How to approach die plate adhesion during tableting
Posted: 23 October 2023 | IMA Pharma | No comments yet
A study by IMA and Labomar has illustrated a gentle but effective approach for achieving defect-free tablets and an adhesion-free die plate.
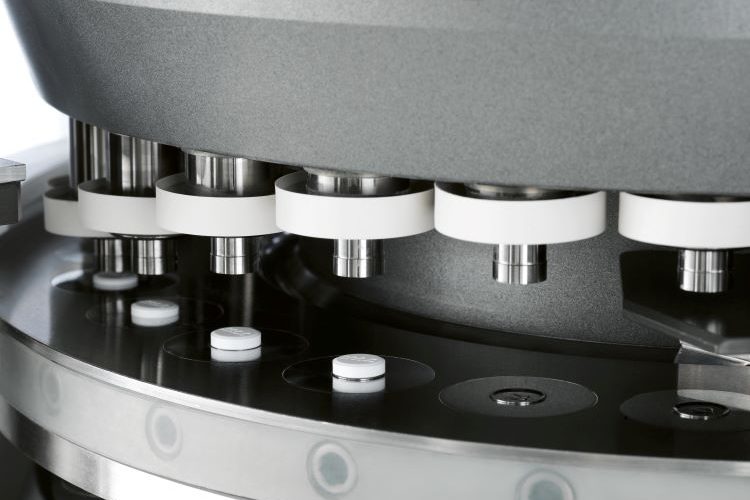
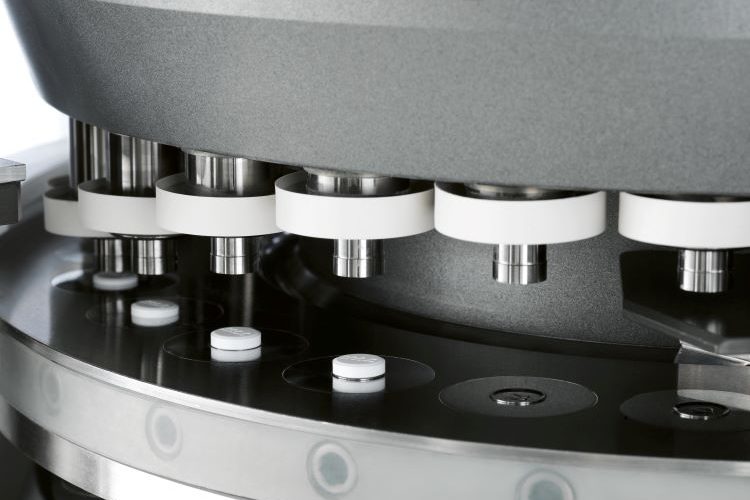
Credit: IMA Pharma
In tablet compression, there are a range of factors which contribute to a successful production run.1
In pharmaceutical manufacturing, the high level of final product quality is the major driver. Tablets should be defect-free and compliant to good manufacturing practice (GMP) aspects and final-user requirements.
The most common defects in tableting are classified as visual or functional2: visual issues compromise tablet quality without affecting its functionality, something which functional issues affect, such as API availability.
Troubleshooting the tableting process
The key to properly managing troubleshooting of the tableting process is to thoroughly investigate the causes of the defects: mostly, it can be approached by exploring the physical-chemical features of the formulation, the selected tableting process parameters or equipment wear even including tablet press parts such as punches and dies.
In most cases, formulation compounds represent a fixed starting point from which any changes can be implemented, whereas tableting process parameters as well as machine condition, can be managed and optimised to their best, combining the knowledge of the machine manufacturer with the experience of the pharmaceutical industry. Stickiness is one of the crucial issues to be faced: it generally happens because, during tableting, powder may stick to the part in contact with the product.
Generally, stickiness occurs on punches and dies since they are directly concerned by the tableting process. Die-plate adhesion occurs in specific conditions.
Excessive quantities of fine particles in the formula, incorrect environment control or compounds with low melting points, eg, sugar derivates are all possible causes of stickiness on the die plate. The inner heat generation during the process (force application and friction below scrapers and feeding system) accelerates adhesion in products with the aforementioned properties.3
In this case, the standard approach used to solve sticking on punches and dies is palliative: providing a higher quantity of lubricant, introducing external lubrication4 or specific punch-tip coatings do not improve the final outcomes.
A collaborative study between IMA and Labomar has demonstrated optimisation of the die-plate adhesion phenomenon, resulting in defect-free tablets when working with a sticky blend. Production output was also optimised.
Tableting study – materials & methods
In this study, a sticky formulation of a chewable tablet was optimised; the latter includes a probiotic and a prebiotic (oligosaccharides – OS) as active ingredients, with the function of promoting the balance of the intestinal flora, and polyols as fillers, due to their good flowability, their high solubility and their sweet taste.
Prebiotics are defined as a “non-viable food component that confers a health benefit on the host associated with modulation of the microflora”.5 OS are dietary fibres, ie, carbohydrate polymers with a ≥3 degree of polymerisation, that are not digested or adsorbed in the intestine; rather they are fermented by the gut microbiota producing energy for their survival.6 OS present in the formulation is a fine powder that is highly hygroscopic and presents a low melting point because of its sugary nature.
Polyols, also defined as polyalcohols or sugar alcohols, are typically derived from hydrogenation of sugars (mono-, di- or polysaccharides)7, for this reason they generally appear to be moderately to highly hygroscopic powders. Polyols present in this formulation are characterised by a melting point ranging between 90 and 110°C.
Table 1 summarises the qualitative composition of the formulation, while Table 2 shows the tests and related methods performed on the mixture.
Active Ingredient (A) / Excipient (E) | Description | Percentage (%) |
A | Probiotic | < 5 |
A | Prebiotic | > 25 |
E | Polyols | > 60 |
E | Lubricant | > 0,5 |
E | Flavours | as required |
Table 1: Qualitative and quantitative composition of the mixture.
Test | U.M. | Method |
Particle Size Distribution (PSD) | µm | Laser diffraction particle size analyser Analysette 22 equipped with a Ø 1.5 mm funnel (Fritsch GmbH MicroTec plus / NanoTec plus, Idar-Oberstein, Germany). |
Water activity | / | Lab touch – aW SYSTEM (NOVASINA, Lachen, Switzerland) |
Loss On Drying | % | 5 grams, 80°C, 10 minutes (i-THERMO 163 M, 64M) |
Density | g/ml | Italian Pharmacopoeia XII ed |
Carr Index (CI) | % | Italian Pharmacopoeia XII ed |
Table 2: Test and related methods performed.
A PREXIMA 300 rotary tablet press was used for process optimisation. The machine was equipped with a Euro-D turret hosting 27 stations with round Ø 14.5mm punches. The feeder installed had two paddles inside with a flat geometry and a loading cam of 12mm was selected. The distance between feeder and die plate was 0.05mm, as a good starting point.
In this condition, stickiness on the die plate was evident (Figure 1) generating defects on the tablets themselves: in detail, a darker spot appeared on the surface due to the residual powder that was recovered by the machine and compressed again.
To manage this issue, approaches were made at different levels (Table 1):
- Loading cam
- Feeder geometry
- Distance between die plate and feeder.
TABLETING PROCESS PARAMETERS | VALUES | |||
Loading cam (mm) | 8 | 12 | ||
Feeder geometry (-) | Flat-Flat | Flat-Round | ||
Distance Feeder-Die plate (mm) | 0.05 | 0.10 | 0.12 | 0.15 |
Table 3: Tableting process parameters investigated during troubleshooting.
To evaluate the efficiency of the adjusted parameters, the most important tableting process responses (main compression force and its relative standard deviation, output reachable without defect, time of defect occurrence) as well as the tablets’ visual aspect were evaluated (Table 4).
PARAMETER | U.M. | VALUE | ||||
Test | – | 1 | 2 | 3 | 4 | 5 |
Paddle profile | – | Flat-Flat | Flat-Round | Flat-Round | Flat-Round | Flat-Round |
Loading cam | mm | 12 | 8 | 8 | 8 | 8 |
Main compression force | kN | 23 | 22.5 | 22.6 | 24.2 | 24.4 |
CF standard deviation | % | 7 | 4.3 | 4 | 3.8 | 3.7 |
Turret speed | rpm | 30 | 15 | 20 | 25 | 25 |
Production output | tph | 48600 | 24300 | 32400 | 40500 | 40500 |
Distance feeder-die plate | mm | 0.05 | 0.05 | 0.1 | 0.12 | 0.15 |
Good tablet appearance | (Y/N) | N | N | N | N | Y |
Time of defect occurrence | Y/N (min) | Y,2 | Y,10 | Y,30 | Y,60 | N |
Table 4: Tableting process responses and tablet appearance.
Results & discussion
Tests described in Table 2 were performed to evaluate the technological properties of the mixture and therefore examine die-plate adhesion phenomenon.
Results of these analyses are included in Table 5.
Test | U.M. | Results |
Particle Size Distribution (PSD) | µm | D10= 0,7 D50=17,8 D90=295 (*Figure 2) |
Water activity | / | 0.223 |
Loss On Drying | % | 0.78 |
Bulk density | g/ml | 0.67 |
Carr Index (CI) | % | 13 |
Table 5: Results of powder characterisation tests.
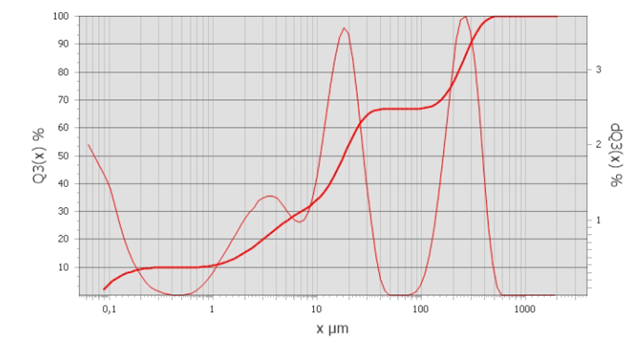
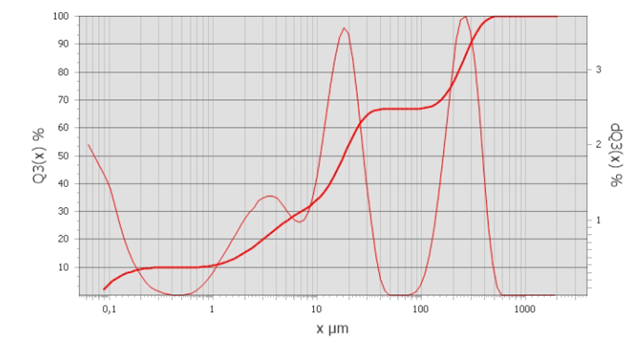
*Figure 2: PSD graph of the mixture and its cumulative oversize curve. X µm: particle size in µm Q3 (X) %: Cumulative PSD percentiles dQ3(x)%: Density distribution
Data from the investigation suggested that formulation compounds caused the stickiness on the die plate. Oligosaccharides (OS) tended to melt if they underwent excessive friction (with heat generation as a consequence) inside the feeder and between feeding system and die plate.
The approaches explored allowed for gentler handling of this compound, producing less friction and heat generation.
Having a round profile on the paddle at the right position inside the feeder smoothly scraped the extra powder dosed inside the dies, whereas a smaller loading cam reduced the powder dosed back inside feeder. The combination of these two parameters reduced powder movement inside the feeder, a factor that could concur in heat generation.
The most important process parameter managed was the distance between the feeder and the die plate: increasing this value so it was comparable with the particle size distribution of the blend allowed for a gentle passage of the powder below the feeder without generating friction and heat.
The outcome was defect-free tablets and a perfectly clean die plate without any adhesion.
Conclusions
Troubleshooting in die-plate adhesion is generally challenging because of formulation characteristics.
Gentler blend management was the lynchpin to reduce the possibility of generating friction and heat: round paddle geometry, reduced refilling inside the die feeder and distance accurately studied according to particle size distribution allowed for process optimisation that stabilised the overall tablet press efficiency and quality of the tablets.
Authors
Federica Giatti, Process development Laboratory at IMA Active, Ozzano dell’Emilia, Italia
Elena Ammoniaci, Pharma Technology Department, Labomar, Istrana (TV), Italia
Margherita Savio, Pharma Technology Department, Labomar, Istrana (TV), Italia
Caterina Funaro, Process development Laboratory at IMA Active, Ozzano dell’Emilia, Italia
References
- Kirsch D. Fixing Tableting Problems. Pharmaceutical Technology. 2015; 39(5)
- Tablet Resolution Handbook, 2014
- Adhnikart B, Bhandanrt B, Howers T, Truong V. Stickiness in Foods: A Review of Mechanisms and Test Methods. International Journal of Food Properties. 2001; 4(1), 1-33
- Giatti F et al., External lubrication application on a double-side rotary tablet press: how to set up the equipment and minimise time losses. [Internet] IMA Pharma. [cited 2023Oct]. Available from: https://ima.it/pharma/paper/external-lubrication-application-on-a-double-side-rotary-tablet-press-how-to-set-up-the-equipment-and-minimise-time-losses/.
- FAO Technical Meeting on Prebiotics, Rome. 2007
- Davani-Davari D, Negahdaripuor M et al. Prebiotics: Definition, Types, Sources, Mechanism, and Clinical Applications. Foods. 2019
- Grembecka M. Sugar Alcohols. Encyclopedia of Food Chemistry. 2019; 265-275
Related topics
Active Pharmaceutical Ingredient (API), Drug Manufacturing, Ingredients, Particle Sizing, Processing, Production, QA/QC