Temperature-controlled packaging
Posted: 27 February 2019 | Andrew Meyers - Global Director Cold Chain Consultants Ltd | No comments yet
Andrew Meyers has travelled across many countries designing, auditing, investigating and correcting failures in temperature supply chains. In this article he explores some examples of his observations from the field.
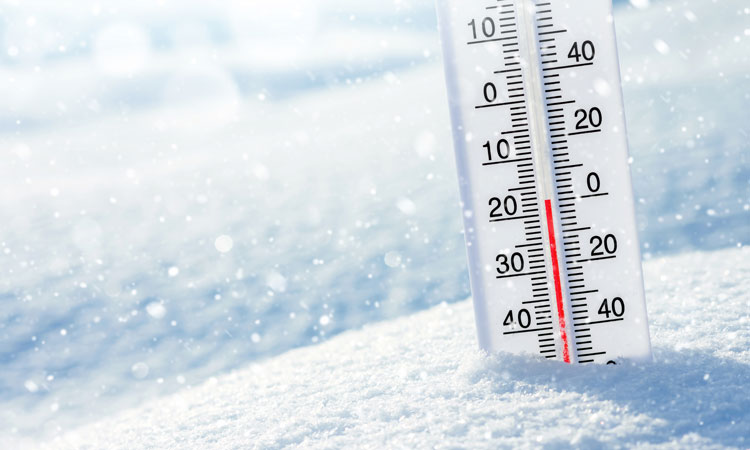
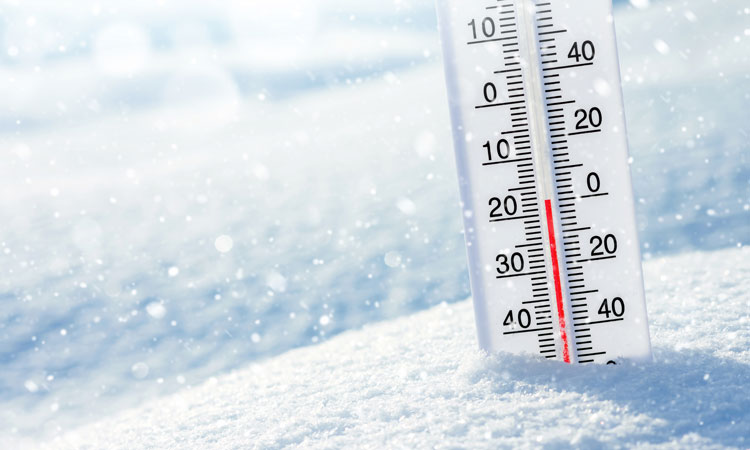
One of the most challenging supply chains involves shipping temperature-controlled products from origin to destination whilst maintaining product temperature. Normal supply chains have many variables to control or manage to ensure a successful outcome; however, when temperature control is included another 30 to 40 variables add to the complexity.
Temperature-controlled packaging is a critical part of the temperature supply chain, but is often underestimated. It comprises many components, which all must interact in the way they were designed to for temperature to be maintained. Many factors impact product temperatures and duration, including heat transfer by convection and conduction, changing external temperatures, differing conditioning requirements, masses of different temperatures trying to equalise, ice packs and phase change materials (PCM).
The laws of physics
In simple terms, cold chain packaging is a box of physics and you cannot cheat the laws of physics. Assuming the packaging is suitable for purpose, there is one other major factor to consider – the complexity of the human factor. From my observations, the human factor is often the most challenging and weakest link in the chain.
For someone not experienced in cold chain packaging there is a simple way to start a decision-making process for selecting the correct packaging. Begin with a simple comparison table of packaging from multiple suppliers with similar dimensions to suit the purpose, entering the advertised data from packaging companies.
Compare the following from each company:
1) Type of insulation
2) Thickness of insulation
3) Total weight of phase change or ice packs
4) The qualified times.
Group the data into insulation types and start comparing each packaging data. You will generally observe patterns of the similar size packages with similar thickness and type of insulation use, a similar number of ice packs or PCM. It is important to only compare similar insulation materials and similar thicknesses, as vacuum insulated panels (VIP) will provide significantly better insulation and cannot be compared with other insulation materials of the same thickness.
If you observe similar size packaging using significantly less ice packs or PCM, then investigate the qualification before discounting them. The stored energy necessary to maintain the temperature is due to the cooling packs and if there are significantly fewer, the qualification should be investigated.
One major misconception is that the insulation prevents the heat entering the packaging. It does not stop heat entering the temperature-controlled packaging, it merely slows down the rate of heat transfer. After testing thousands of cold chain packages over the past 15 years, I can confidently state that you cannot cheat physics or chemistry.
For example, I often observe thin low-density polystyrene packaging being used to transport healthcare products with a few ice packs on top. In a recent case, there were four x 600g ice packs used on top of the product. When I queried the qualification, I was informed it was qualified for 64 hours at temperatures up to 40°C. Doubting this qualification, I requested a copy and to date have never received confirmation of performance. A thin wall polystyrene low-density packaging will allow heat to transfer within 5-10 minutes. After this time the cooling medium, either ice packs or PCM, are the main elements maintaining the temperature of the product. There is insufficient energy stored in four x 600g ice packs to maintain the temperature for 64 hours.
Changing temperatures
In qualifications that represent actual supply chains with continuously changing temperature segments it can often be observed that the internal temperature of the packing will rise and fall in a similar pattern to the external ambient temperature. The lag in the internal profile is due to the insulation type, quality and thickness slowing down the heat transfer.
There are some cycling profiles published on the internet that should be treated with caution. These often claim that packaging is qualified, for example, for +40°C to -10°C. The profiles cycle between high and low temperatures, and the internal temperatures follow a similar pattern without exceeding the limits. Firstly, these profiles do not represent any actual supply chain profiles. Secondly, the external temperatures can be manipulated and cycled to control the internal temperature. You should be aware of these types of qualifications and I recommend conducting your own testing.
The most important part of investigating thermal packaging is to understand how the qualification was performed. When selecting packaging, it is important to request details from suppliers regarding what products or placebos were used in the qualification. Many times, when investigating failures, the packaging was qualified with ½ pint or 500ml bottles of water with immersed probes, when the company is shipping low mass vaccines 2-4ml, or small vials which have a small mass and change temperature more quickly. GMP qualification requires to test to worst-case scenario – and the surface of the product is generally the worst case – and specifies where the temperature measurements should be taken.
It is critical when reviewing thermal packaging qualifications that the raw data from the qualification is checked to ensure the data does not have a delay in recordings after packing. In many cases the practice of delay in temperature recording of up to two hours is justified in the procedure or qualification as this is the time it takes for the packaging to acclimatise and balance the temperatures. In audits of temperature supply chains, the first few hours after packing are the most common time when excursions are recorded, and product quality is compromised with temperatures often far below zero degrees.
Travel through your supply chain
Once the correct packing is selected you cannot assume the product will be transported throughout the supply chain correctly. From end-to-end auditing of supply chains, which very few companies conduct, the reality of the temperature supply chain is vastly different to what is assumed. Implementing procedures and reviewing quality systems in an audit does not guarantee that the products will arrive at the destination with the efficacy maintained. To truly understand the temperature supply chain, go for a ride with the thermal packaging – follow it through the supply chain checking what occurs at every point. By travelling through your own supply chain and stopping at each point at which humans are involved you will gain the transparency and understanding of the root cause of most failures and excursions. I’m certainly not suggesting that humans intentionally sabotage the supply chain, but there is a general awareness that they need to care for thermal packaging in transit and most problems are due to a lack of knowledge, training, supervision or understanding. Investing time in training, knowledge, education, supervising procedures and knowledge can easily correct most excursions. It’s the old case of “they only know what they know, and they are trying their best with what they know”, which can often be based on incorrect information or assumptions.
In general, the primary supply chain from many good quality factories in developed and developing countries performs exceptionally well. Unfortunately, a large percentage in all markets damage the products within the first few hours. This is mainly due to poor packaging designs, lack of qualification, the wrong packaging selections, untrained staff or a lack of understanding of general cold chain packaging and procedures. In many observations the price of qualified packaging is a barrier and budgets are continuously reduced or are limited.
The products leaving the factory cannot be made any better, especially with GMP manufacturing standards ensuring quality and efficacy. However, the quality and efficacy can certainly be compromised very quickly within the supply chain, effectively wasting the time, care and money expended to produce them.
The other barrier is that employees cannot go to management and inform them their supply chain is failing to maintain temperature, for fear of losing their jobs. In some cases, I have collected data and presented audit reports, only to have them shredded in front of me. Other requests have insisted I deliver a word copy of the files for review and correction, which I delicately decline to provide.
The further along the temperature supply chain I travel the more I observe procedures not correctly implemented, or changes to procedures that impact the products. In a recent review of a supply chain through a distribution network, we observed more than 50 percent of clinical trial materials exceeded temperatures below zero for long periods of time within 2-8°C shipments. In several of the transport segments dry ice was used to keep the products cold as the operations received complaints that products had previously arrived warm. They were aware cold chain products needed to be kept cold and by using dry ice the products always arrived at their destination cold.
Cost savings
One operator showed me how much money could be saved by reducing the packaging cubic size and weight by using dry ice instead of ice packs and he never received complaints that the cold chain products were warm. Conducting the trial in a developing market, this may have been more economical; however, the real cost to the sponsor who spent millions developing the products may have been much greater. The results of the clinical trial possibly stopped the product advancing further.
As shocking as it may seem, I have on multiple occasions in developed markets, witnessed similar practices where additional ice packs are added to packing configurations by operators without any qualification following complaints that the products arrived warm. If a product arrives warm in most of my observations it is recorded, reported and rejected. If a product arrives in packaging cold, it is assumed the cold chain has been maintained and the product is suitable for use. However, when products have been frozen, which will generally affect efficacy to a greater extent than heat, they are rarely detected. There is still a long way to go in educating staff about the temperature controlled end-to-end supply chain and use of qualified thermal packaging.
I leave you with an interesting thought and perception from a transport operator. On one occasion I observed a truck driver rolling a heavy cold chain package down the length of his truck like a ball. I immediately shouted, “Hey, that’s an expensive medical delivery probably worth thousands of dollars.” He stopped, looked me in the eye and loudly stated, “To me it’s a $20 delivery,” before continuing to roll the package.
Biography
Andrew Meyers is the managing director and founder of global pharmaceutical cold chain consulting company, Cold Chain Consultants. Andrew has studied all aspects of cold chain and temperature sensitive supply chains for over 15 years, specialising in the pharmaceutical industry. He has conducted more than 4,000 qualifications and temperature supply chain audits.
He has worked extensively within the operations of transport, warehousing and distribution of pharmaceutical temperature sensitive supply chains and has a wealth of practical hands-on knowledge and experience.
Andrew and Cold Chain Consultants have provided services to over 300 global clients including Dr Reddy, Cipla Pfizer, Lilly, Pfizer, Unicef, CSL, Alcon, Bristol Meyer Squibb, Blood Service, Abbott, Alcon, Amgen, Military, Ambulance, Air Rescue, Expeditors, Toll and DB Schenker
He has held several director positions and served on various boards and committees including the SCLAA (Supply Chain Logistics Association). He has lectured and conducted cold chain and GDP practical training courses and workshops throughout the US, Asia/Pacific, Europe and Australia, with an operational focus for the pharmaceutical and life science industries.