A glimpse at how Novartis’ manufacturing and supply organisation responded to COVID-19
Posted: 28 August 2020 | Steffen Lang (Novartis) | No comments yet
The rapid evolution of the COVID-19 situation has created significant barriers to normal operations, from locking down borders to the imposition of restrictions on trade and export – not to mention a surge in demand for many common medicines. Each of these events in isolation can affect production and supply, but together they represent a huge challenge in ensuring patients receive their medicines on time. This article examines how Novartis prepared for the challenges of COVID-19 and managed global operations with minimal impact.
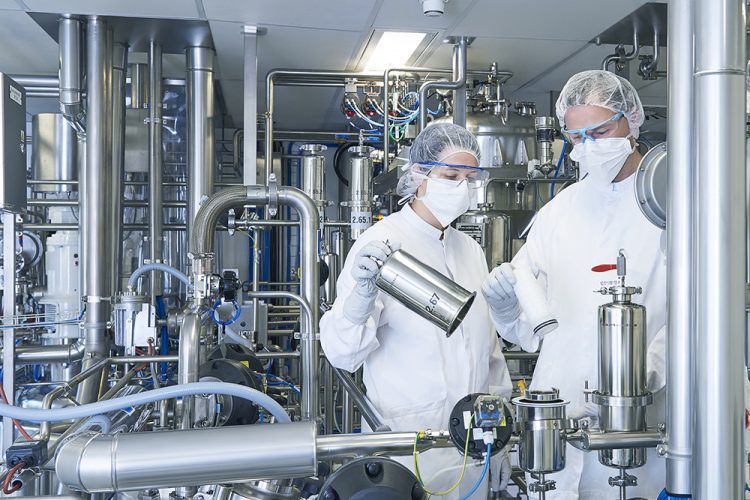
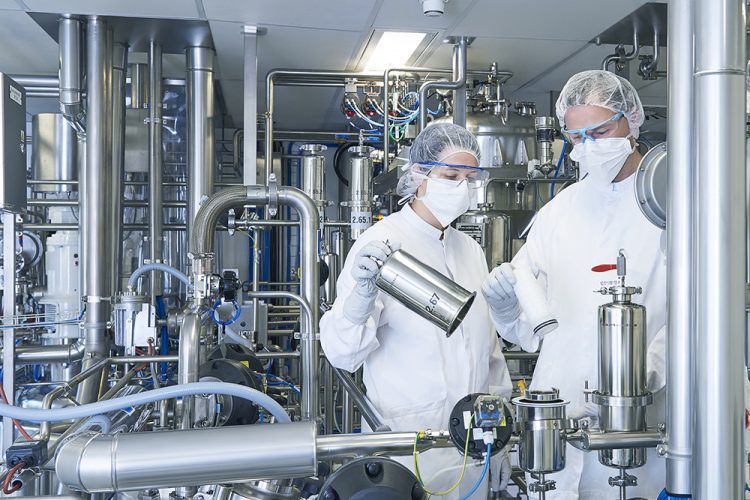
How do you ensure the continuity of your manufacturing and supply service for your patients in the face of a global pandemic? How do you stay ahead of the curve and ensure your strategy is not beholden to the whims of a “second wave” or regional outbreak? Finally, how, in the case of global pharmaceutical company Novartis, do you balance your priorities – of combating the crisis with ongoing trials and work to safeguard against future possible pandemics? The answer is as simple as it is complex: you combine a proactive strategy with decisive action plan for disruption of some kind, with existing mechanisms in place to help navigate through the storm.
Novartis has been able to mitigate the challenges presented by COVID-19 and manage global operations with minimal impact. At Novartis Technical Operations (NTO), the global manufacturing and supply network of Novartis, it helped that preparations pre-dated the pandemic.
Starting early, acting promptly and being decisive
In supply and replenishment planning, the company balanced demand with supply at optimised inventory levels. The target is to be able to react almost in real time to market demand changes by utilising applications and systems that support quick scenario planning and recommendations, as well as outcome predictions.
NTO has an established risk, business continuity and supply risk management framework that remains active throughout the year. At the heart of its COVID-19 response was an NTO taskforce that tracked real-time information from several sources and quickly took action to ensure supply to patients. The team examined product supply, internal and external dependencies, risk management and more.
The business continuity and pandemic preparedness plans were brought into force at the first warning sign and the number one priority was safeguarding the health and wellbeing of the organisation’s people. Overnight, plans were devised to reduce the number of employees required to be on site. For those needed on site, immediate safety measures were taken including adapting working patterns to avoid interaction between shifts, virtual shift handovers and having defined exit paths in case of any symptoms. In addition, surgical masks were distributed to offer further personal protection. Aside from a small number of cases where local authorities required sites to close temporarily, all sites remained operational during the pandemic. In some cases, where transport to sites was problematic, arrangements were made for essential staff to stay on site or in a nearby hotel.
For those with critical on-site roles, additional options were offered, including help with childcare and extra leave days. Shift patterns were adapted to ensure working couples could co-ordinate and manage work alongside their responsibilities at home. The company also offered free access to learning platforms for employees’ family members to help occupy the many hours at home. Employees also stepped forward, volunteering to help in production and collaborating outside work to support each other’s families. The commitment of Novartis’ people has helped maintain the continuity of manufacturing and supply, while keeping colleagues safe.
The business continuity and pandemic response plans additionally included maintaining robust inventory levels and “dual supply points”, which provided significant flexibility. Substantial inventory levels of finished products have been vital throughout the entire value chain.
Across the network, teams and facilities have mobilised our teams and facilities to respond to the demands of the situation – both in the organisation and the broader community. At Stein in Switzerland, the Novartis Cell and Gene Therapy team redeployed associates to fill 40,000 vials for urgently needed COVID-19 testing kits. At Mengeš in Slovenia, the team prepared and bottled over 32,000 litres of 70 percent isopropanol for disinfection purposes, almost 25,000 litres of which was for donation to the local community and the remaining for Novartis’ Slovenian sites. One of the sites in the US began manufacturing hand sanitiser for internal use and donated more than 27,000 units to the New York administration.
Being prepared for the ‘what comes next’
Preparedness always means keeping one eye on the future. To that end, work has begun to establish a supply chain and procurement collaboration to create a fully automated e-source solution, which will mitigate freight cost increases. This is to ensure the company has the capacity to track medicines in the supply chain as part of an ambitious data and digital transformation plan. This has already enabled the business to quickly introduce a new digital tool to track personal protective equipment (PPE) stock across the world.
Across the business, there are examples of how technology is being used to transform medicine – and it is precisely this view to the future that allows them to stay ahead. Last year, for example, Novartis and Microsoft announced a collaboration to transform medicine with artificial intelligence (AI). The move was seen as an important step in the company’s mission to reimagine medicine. The lab aimed to leverage the power of AI in the desktop of every Novartis associate and brought together vast amounts of Novartis datasets with Microsoft’s advanced AI solutions.
Last year also saw Novartis enter a strategic collaboration with Amazon Web Services. The cloud services will help to build an enterprisewide platform putting real-time data and analytics in the hands of associates, thus empowering them to make improved business decisions and increase efficiencies across manufacturing processes and the supply chain.
Moving forward, Novartis is actively working with suppliers to maintain end-to-end visibility on the supply chain through greater digital investment. The company is also simplifying and digitising the demand planning process by using predictive analytics and AI to generate forecasts. Novartis believes that the more of the organisation to optimise and go digital, the better prepared the company is to manage vulnerable situations.
Ultimately, the business continuity preparedness, existing infrastructure, cohesive global team and strong relationships with suppliers came together to enable the business to continue making and supplying medicines to patients worldwide despite the challenging situation. Nobody wished for this situation, but it has presented the opportunity to accelerate digitilisation and ramp up the company’s remote working infrastructure which, in turn, has made the business more resilient for the future.
About the author
Steffen Lang has been Global Head of Novartis Technical Operations (NTO) since 2017. He is also a member of the Executive Committee of Novartis. Prior to his current appointment, Steffen served as Global Head of Biologics Technical Development and Manufacturing within NTO from 2015 to 2017. Steffen holds a doctorate in pharmaceutical technology from the Swiss Federal Institute of Technology in Switzerland and a master’s degree in pharmaceutical sciences from the University of Heidelberg in Germany.
Issue
Related topics
Artificial Intelligence, Drug Manufacturing, Gene therapy, Industry Insight, Supply Chain, Viruses