Development of novel water-soluble inks for 3D-printed polypills
Posted: 23 May 2024 | Catherine Eckford (European Pharmaceutical Review) | No comments yet
An “innovative formulation and printing process” utilising 3D-printing could lead to scalable batch production of personalised pharmaceutical tablets, research suggests.
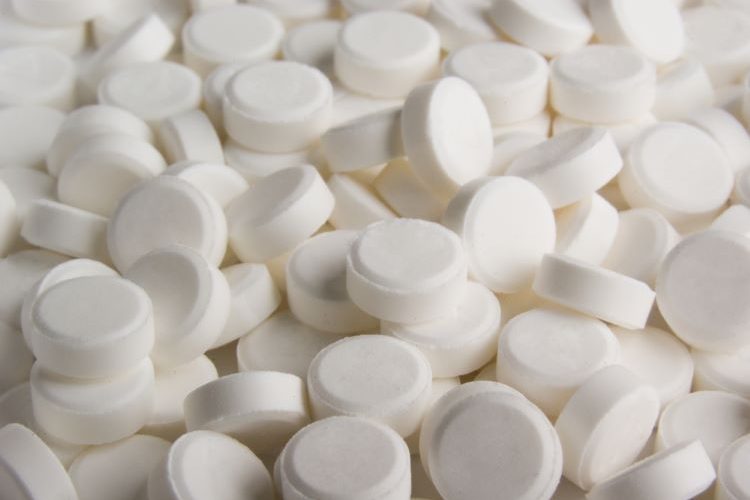
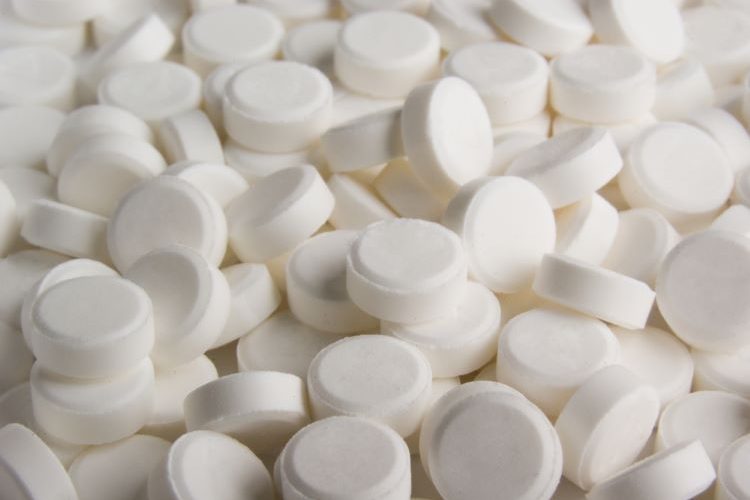
A paper has reported a multi-material ink-jet 3D printing (MM-IJ3DP)-based method that could enable tailored drug release profiles of personalised pharmaceutical tablets during manufacturing.
While biocompatible water-soluble polymers as excipients, have “been recently explored to produce gels [they have not been investigated] as a water-soluble excipient”, according to the paper.
Benefits in manufacturing
The authors illustrated MM-IJ3DP using a novel formulation of a soluble polymer, to enable for the first time, Noyes–Whitney release rates to be programmed and modulated through digital design and manufacture.
Design of the pill meant that the drug release and dosage timing of individual active materials were controlled by geometrical design”
Specifically, in the study, individual water soluble and insoluble materials were “co-printed within a design envelope to dial up a range of release rates including slow, fast and multi-stepped dissolution curves”.
Design of the pill meant that the drug release and dosage timing of individual active materials were controlled by geometrical design, the authors stated.
Importantly, the MM-IJ3DP technique explored in the paper enables “unprecedented control of multimaterial design opportunities to enable the control of dosing and release rate without an increase in the overall tablet size”.
New avenues in personalised tablet formulation
In the study, a photo-polymerisable acrylomorpholine (ACMO) formulation combined with aspirin demonstrated potential as a new water-soluble carrier.
As a scalable additive manufacturing process, MM-IJ3DP can offer “unprecedented opportunities for accessing personalised drug delivery compositions, and consequently drug release profiles” not possible via conventional manufacturing, the paper suggested.
The findings highlight the potential of personalised printed polypills with release rates that are “easily programmed through their 3D-printed structure”.
Rivers et al. concluded that the advantages MM-IJ3DP for “in-batch manufacturing of different designs, combined with the controlled release of the active pharmaceutical ingredient (API) demonstrated here, offer realistic opportunities for advanced pharmaceutics manufacturing and personalised medicines”.
This paper features in the June 2024 issue of the journal Materials Today Advanced.
Benefits of 3D printing for personalised medicine formulation
Related topics
Active Pharmaceutical Ingredient (API), Drug Manufacturing, Excipients, Formulation, Industry Insight, Personalised medicine, Research & Development (R&D)