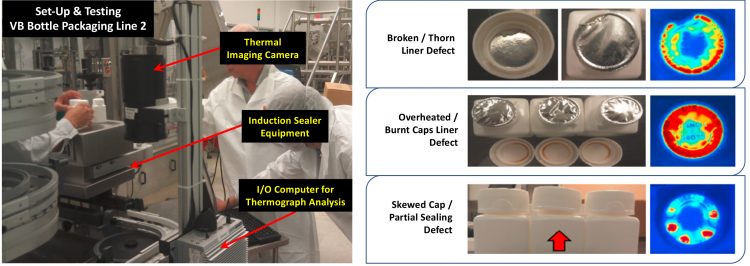
Figure 2: Left: Initial plant feasibility work performed in collaboration between vendor company, a Pfizer manufacturing site and Pfizer’s GT&E Manufacturing Intelligence team. Right: Sample defects consistently captured by thermal imaging system during initial plant feasibility work.
The second phase of the evaluation involved the installation of a portable field tester prototype to perform extended plant proof-of-concept trials during commercial production. The unit was installed at different packaging lines (Figure 3) with aims to cover most bottle/cap sizes and combinations, different types of closures (continuous thread, squeeze and turn, etc) and varying line conveyor speeds. The plan intended to thoroughly challenge the technology capabilities in a representative production environment – involving a significant period of time – to generate enough data on system performance, stability and ruggedness.
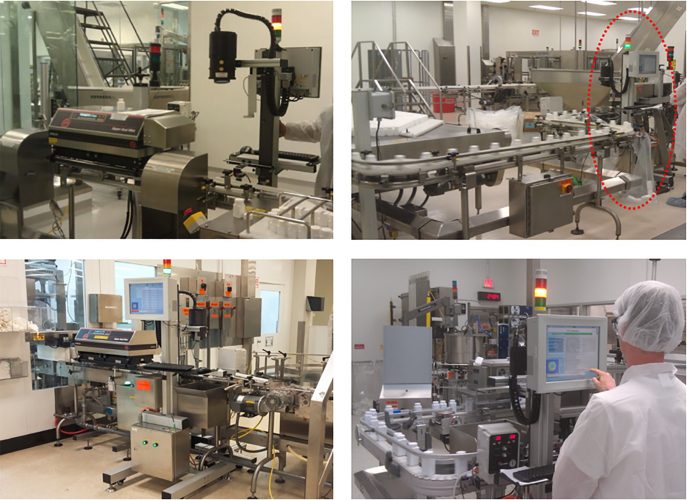
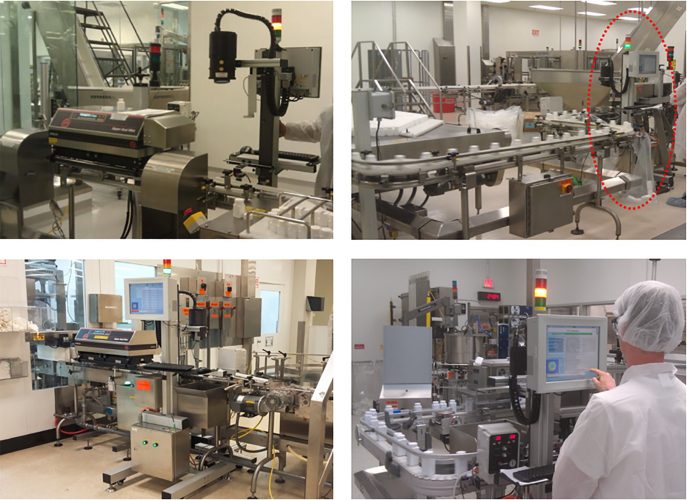
Figure 3: Thermal imaging field tester unit previously installed at four different packaging lines across two Pfizer manufacturing facilities during extended plant proof-of-concept trials.
The focused testing activities provided factual confirmation of the system’s detection and automated ejection capabilities for sealing defects resulting from broken and folded liners, under- and over-heated seals, high/unengaged caps, inverted foil liner and no induction (Figure 4) with a high degree of accuracy. It also provided inspection redundancy for defects such as skewed caps, which traditional checkpoint sensors have previously shown to occasionally fail to detect. These capabilities were later formally documented as part of the implementation cycle of the technology, including system acceptance tests (FAT/SAT) and validation (OQ/PQ).
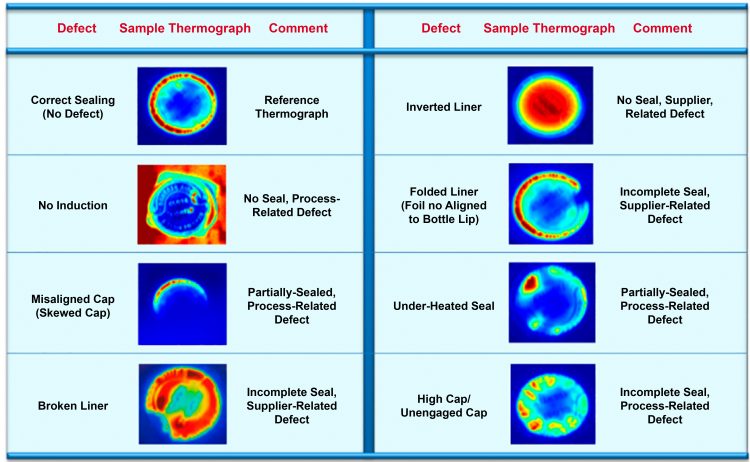
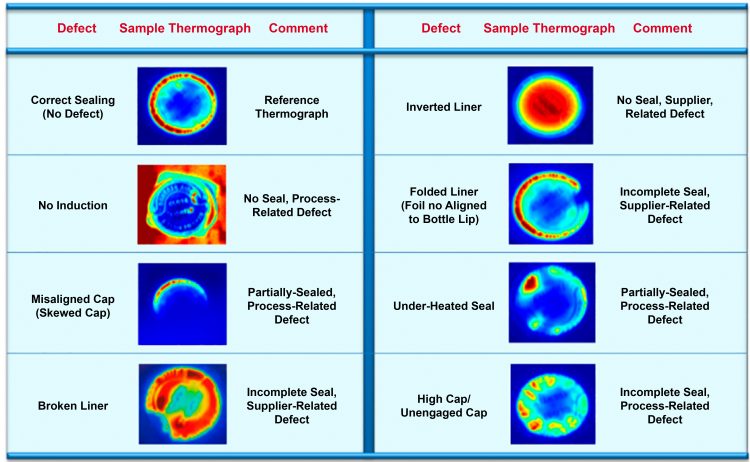
Figure 4: Summary of the defects consistently captured and sample thermographs from extended plant proof-of-concept trials with thermal imaging technology.
Benefits of thermal imaging technology
The implemented thermal imaging system provides numerous significant benefits. For example, implementation of the technology eliminates the need for sampling and off-line inspection, reducing operator interventions and potential human errors during visual inspection. Additionally, process improvements are realised from a data integrity perspective.
By enabling high-speed 100 percent inline inspection through the caps, the technology avoids defective products from reaching customers without increasing packaging cycle times. Improved process robustness means reducing defects and customer complaints, which cascades into cost avoidances due to fewer investigations.
At the operational level, the instant feedback provided by the technology can help to optimise the initial set-up of the capper and induction sealing machines. It can also be used to improve the set-up of dimension-based sensor assemblies at traditional checkpoints if the user decides to keep them for redundant detection capabilities. In addition, the technology can also help with early identification of the need for maintenance on these machines and/or sensor assemblies based on actual performance.
Furthermore, the thermal imaging system is capable of classifying the types of defects detected. This functionality aids during troubleshooting and can expedite root cause identification. Based on our experience, most defects are either process- or material-related. Monitoring and quantification of material-related defects can support evidence-based negotiations to request quality improvements from suppliers. Additionally, the immediate detection of recurrent defects also serves as early identification of process shifts that could be caused due to material variation or mechanical failures. Lastly, on a more strategic level, avoiding defects from reaching customers protects – and in the longer term may help improve – brand image.
Final remarks
This article shared the evaluation of a novel thermal imaging technology that resulted in the implementation of the technology at a Pfizer manufacturing facility (Figure 5). The technology’s capabilities were thoroughly challenged in a rigorous process that focused on field testing. The thermal imaging system consistently showed first-ever equipment capabilities to detect a wide range of induction sealing defects during bottle packaging with a high degree of accuracy. This manuscript also summarised some of the key benefits of this first‑in‑class pharmaceutical technology.
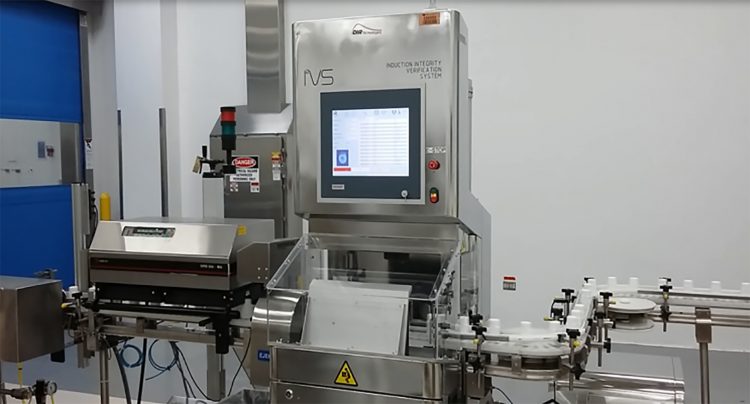
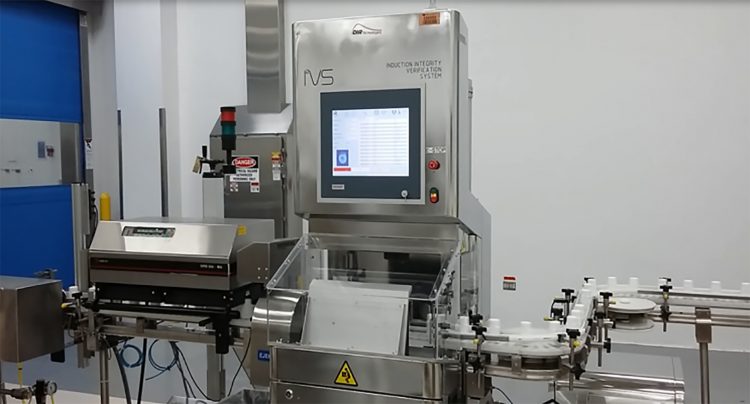
Figure 5: First Pfizer network implementation of Induction Integrity Verification System (I2VS) thermal imaging technology at a high‑speed bottle packaging line at a Pfizer manufacturing facility.
Bottle seal integrity has been historically tested by sampling a finite number of bottles and manually removing caps to visually inspect foil seal off-line as an in-process verification during the packaging process. Traditional technologies cannot directly inspect the quality of the sealing in an inline fashion. In the authors’ view, the capabilities of this new high-resolution thermal imaging technology provide a tangible and disruptive improvement to inspection that raises the bar for quality assurance and has the potential to become the new standard for the verification of induction sealing integrity in the pharmaceutical industry.
Acknowledgements
Many colleagues were directly and indirectly involved in supporting the activities described in this article. Since the list is too long to mention them individually, the authors prefer to collectively thank the Pfizer network of technical colleagues, as well as vendors and contractors, that collaborated to realise this work.
About the authors
References
- Meola, C.; Boccardi, S.; Carlomagno, G.M. (2017). “Chapter 4 – Non-destructive Testing with Infrared Thermography”. Published in Infrared Thermography in the Evaluation of Aerospace Composite Materials, Woodhead Publishing (2017), pp. 85-125. Electronically retrieved on September 12, 2020 from ScienceDirect website at https://www.sciencedirect.com/science/article/pii/B9781782421719000048.
- RELIABILITYWEB.COM (N.S.). Beyond the Usual Applications for Infrared Thermography. Electronically retrieved on September 11, 2020 from RELIABILITYWEB.COM website at http://reliabilityweb.com/index.php/articles/beyond_the_usual_applications_for_infrared_thermography/.
- Montenegro-Alvarado, J.; Diehl, B.; Guay, J.M.; Hammond, S.; Isaac, H.; Lyons, B.; McSweeney, C.; O’Neill, S.; Simard, J.S.; Timmermans, J. (2014). “PAT for Packaging: Review of Applications for Expeditious, Non-destructive Quality Testing”. Published in European Pharmaceutical Review, 19(2), April 2014.
- StackExchange (N.S.). Physics: Why do moving particles emit thermal radiation? Electronically retrieved on September 11, 2020 from physics.stackexchange.com website at https://physics.stackexchange.com/questions/72174/why-do-moving-particlesemit-thermal-radiation.
- Encyclopaedia Britannica, Inc. (2020). Electromagnetic radiation. Electronically retrieved on September 11, 2020 from Encyclopaedia Britannica website at https://www.britannica.com/science/electromagnetic-radiation/Continuous-spectra-of-electromagnetic-radiation.
- BBC (2020). Black body radiation. Electronically retrieved on September 12, 2020 from BBC Bitesize website at https://www.bbc.co.uk/bitesize/guides/zshgqhv/revision/1.
Issue
Related topics
Drug Manufacturing, Manufacturing, Packaging, Production, QA/QC